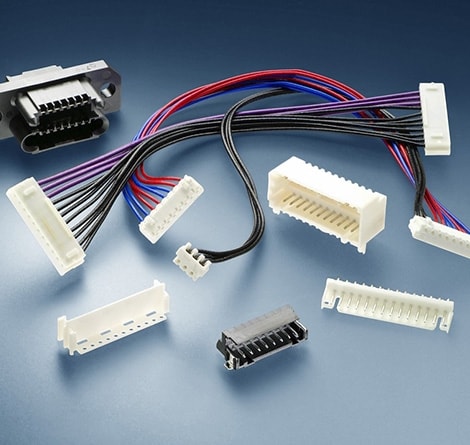
Reliable Connectors, Plugs, Wire & Cable Assemblies for a more Connected World
TE's AMP family of products includes industry-leading connectors, components, plugs, wire & cables, and tooling used to transmit data, power, and signal in the machines, devices, and systems helping to make the world safer, sustainable, productive and connected.
Find AMP Products by Category
For 75 years, TE’s AMP has manufactured rugged electronic components for reliable connectivity in the harshest environments. The story of TE’s AMP began on September 15th, 1941 – at 3:30pm (EST) to be precise, in a room above a small Greek restaurant in New Jersey. This is where engineer Uncas A. Whitaker developed more reliable alternative to the rigid, soldered termination: the crimped termination. His invention was simple yet revolutionary. At the time, solder was used to complete connections. With Mr. Whitaker's solution, engineers could quickly make solderless, uninsulated electrical connectors that were faster to install than soldered termination, particularly when the space was very cramped, such as in aerospace and marine applications. Unlike the point-to-point wiring that needed to be soldered on both ends, crimped termination offered a small metal tube with a ring on one end combined with a specialized tool to make the crimp revolutionized the industry. The device allowed technicians to make quick, removable wire connections without solder and enabled the pre-assembly of wire harnesses. Crimped termination inspired Mr. Whitaker to found a new company: Aircraft Marine Products, known as AMP.
Mr. Whitaker’s solution came just in time for the Allied war effort in World War II. These new connectors were critical to the new higher performance aircraft being developed that operated at higher altitudes and dramatically higher shock and vibration conditions than their predecessors. These AMP connectors maintained electrical connections in the most demanding and harshest environmental conditions. Shortly after the United States entered the war, AMP received contracts from Boeing, Electrical Boat, and the Ford Motor Company. The result was an increasing number of military planes, ships, and field equipment were equipped with AMP’s reliable solderless connections. AMP built on this success by introducing, in 1943, the pre-insulated terminal. This product advanced a then-successful electronics product by reducing the product’s incidence of shorted circuits.

After the war ended, and production for the military equipment sharply decreased, many manufacturing companies struggled – and some faltered. The leadership of TE’s AMP took a long view to survive. The company re-invented itself by shifting its focus toward electronic solutions for harsh-environment commercial applications, including such then-growing industries as automotive and appliances. The company re-established itself by launching the strip-formed terminal, which – along with its AMP-O-MATER lead terminating machine – allowed manufacturers to increase their production rates, to the point of producing thousands of quality-inspected wire terminations per hour. This innovation enabled manufacturers to meet the growing demand for post-war products in the electric and appliance industries. It was a dynamic period of growth and invention for TE’s AMP. The company achieved early success around power tools, which were in high demand because of the post-WWII housing boom. Porter Cable was an earlier adopter of solderless terminations. During this period, the company developed an electrical splice that achieved public recognition because it was used in the Slinky – a popular children’s toy in post-war United States – to mechanically secure the free ends of the toy’s coil spring. Around the same time, the company expanded its portfolio by introducing connectors for pin and sockets, coaxial cables, and printed circuits – all to meet the demands of the growing telecommunications industry and cable-TV market.
As the company matured, and its products became synonymous with reliability and integrity, the company continued experimenting with new ideas. In 1964, the company’s spirit of innovation lead to it using the craft of glass blowing to produce hermetically sealed high-voltage relays, which today are used in cannot-fail applications such as defibrillators and space stations. And as the years passed, the company continued to surpass expectations. In 1977, TE’s AMP developed a resistive touch technology for touch screen devices, versions of which remain popular today. In 1984, the company developed coaxial cable nearly as thin as a human hair. This new standard in ultra-miniature coax enabled producing highly flexible 128-conductor ultrasound cable assemblies for use in diagnostic medical equipment. And a year later, in 1985, the company was developing – for the automotive industry – integrated subassemblies, using new automated application methods, to meet the industry’s need to simplify the complex and labor-intensive process of installing wire harnesses. To compete in a global market, Tyco International completed the purchase of AMP Inc., thereby solidifying the company's position as the world's largest manufacturer of electronic connectors. Then in 2007, TE Connectivity was split off from Tyco International in a three-way divestiture that would allow TE Connectivity to focus all of their resources on the electronic components business.
Types of TE Connectivity AMP Connectors
As demand worldwide sharply rose for 21st-century caliber electronics, TE’s AMP responded. In 2003, it was the first company to develop a fiber-optic connector with 72 fibers in a single compact housing. This important advancement was notable because the solution was not much larger than the company’s original single-fiber connector, which was introduced in 1975. Ten years before we developed this technology, industry engineers deemed it “impossible.” Today, it is part of the awesome connectivity that is helping make the world safer, smarter, greener, and more connected.
Ten years before we developed this technology, industry engineers deemed it “impossible.” Today, it is part of the awesome connectivity that is helping make the world safer, smarter, greener, and more connected.
Over the past decade, TE’s AMP portfolio has continued to evolve. In 2006, Our engineers have developed such engineering advancements as the breakthrough Acoustic Pulse Recognition (APR) touch-screen technology, which can detect a finger or stylus location on a touch screen – by recognizing the sound created when glass is touched at a given position.
Today, TE’s AMP product line includes an extensive list of passive electronic components, including wire connectors, plugs and interconnect systems, relays, switches, sensors, and wire and cable. These components are transmitting data, power, and signal in the highly sophisticated systems found in today’s cars, computers, communications equipment, industrial machines, commercial instruments, household appliances, and lighting. Throughout its many years of solving the unique connectivity challenges of our customers, TE’s AMP has performed as expected.
As we move closer to a future where most things are connected through the Internet of Things, OEMs will increasingly need electronic components that integrate the machines, devices, and systems people need, with solutions that are safe, green, highly reliable, and more connected. With TE's AMP products, OEMs can gain a crucial advantage in designing and building the next generation of technology.