Our Advanced High-SpeedI/O Liquid Cooling & Thermal Bridge Hybrid Solution integrates liquidcooling cold plates to tackle the most challenging thermal issues. These solutions are engineered for fixed cooling applications with restrictedairflow, such as liquid cooling systems or cold plates, making them idealfor hyperscale data centers, AI/ML, and HPC workloads.
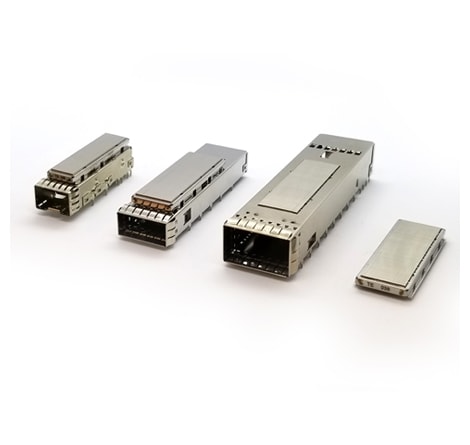
Superior Thermal Performance and Durability
TE Connectivity’s advanced thermal management solutions address the increasing heat dissipation demands of modern I/O applications. Our innovative Thermal Bridge Technology provides better thermal resistance compared to traditional gap pads or thermal pads, while our Advanced High-Speed I/O Liquid Cooling & Thermal Bridge Hybrid Solution integrates liquid cooling cold plates to tackle the tough thermal challenges. These solutions are engineered for fixed cooling applications with restricted airflow, such as liquid cooling systems or cold plates, making them ideal for hyperscale data centers, AI/ML, and HPC workloads.
Advanced Thermal Management for I/O
TE Connectivity’s thermal management portfolio now includes the groundbreaking Advanced High-Speed I/O Liquid Cooling & Thermal Bridge Hybrid Solution. This hybrid approach combines our patented thermal bridge technology with liquid cooling cold plates, delivering enhanced heat dissipation for power-dense AI applications (up to 40W per module). Alongside our Thermal Bridge Technology, which offers better thermal resistance than traditional methods, this solution ensures reliability and scalability in fixed cooling environments with minimal airflow.
Product Benefits
- Optimized for applications using cold plates with liquid cooling or heat pipes, ganged heatsinks, or direct chassis conduction with minimal airflow.
- Provides consistent, long-lasting thermal performance with an elastic compression design resistant to set and relaxation over time.
- Eliminates the need for interface materials such as TIM or thermal gap pad between Thermal Bridge and liquid cool cold plate.
- Ensure low and consistent compression force between cold plate and I/O plug/chipsets. Enhances heat dissipation for AI/ML workloads with the hybrid liquid cooling solution.
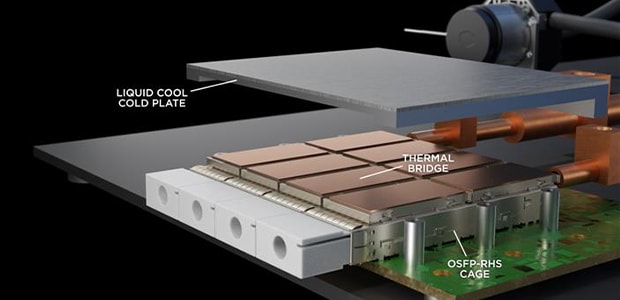
Product Features
- Spring loaded bridge offers 1.0mm (typical) of z-axis compression
- Individual plate actuation allows for surface conformability in the x-axis
- Dual-spring design allows for tilt conformability in the y-axis
- At 3 points of contact per plate, a typical bridge will have 150+ points of contact to adjacent surface
- Dry interface resistance 20-40% lower than most traditional riding heatsinks
- Thermal Resistance: ~ 0.7 to 1.7 cm2°C/W
- Better thermal resistance over most traditional thermal technologies.
- Near -zero plate gap in the thermal bridge construction for optimized compression and thermal transfer.
How the Thermal Bridge Technology Works
Our new, innovative thermal bridge technology replaces the traditional gap pad or thermal interface material (TIM) with integrated mechanical springs to provide interface force and 1.0mm of compression travel. This interleaved series of parallel plates allows heat to pass from the I/O module to the cooling area.
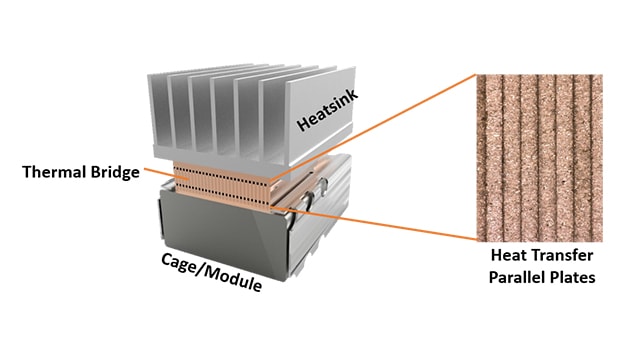
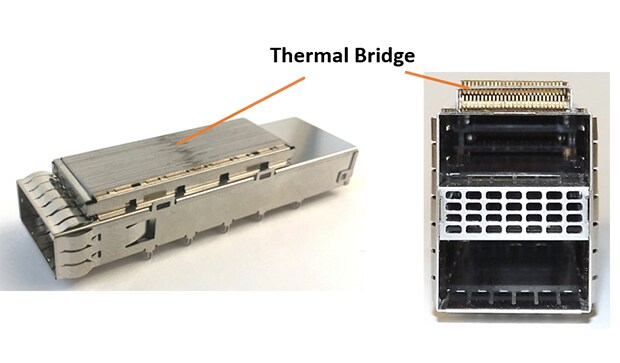
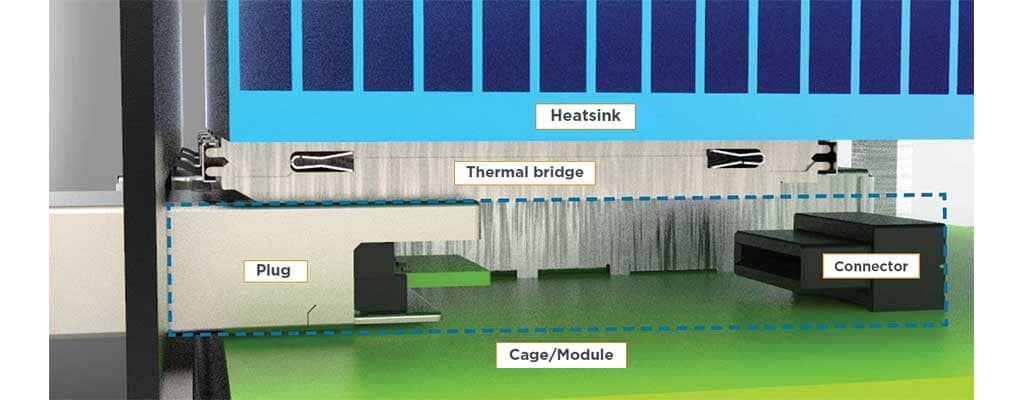
Select Applications
Thermal Bridge
Frequently Asked Questions (FAQs)
Q: What are the best applications for using thermal bridge technology?
A: This solution was developed to dissipate heat in applications that use cold plates with liquid cooling or heat pipes, ganged heatsinks or direct chassis conduction applications with little to no airflow. It is a mechanical alternative to the traditional gap pad or thermal interface material (TIM).
Q: How does the thermal bridge work with fixed heat sink and cooling applications?
A: The thermal bridge solution is optimized for applications where the heat sink or cold plate is at a fixed location. For these types of applications, normally TIMs or gap pads are used and require a high level of compression to bring the thermal resistance down. These TIMs and gap pads tend to relax or set over time, decreasing the performance. TE’s thermal bridge technology replaces the gap pad in these applications with a mechanical, compressible gap pad, providing low-compression force and low thermal resistance, making this solution more reliable over time.