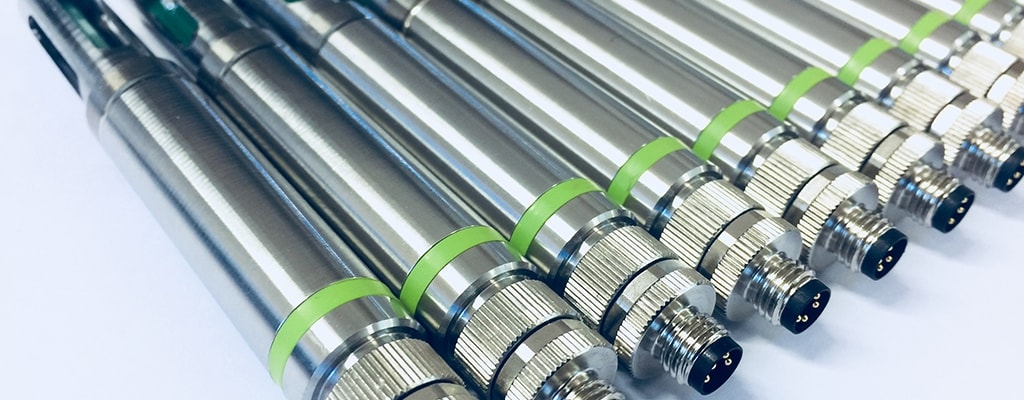
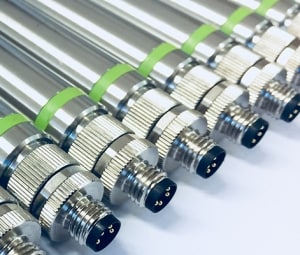
Clients [want to know] what we provide now...and throughout that 4-year cycle. Partnering with TE enables us to keep innovating and thinking about client needs so we can continue to solve their problems throughout the relationship.
Customer: commonSENSE Monitoring Solutions, Ltd.
Focus: Helping businesses stay reliably informed
Solution: Environmental monitoring system and service
Location: Essex, U.K.
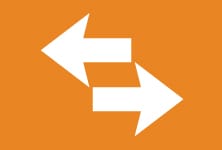
ENGINEERING CHALLENGES
• Plug-in capability for measurement sensors
• User-friendly interface anyone can use
• Meet regulatory and maintainability needs
The founders of commonSENSE Monitoring Solutions saw that environmental monitoring systems for sensitive goods could be better, smarter and more user-friendly. They set out to develop a system that could be used by anyone, even non-engineers, and adaptable to nearly any measurement need. Their first big challenge was developing a common communication protocol, which they did on their own, so they could plug in any measurement device and report data out.
Next was creating a user interface that is very intuitive, designed to help the end client easily withdraw data needed for regulatory compliance audits. “Almost all the existing systems we looked at prior to developing commonSENSE PRO felt clunky and outdated. The software was slow, and data was often stored on site,” said Paul Humphries, commonSENSE CEO.
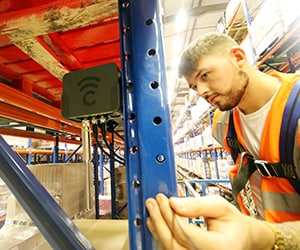
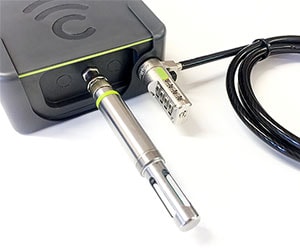
Many clients were using 10+-year-old servers to store and manage their temperature data, with little or no redundancy built into their system. In addition, the display of both real-time and historical data was often confusing and difficult to digest. commonSENSE wanted their software to be easy enough for people to use every day, but configurable enough that clients could adapt the software to suit their specific needs.
Maintainability was also a focus. Typically, in most monitoring systems, the transmitter houses all electronics including a passive sensor, which makes annual calibration of the device very time-consuming and cumbersome. The device has to be removed from the location, taken to a UKAS-accredited calibration laboratory, calibrated and then reinstalled on-site – a process that takes 2-3 weeks. commonSENSE saw these challenges as an opportunity to revolutionize monitoring by designing a solution from the end user’s perspective and, after researching several sensor manufacturers, they chose to work with TE.
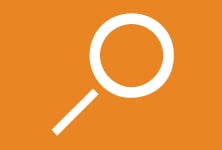
PARTNERSHIP SOLUTION
• Develop highly accurate, smart sensors
• Enable easy calibration and regulatory compliance
• Mitigate future process failures
commonSENSE came to TE with a clear goal: To deliver a new highly accurate and dependable benchmark in monitoring the production, storage, and distribution of sensitive goods. The team wanted a design in which the sensor performed the analog-to-digital conversion and sent temperature data digitally to an output interface. Due to industry regulatory requirements, this sensor would also need to store programmable calibration offsets to mitigate against drift. TE designed a custom solution – a digital temperature probe with electronics in the probe head instead of in the transmitter.
“This technology with data communication capabilities built in is a game-changer for us,” said Humphries. “Because our transmitters will accept any sensor input, customers can come to us, tell us they have a problem to solve, and we know that with TE we can develop a sensor to overcome that problem.”
The interface is set up to allow users to define the level of detail they want from the software. Engineers can view individual sensor data and reports on their location; admin-level users can gain an overview of the system installed across multiple sites; and with electronic signature capability, users have all the data they need for regulatory submissions at their fingertips.
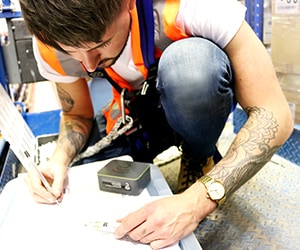
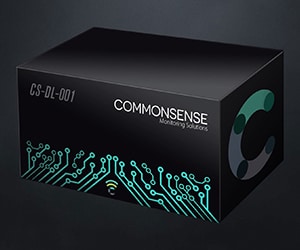
To mitigate failures, commonSENSE’s CTO Andrew Mills worked with one of TE’s product development engineers to refine the firmware and communications protocol while the sensor teams worked together to refine the accuracy, calibration and housing requirements. To help account for stem conduction, they covered the sensing element – a very small resistance temperature detector (RTD) located in the tip of the probe – within thermal paste. The digital temperature probe provides high accuracy over a large temperature range which makes it suitable for a wide range of applications and different places of installation. Additionally, TE packaged the sensor into a waterproof, IP-rated, stainless steel housing, making it easy to install and use and enabling the sensor to be fully immersed into a bath for calibration.
Calibration data is easily accessible, and the calibration process itself is much more efficient. Each sensor can simply be swapped out with a newly calibrated sensor. Replacement sensors can be calibrated up to a month before and installed in place of existing sensors on location. This reduces the downtime of the system from weeks to less than an hour for each sensor. From the sensor ID, users can navigate and download or upload all calibration data.
As a final client-focused feature, the monitoring service is offered as a 4-year subscription. Travis Hurlock, commonSENSE CMO, explains why: “Clients aren’t only interested in what we provide now, but also what we can provide throughout that 4-year cycle. Partnering with TE enables us to keep innovating and thinking about client needs so we can continue to solve their problems throughout the relationship.”
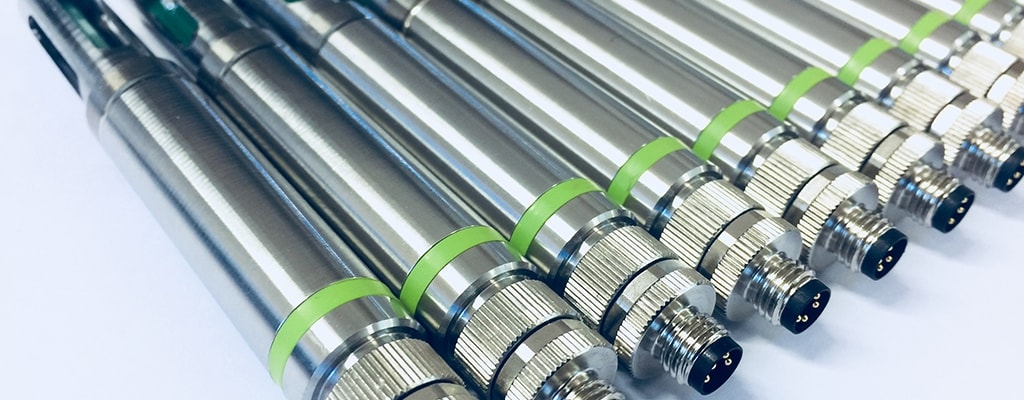
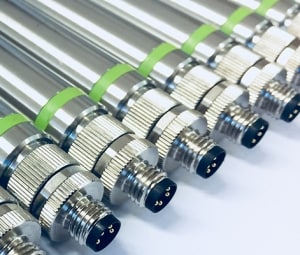
Clients [want to know] what we provide now...and throughout that 4-year cycle. Partnering with TE enables us to keep innovating and thinking about client needs so we can continue to solve their problems throughout the relationship.
Customer: commonSENSE Monitoring Solutions, Ltd.
Focus: Helping businesses stay reliably informed
Solution: Environmental monitoring system and service
Location: Essex, U.K.
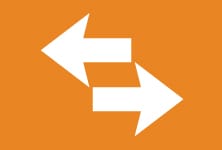
ENGINEERING CHALLENGES
• Plug-in capability for measurement sensors
• User-friendly interface anyone can use
• Meet regulatory and maintainability needs
The founders of commonSENSE Monitoring Solutions saw that environmental monitoring systems for sensitive goods could be better, smarter and more user-friendly. They set out to develop a system that could be used by anyone, even non-engineers, and adaptable to nearly any measurement need. Their first big challenge was developing a common communication protocol, which they did on their own, so they could plug in any measurement device and report data out.
Next was creating a user interface that is very intuitive, designed to help the end client easily withdraw data needed for regulatory compliance audits. “Almost all the existing systems we looked at prior to developing commonSENSE PRO felt clunky and outdated. The software was slow, and data was often stored on site,” said Paul Humphries, commonSENSE CEO.
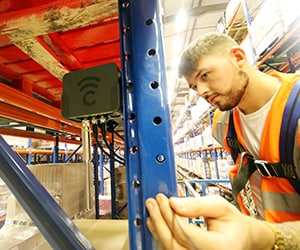
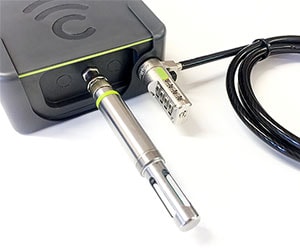
Many clients were using 10+-year-old servers to store and manage their temperature data, with little or no redundancy built into their system. In addition, the display of both real-time and historical data was often confusing and difficult to digest. commonSENSE wanted their software to be easy enough for people to use every day, but configurable enough that clients could adapt the software to suit their specific needs.
Maintainability was also a focus. Typically, in most monitoring systems, the transmitter houses all electronics including a passive sensor, which makes annual calibration of the device very time-consuming and cumbersome. The device has to be removed from the location, taken to a UKAS-accredited calibration laboratory, calibrated and then reinstalled on-site – a process that takes 2-3 weeks. commonSENSE saw these challenges as an opportunity to revolutionize monitoring by designing a solution from the end user’s perspective and, after researching several sensor manufacturers, they chose to work with TE.
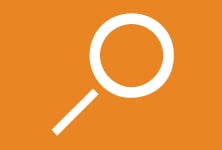
PARTNERSHIP SOLUTION
• Develop highly accurate, smart sensors
• Enable easy calibration and regulatory compliance
• Mitigate future process failures
commonSENSE came to TE with a clear goal: To deliver a new highly accurate and dependable benchmark in monitoring the production, storage, and distribution of sensitive goods. The team wanted a design in which the sensor performed the analog-to-digital conversion and sent temperature data digitally to an output interface. Due to industry regulatory requirements, this sensor would also need to store programmable calibration offsets to mitigate against drift. TE designed a custom solution – a digital temperature probe with electronics in the probe head instead of in the transmitter.
“This technology with data communication capabilities built in is a game-changer for us,” said Humphries. “Because our transmitters will accept any sensor input, customers can come to us, tell us they have a problem to solve, and we know that with TE we can develop a sensor to overcome that problem.”
The interface is set up to allow users to define the level of detail they want from the software. Engineers can view individual sensor data and reports on their location; admin-level users can gain an overview of the system installed across multiple sites; and with electronic signature capability, users have all the data they need for regulatory submissions at their fingertips.
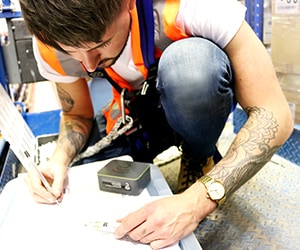
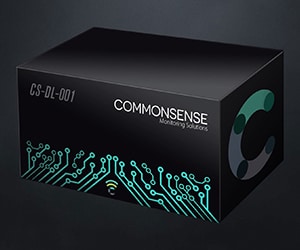
To mitigate failures, commonSENSE’s CTO Andrew Mills worked with one of TE’s product development engineers to refine the firmware and communications protocol while the sensor teams worked together to refine the accuracy, calibration and housing requirements. To help account for stem conduction, they covered the sensing element – a very small resistance temperature detector (RTD) located in the tip of the probe – within thermal paste. The digital temperature probe provides high accuracy over a large temperature range which makes it suitable for a wide range of applications and different places of installation. Additionally, TE packaged the sensor into a waterproof, IP-rated, stainless steel housing, making it easy to install and use and enabling the sensor to be fully immersed into a bath for calibration.
Calibration data is easily accessible, and the calibration process itself is much more efficient. Each sensor can simply be swapped out with a newly calibrated sensor. Replacement sensors can be calibrated up to a month before and installed in place of existing sensors on location. This reduces the downtime of the system from weeks to less than an hour for each sensor. From the sensor ID, users can navigate and download or upload all calibration data.
As a final client-focused feature, the monitoring service is offered as a 4-year subscription. Travis Hurlock, commonSENSE CMO, explains why: “Clients aren’t only interested in what we provide now, but also what we can provide throughout that 4-year cycle. Partnering with TE enables us to keep innovating and thinking about client needs so we can continue to solve their problems throughout the relationship.”