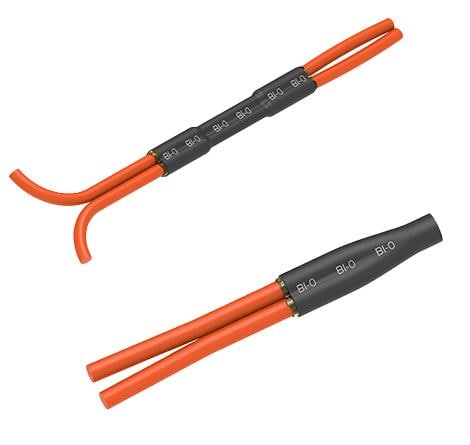
BIOFUSE Tubing: The next generation of Bio-Based Heat Shrink
The TE connectivity's (TE) BIOFUSE tubing line has been engineering to respond to the increasing global awareness of sustainability and environmental protection. BIOFUSE is bio-based polyethylene heat shrink tubing line to address the growing demand for the use of environmentally friendly and sustainable materials across various industries.
Concerns about the increasing carbon footprint of major manufacturing facilities have prompted the industry to switch from bio-sources to polymers. Major advancements in polymer chemistry facilitate the development of purelysynthetic or complex polymer materials.
Plant-derived bio-based polymers, also known as the next-generation polymers which have been used to reduce fossil fuel usage.
Features
- Highly flame retardant
- Halogen free
- REACH and RoHS compliant
- CA PROP 65 compliant
- High shrink ratio allows a few sizes to cover a wide range of splice and component diameters
Benefits
TE’s Bio-Based Heat Shrink Tubing Products
- Bio-based products have a lower CFP than conventional products
- Excellent environmental sealing
- Moisture and fluid ingress protection
- Prevention against corrosion
- Suitable to withstand various Automotive fluids
- Excellent strain relief against impact to the splice and wire configurations
- Abrasion resistant
- Provides excellent electrical insulation to prevent damage and extend performance
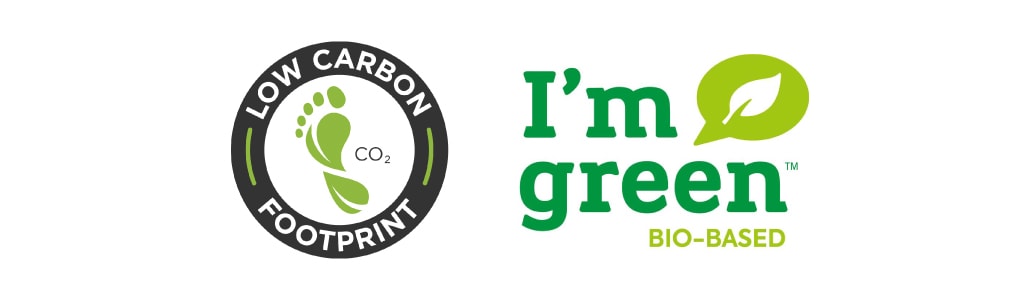
BIOFUSE Tubing Portfolio
Myths and Facts about Bio-Based Polymers
1. Why can't the plastics sector decarbonize?
In 2021, the European Union set itself a legally binding target to be an economy with net-zero greenhouse gas emissions by 2050. This commitment has triggered myriad legislative initiatives which aim to curb carbon emissions across all industrial sectors, but this is very difficult for sectors where decarbonization is not an option. Plastics is such a sector. Without carbon, you cannot make plastics. What is needed here is de-fossilization, whereby you replace fossil carbon sources with alternatives. Today, more than 99% of plastics are made using fossil sources, so we need to start deploying these alternative sources to enable de-fossilization as soon as possible. Using recycled plastics is one option, and another, complementary one, is the use of biomass.
2. How can plastics made from biomass, such as sugarcane, reduce carbon emissions in plastic production? Surely, the production of any plastic comes with high greenhouse gas emissions?
Conventional plastics are made from fossil resources (oil, natural gas, or coal). We extract these natural resources, refine them, and they then produce the basic building blocks needed to make plastics. The aggregated GHG emissions of all these steps is around 2.4 kgCO2/kg, and that is what is referred to as the 'cradle-to-gate carbon footprint' of plastics. But this is just the beginning of the story. Plastics are then converted into products, used, reused, recycled (all these stages can add GHG emissions) and eventually reach their end-of-life when they are landfilled or incinerated. At this end-of-life stage the carbon contained in the molecule will be released adding another 3.1 kgCO2/kg[1].
Bio-based plastics are chemically identical to fossil plastics meaning that they are converted, used, recycled, and disposed in the same way, so the only difference is in how they are produced (the cradle-to-gate). The production of the I'm green TM bio-based plastic also has GHG emissions coming from the cultivation of crops (fuel for machinery, fertilizers, pesticides, etc are all made from fossil resources) and the industrial steps to produce the plastics, but it also has steps in place that abate and avoid emissions that fossil plastics cannot.I'm green TM bio-based uses sugarcane which fixates carbon in the soil if it is grown on degraded land. Leftover biomass from the production is used to make renewable electricity, which avoids the use of natural gas to power the plant. And importantly, carbon is absorbed during the growth of the sugarcane, meaning that the carbon present in the plastic has been captured directly from the atmosphere. Consequently, the upstream life cycle stages, when balanced out, is favourable. More carbon is removed from the atmosphere than emitted. This is why we say the cradle-to-gate carbon footprint of I'm green TM bio-based polyethylene is -2.12 kgCO2/kg.
3. The Brazilian rainforest is a very important carbon sink and climate regulator. The production of sugar cane will surely be disruptive to this important ecosystem?
Brazil is one of the global leaders in sugar and ethanol production making sugarcane production a highly important agricultural crop. Despite this, sugarcane only occupies 1% of Brazil's territory and is grown in the center-south of Brazil, thousands of kilometers from the Amazon rainforest - that distance is approximately the same as the distance between Lisbon and Helsinki.
As the market for sugar and ethanol has grown, more sugarcane has been planted to meet the demand. But even this growth in agriculture can be done sustainably. 95% of the sugarcane planted in the last twenty years is on what used to be pastureland with moderate to severe levels of degradation[2]. When planted on degraded land in particular, sugarcane helps increase the soil's carbon stocks, and since it is being grown very far away from the rainforest, it is not contributing to the deforestation of the Amazon.
4. Sugarcane is a food crop. Making plastics out of it will have a negative impact on food production, so why is not all of it turned into sugar?
When Brazil decided to replace gasoline with ethanol almost fifty years ago, the country was not a big exporter of sugar. Today, Brazil is the biggest exporter of sugar and the second biggest producer of ethanol, globally. Such progress is due to the optimization of the crop and efficiency of production. With technological advancements here, farmers were able to produce more sugar andethanol with the same amount of crop.To further understand if using sugarcane is putting pressure on food prices, here are some figures are important to put things into perspective. While 1% of the country's land is covered by sugarcane, 19% is pasture and 14% is used for agriculture and forestry. There is an area of severely degraded pastureland, no longer suitable for livestock grazing, which is bigger than Poland[3]. It is exactly this land that has low carbon stocks and is susceptible to erosion that sugarcane helps recover. This means there is more than enough land for sugarcane to expand into without the need to occupy native vegetation or compete with other food crops.
So, to summarize, Braskem uses a very small fraction of existing sugarcane crops (~1%), and these crops are currently only using 1% of the land available in Brazil, without competing with the global demand for sugar.
5. It is all very well to say that the production of sugar cane does not compete with food production, nor negatively impacts the rainforest, but what about the sourcing aspects? Monoculture production uses a lot of pesticides and has a negative impact on biodiversity.
In the state of São Paulo, where 60%[4] of the country's sugarcane is planted, crop rotation with leguminous vegetables is a common practice that helps fix nitrogen in the soil. Hence, 15% to 20% of sugarcane producing areas are also used for the cultivation of soybean, beans and peanuts, supplying the food market.Another practice is the biological pest control program. The use of chemical pesticides is significantly reduced, for example, by using a wasp to control the population of the sugarcane borer, a bug that negatively impacts the development of the cane. Over 6 million hectares of land already use this technique[5]. In order to preserve and restore biodiversity, some farms have established green corridors linking two protected areas, allowing native wildlife to flourish alongside the sugarcane crops. Braskem further develops these practices through its Responsible Ethanol Sourcing Program[6]. Furthermore, according to UNICA (Brazilian association of sugarcane industry), since 2007 when the Green Protocol was signed, their associated mills have planted over 46 million seedings to recover over 200kha of riparian areas and protected 7,315 springs. Sugarcane producers are also increasingly monitoring bee populations and are using their permanent preservation areas to enhance habitats for them to thrive. As shown in the case of Brazilian sugarcane, intelligent and kind farming can in fact help restore biodiversity, rather than destroy it.
6. Ok, so how do you produce the ethanol used for the development of plastics?
Once the sugarcane has been harvested, it moves onto the mills to be processed. Modern Brazilian sugarcane mills are equipped to produce sugar and ethanol (from the sugarcane juice), and electricity (from the sugarcane fibres known as bagasse). The energy made from burning bagasse, making steam and electricity, not only completely powers the plant, but often there is an excess of this renewable energy which is sold back to the grid. The mills are also very resource efficient, and nutrient rich waste and wastewater (also known as vinasse) are returned to the field to fertilize the soil. The ethanol produced is then converted into ethylene, which is then polymerized to make polyethylene.