We partner with our customers to develop and co-engineer connectivity, sensor, and relay solutions that meet the growing needs of warehouse automation.
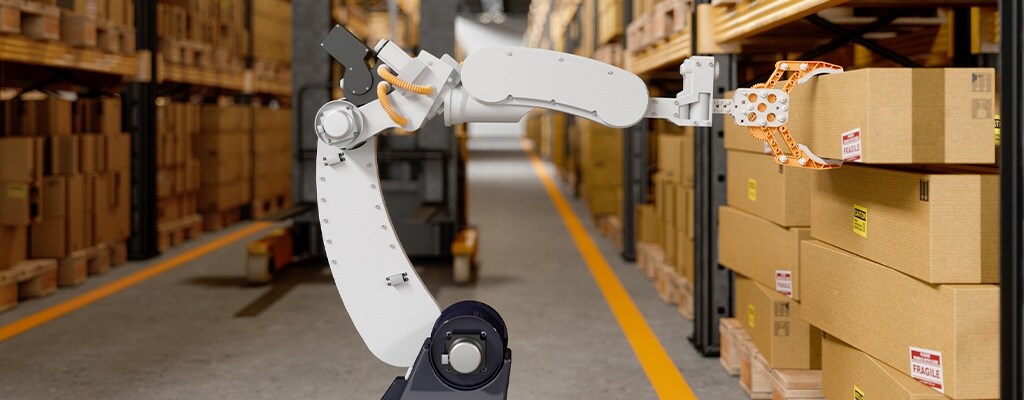
Optimizing Operations with Warehouse Automation
Today’s warehouses are becoming more productive and flexible through the automation of key tasks such as storing, retrieving, and moving inventory. Learn how our solutions are helping turn the next level of warehouse automation into reality even faster.
The rise of Industry 4.0 and rapid growth of e-commerce have led to a revolution in warehouse automation. Increasingly complex tasks can now be automated within a wide range of environments thanks to the latest generation of robotics. Automated guided vehicles (AGVs), which require guidance from wires or strips, and autonomous mobile robots (AMRs), which feature smart navigation and higher flexibility, are making warehouses more productive than ever. With automatic storage and retrieval systems (ASRS), these robots can work together to handle material storage, make smart decisions on material placement and inventory rotation, and fulfill tasks such as pickup and shipping preparation. In most warehouses, though, there will always (for the foreseeable future at least) be robot and human collaboration, and forklifts are still a key piece of equipment in warehouses.
At TE Connectivity (TE), we are enabling many of the trends and developments in forklifts, AGVs, AMRs, and ASRS through a broad portfolio of board connectivity and relay products; with solutions for electric drives, battery systems, charging stations, electric control units (ECUs), and wiring. Through our global manufacturing footprint and logistics and support network, we enable multinational players to source in-location worldwide, where our field application experts can advise on product choice, evaluate architecture, and help optimize the function and cost of warehouse equipment.
Warehouse Automation Solutions

Electric Drive
The motor controller (often called inverter or drive) powers and controls the motor in warehouse automation equipment. To enable efficiency and quality control of the motor, fast and reliable connectivity between the motor and inverter is needed. As is the case with all factory-based electric drive applications, shock and vibration capability, and sealing are important factors at play in warehouse automation equipment such as forklifts, AGVs, AMRs, and ASRS. Below you can browse our products for electric drives, which arespecifically engineered to provide reliable, high-quality connections, all in a small form factor.

Battery Management
In warehouse automation, the reliability of forklifts, AGVs, AMRs, and ASRS is crucial. The steady operation of these warehouse vehicles depends on a battery management system (BMS), which tracks battery usage, temperature, and charging status. Since battery connectors are one of the most vulnerable parts of the system, the use of rugged, high-quality connections is key to avoiding downtime. Our products for battery management are designed and engineered to work in harsh environments with high vibration. They also enable the miniaturization needed for increasingly compact batteries and battery systems.

Charging Stations
Where there are batteries, there must be charging. Speed is key in warehouse automation, and the various robots operating in a warehouse cannot sit idly for hours on end to power up. Therefore, charging currents tend to be high in warehouses, ranging from 40 A to 300 A.
Reliable power connectors simplify assembly efforts and help reduce safety hazards, and TE’s products can help improve power distribution capabilities between the charger, battery, and drive system. Our connectors offer multiple contact points to support high-vibration tolerance, and our large product portfolios serve a wide variety of uses and compact designs.

ECU, HMI and vehicle wiring
In warehouse vehicles and equipment, a multitude of controllers, sensors, actuators, and human-machine interfaces (HMI) need to be wired together. For all these systems to work together, the connections between them must be robust and capable of withstanding high vibration. For sensors and actuators, interoperability between suppliers and high protection against dust, liquids, and vibration is important.
Our products for ECUs and vehicle wiring are designed with harsh environments in mind and offer reliable field installable solutions with push-pull technology and multiple connectors mounting options for easy integration in devices.
