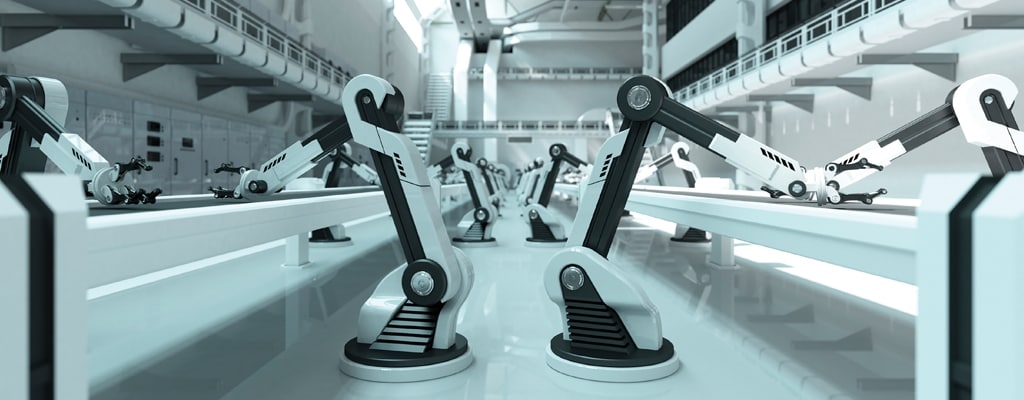
Trend Insight
The Role of Sensors in the Evolution of Robotics
Learn how sensors are helping drive the evolution of robotic automation.
At one time, robotics was considered more science fiction than reality. That’s changing. Today, robots are increasingly playing a role in our everyday lives. They’re zooming around our homes to pick up dust, helping surgeons perform operations with even more precision, sniffing out suspicious packages for law enforcement, and on the factory floor — they’re performing all kinds of tasks for automotive, electronics, and industrial manufacturing companies.
Traditional industrial robots, logistical robots, and collaborative robots all have their jobs to do — just as robot developers and design engineers do. They require solutions that enable accurate, safe, cost-effective operations. With the drive toward “Industry 4.0,” the use of robotic, automation, and control systems on the factory floor have become commonplace as they allow manufacturers to increase efficiency, productivity, and profitability. Industry 4.0 or the smart factory has been defined as the mixing of traditional manufacturing and industrial practices with the technological world. Regardless of its name, it is creating a complete revolution in factories and manufacturing.

Four Key Trends in Digital Transformation
According to an article in Forbes Magazine, “there are four key trends in the digital transformation ” that manufacturers should be paying close attention to:
- Connected consumers, customized experiences: Combining the efficiencies of mass customization with a truly unique product.
- Connected employees: Empowered by the information they need most.
- Optimized production: Leveraging insights from real-time data.
- Transformed products: Manufacturing floor machinery that can predict failure and maintenance needs, all thanks to more analytics and data.
These four trends all touch on one key foundational technology: sensing. At TE Connectivity (TE), we believe that as the need for industrial robotic automation advances, sensing technology will continue to be the foundation for data collection that will help transform manufacturing floors into the connected, cost-effective, and reliable factories of the future.
In fact, TE is future ready in robotics. We understand that the greater flexibility and precision that robotic systems demand requires more flexibility and even more reliable connectivity solutions. From automotive and aircraft construction to the pharmaceutical industry to logistics and metal processing, the latest generation of industrial robots can handle even more complex tasks.
In these robotic environments, connections can’t fail. TE offers numerous force, temperature, pressure, and position sensors that provide highly accurate measurements for precise movement control and accurate monitoring of system components for preventative maintenance. TE can help you meet the challenges your design engineers face.

The Challenge: Accuracy and Precision
As the robotics revolution takes hold, most manufacturers are finding that they need to build accurate and precise sensing elements into robotic equipment to help them handle the challenges of the factory floor. As an example, for collaborative applications, sensing systems must not only detect if a human is around but also prevent any possible collision between the robot and nearby workers. Sophisticated sensor technologies are a core requirement yet meeting these design requirements is not easy. Most environments require variable sensing ranges and resolutions and factory floor environments can be dirty, harsh, and unforgiving — making it difficult to differentiate between humans and other robots working in the same environment.
Sensor Highlights
Temperature Sensing Technology
Compact discrete negative temperature coefficient (NTC) thermistor sensors offer highly precise measurements and excellent long-term stability for monitoring the surface temperatures of industrial equipment. This NTC sensor technology uses the resistance properties of ceramic/metal composites to measure the temperature. Additionally, digital temperature sensors are designed to be highly precise and provide robotic control and temperature optimization where space constraints exist. For high-temperature processes where temperature needs to be monitored at a distance, the integration of thermopile infrared (IR) sensors offer non-contact temperature measurement.
Anisotropic Magnetoresistive Technology
With its anisotropic magnetoresistive technology (AMR) and multiple form factors, the KMXP position sensor provides excellent precision and reliable, accurate measurements in extreme environments including high temperatures. These sensors are playing an increasingly important role in many industrial robotic applications. Advanced applications in harsh environments need sensors that perform well, even when exposed to oil, dirt, and dust. These sensors are offered in two different DFN packages for multiple orientation options and the packages can be easily integrated into almost any automated assembly process.

The Challenge: Personnel Safety for Robotic Equipment
Safety ranks as the top priority for robotic automation developers. Because industrial robots can introduce many new safety hazards into the workplace, the “do no harm” approach has become even more important as these robots are increasingly used for heavy lifting on automotive assembly lines and other industrial manufacturing venues. There are strict regulations, as well as stiff penalties, surrounding robotic safety. Manufacturers must prepare for this before the robots are installed to ensure compliance and create a safe environment for workers. Training for manufacturing staff is also required to ensure employee safety. When robotic equipment is implemented, a new level of expertise is required from workers. Many will have to be trained on how to operate this new equipment while other employees will have to be hired that have the proper certifications, education, and robotic experience.
Sensor Highlights
Piezoresistive Load Cell Technology
Similar to how a digital scale can measure weight, piezoresistive load cells can measure force based on the load being applied to the sensor. Within a factory setting, these sensors can be integrated into factory floor mats to sense if a human is in near proximity to dangerous factory equipment helping to prevent injury.
Load cells are also used in some transfer equipment to provide safe movement of components and assemblies through the factory. In this case, load cells would be able to determine the weight of the load and would be able to trigger a fault or error condition if the load was too heavy or unbalanced.
FX29 Compact Compression Load Cell
The FX29 is a compact compression load cell that offers exceptional price-to-performance in a robust sensor package with a millivolt, analog, or digital output signal.

The Challenge: Moving to an IoT-enabled Digital Infrastructure
The industrial internet of things (IIoT) presents enormous productivity potential for manufacturers, but the true benefits can be difficult to realize. Industrial robotics inherently promote connectivity and are proving to be a great starting point for broader IIoT initiatives – and are increasingly being integrated from the ground up. TE has observed that companies are beginning to recognize the importance of sensors and how they are changing the approach for IIoT applications— particularly as companies see the benefits of merging traditional operational areas and information technology. Many believe IIoT has the potential to drive greater efficiency and improve productivity. In fact, industry analysts believe that the combination of artificial intelligence (AI), machine learning, and contextually rich, real-time data streams delivered by IIoT sensors and networks is going to make IIoT business cases far more compelling in 2019 and beyond.
As the IIoT smart factory experience evolves, it will run on data — provided by TE Connectivity sensors. Some of the world's largest manufacturers have already begun to integrate industrial robots with IIoT in manufacturing sites around the world — increasing productivity and decreasing unscheduled downtime via predictive maintenance sensing technologies — saving time and money. Some large, automotive manufacturers are using thousands of connected robots in their factories to collect real-time data on robotic performance. The connected sensor technology enables them to see when a robot needs maintenance and proactively address performance issues before the entire assembly line shuts down. In the future, they will be able to monitor and adjust robotic accuracy and repeatability in real time to improve product quality. The automotive industry is not the only early adopters of this approach since connected robotic technology can be valuable in other industrial applications such as industrial printing and packaging, and in the medical field, food service, and law enforcement.
In general, we are in the early stages of connected robot technology, but the desire for greater connectivity exists. As this technology evolves, we believe these systems will transform into more of an in-process adaptive tool that allows the robots to monitor and automatically adjust their own performance for maximum productivity. For many facilities, it simply comes down to making the investment at the right time. For example, commercialization of more higher performance sensors is enabling IIoT to a greater degree. Sensors that traditionally cost thousands of dollars are now more affordable and more compact to enable a smarter factory. The investment is becoming less burdensome up front with advances in sensor technology, digital compensation and signal conditioning, and wireless signal transmission.
And while most see the productivity promise, technical and network employees still see it as a risk from a network security perspective. Smaller proof-of-concepts (POCs) can be critical to give companies a better opportunity to calculate the associated cost-saving benefits and ROI driven by greater efficiency and productivity.
Sensor Highlights
Pressure Sensor Technology
TE’s pressure transducers are suitable for a wide range of industrial applications including some that can be used in hazardous locations and feature a number of products with global certifications. In addition, our board-mountable pressure sensors and media- isolated pressure sensors offer analog or digital output signals for embedded designs and OEM applications.
IoT Start Technology
To help companies implement smaller POC approaches, as mentioned above, TE developed a product that gives manufacturers an opportunity to calculate the associated cost-saving benefits and ROI driven by greater efficiency and productivity. The IoT Start toolkit provides a complete solution that includes sensing elements, electronics, a communications interface, and wireless capabilities, all packaged in an easy-to-use module. More specifically, this connected device allows for experimentation in IIoT applications to enable testing and evaluation of connected systems.
This innovative toolkit can help engineers get started with developing IoT applications and enable them to quickly extract data and achieve success in real time.
M3200 Compact Industrial Pressure Transducer
The M3200 series compact industrial pressure transducer, with analog or digital output, is suitable for measurement of liquid or gas pressure, even for difficult media such as contaminated water, steam, and mildly corrosive fluids.

Conclusion
As the robotics solutions for the IIoT market continue to evolve, will you be ready with the right solution? TE Connectivity offers solutions that can help you get the data you need with precise, real-time measurements of pressure, humidity, force, vibration, temperature, position, and more — advantages that increase efficiency, productivity, and product quality on the factory floor. TE sensors are the backbone of the growing IIoT industry, serving thousands of applications across hundreds of functions and operations.
TE’s wide sensor portfolio and deep engineering experience enables engineers to develop and continuously innovate on their IoT applications, ultimately helping businesses thrive, communities improve, and people connect.
Industrial Sensor Applications
TE Connectivity (TE) manufactures innovative industrial sensors that help customers transform concepts into smart, connected creations.

Robotics and Industrial Sensor Resources