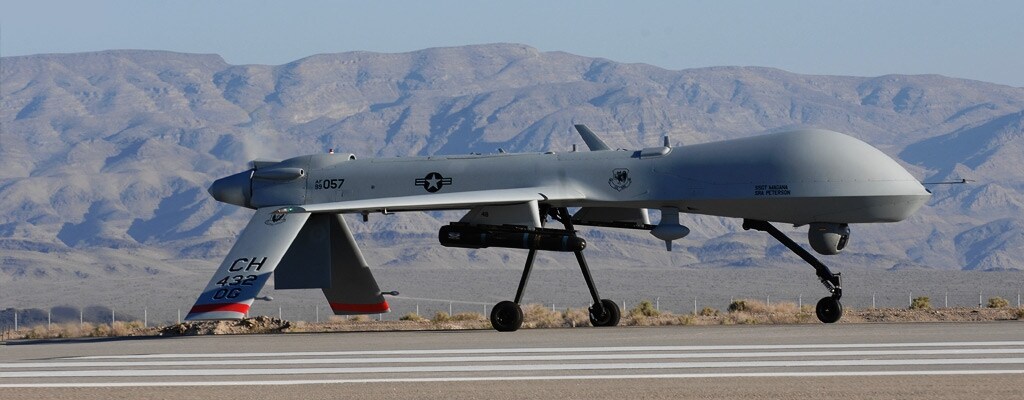
Trend Insight
Engineered to Endure
Today’s UAV subsystems demand high bandwidths combined with low SWaP. VPX technology provides the performance and ruggedness to satisfy those demands. By: Matthew R. McAlonis, Senior Manager, Product Development Engineering, Aerospace, Defense, and Marine
Increasingly unmanned aerial vehicles (UAVs) are expected to have longer persistence, remaining on station for durations measured not in hours but in days. The ability to loiter for surveillance and strike missions places a significant design emphasis on saving space and weight throughout the systems. An ounce here and an ounce there adds up to many pounds overall. At the same time, the sophistication of a UAV's surveillance capabilities continues to expand. Capable of gathering massive amounts of data, multiple cameras and sensors cover a wide frequency spectrum from visible light to infrared and thermal with impressive resolution and field of view. The ARGUS imaging system, for example, can spot a six-inch object within a ten-square-mile radius from 20,000 feet in the air. The ARGUS system uses 368 cameras and can capture, process, and download one million Terabytes a day. Combining images from multiple cameras and other signal processing needs require fast embedded computers and sophisticated software. Because of the enormous amount of data generated by the sensors, an additional system challenge is separating the wheat from the chaff via onboard processing so that only critical data is transmitted to satellites or ground stations. Even if the ARGUS system can process one million terabytes a day, the larger Intelligence, Surveillance, Reconnaissance infrastructure cannot handle such loads, even with hefty data compression.
Embedded Balancing Act
Scalability
One size does not fit all
Embedded computing systems must balance a variety of competing needs. These include:
- Higher processing loads: The system must be able to be able to read high-definition sensors, process the information, and transmit the results to the ground.
- Weight and space savings: Lower weight translates into longer flight times and larger payloads. Space constraints are always an issue.
- Ruggedness: The system must be reliable, able to withstand harsh environments over long flight times.
Any one of those is easily accomplished, but achieving all involves compromises. Commercial systems run faster, but do not have the ruggedness required. The most rugged systems may not have the flexibility, scalability, or performance to meet today's data-intensive military and aerospace needs. Small, lightweight systems are easier to design if ruggedness and performance are not important.
VPX Has Right Mix
VPX, which supports speeds of 3.125 Gbits/s, 6.25 Gbits/s, and higher in a switched fabric architecture, is the latest generation of the venerable VMEbus and offers new levels of performance for embedded computer systems. VPX systems are designed for flexible application of demanding high-speed protocols, such as 10G Ethernet, RapidIO, InfiniBand, and HyperTransport protocols, in ground, aerospace, and marine applications.
VPX is a ruggedized approach to embedded computing that also relies heavily on commercial off-the-shelf products, fostering a wide international supplier base, shortening time to market and further feeding the ecosystem's evolution. Two other standards are important to the VPX ecosystem. VITA 65 defines OpenVPX, which establishes standard profiles for various configurations at the chassis, backplane, slot, and module levels. The goal is to create compatibility between products from different vendors to enable an open architecture and support two-level maintenance and system upgrades by allowing users to swap out line replaceable modules (LRMs) in the field. VITA 68 defines a VPX compliance channel including common backplane electrical performance criteria required to support multiple fabric types across a range of defined data rates.
Connectivity for VPX
VITA 46 is the founding architecture specification for VPX. It specifies TE's MULTIGIG RT 2 backplane connector from TE Connectivity (TE), with a focus on digital signals. As shown in Figure 1 below, the connector's design uses plug-in module wafer in place of pin contacts, an approach well established in commercial applications. Wafers-available for differential, single-ended, and power needs-can be easily modified to support specific customer needs for characteristic impedance, propagation delay, and other electrical parameters. The pinless backplane half of the connector assures protection of the backplane, thereby protecting the system, vehicle, and mission. Signal integrity has been elevated in parallel with the mechanical integrity. The ruggedized commercial VPX connector supports speeds up to 10 Gbit/s, providing plenty of margin to support VPX's standard speeds of 3.125- and 6.25-Gbit/s. The design is highly modular to support both 3U and 6U configurations.
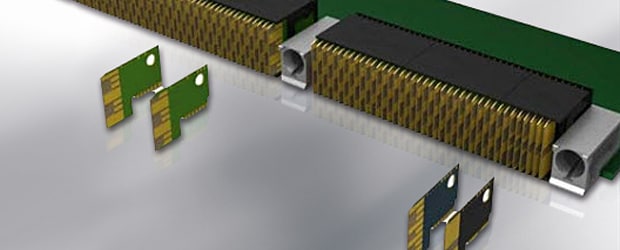
Several competitive connectors, defined by other VITA standards, offer footprint compatibility with TE's MULTIGIG RT 2 connectors, but not intermateability. TE's MULTIGIG RT 2 connector's wafer-based design and sturdy thermoplastic housing create a connector with a lot of air and very little metal-in other words, a very light connector. These are about 50% lighter than other connectors aimed at being VPX alternatives. The connectors are also very modular to give users greater flexibility in building 3U and 6U configurations. The modularity also permits the modules to be replaced by modules for RF, optical, and power needs. These also support both 1.25-inch and spacing-saving 0.8-inch pitches.
Rugged Beyond VITA 47
The VITA 47 environmental standard has long been the measure of ruggedness for embedded computing applications. It defines levels and testing for mechanical and environmental stress, such as vibration, temperature extremes, and other criteria important for reliability in harsh and challenging environments. While VPX/VITA 47 is the current standard for high-reliability, high-speed embedded systems, designers also want to migrate VPX into more challenging environments. UAVs expose components to vibration and wide temperature ranges, while the sophisticated processing required to handle such loads means embedded computers that run fast and hot. Conduction cooling and/or liquid cooling, as defined in VITA 48, may be required since the air at 20,000 feet up may be too thin for air cooling. To meet emerging demands for ruggedness and reliability, designers need new testing methods by which to measure performance. Testing conducted by the VITA 72 Study Group provides such an evaluation. TE's MULTIGIG RT 2 connector has been "up-ruggedized" further to meet the even more demanding requirements of VITA 72. Intermateable with the original design to provide an easy migration path from rugged to ultra-rugged, TE's MULTIGIG RT 2-R connector uses contacts have been redesigned so that each beam makes two points of contact - termed quad redundant - roughly doubling the contact patch area with the wafer. The new contact system may reduce mating forces by up to 10 percent while helping maintain reliable contact under extreme vibration levels. Because the two beams are not symmetrical to one another, each beam has different frequency modes in response to vibration, lessening the possibility of both beams being adversely affected simultaneously.
Creating a Rich VPX Ecosystem
The VPX ecosystem is rich, evolving to provide designers with an array of choices for single-ended and differential signals, mezzanine, power, optical, and RF connectivity. As VPX has evolved, new standards have been created to meet the widest range of interconnection needs. Figure 2 below summarizes the main interconnections now available for VPX systems from TE and shows a notional configuration of signal, RF, and optical possibilities on a single card edge.
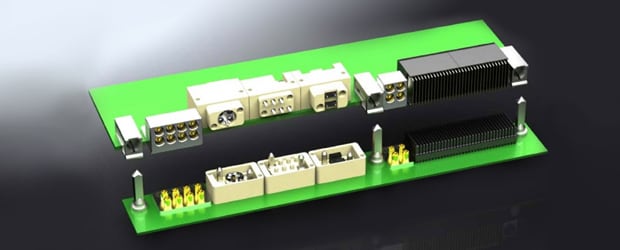
Not shown in the figure are VITA 61 XMC 2.0 mezzanine connectors. Mezzanine boards give additional plug-in flexibility for systems by providing for expanded functionality and modularity to a pc board. They allow existing boards to be re-configured, upgraded, or customized by the addition of the mezzanine card. Typical applications include application-specific high-speed input/output (I/O) protocols, graphics, memory, and digital-signal processing.
The VITA 67 standard specifies the SMPM series connector, chosen for the higher packaging density made possible by small size. The goal in designing the VITA 67 RF modules was to fit eight RF contacts into the space occupied by a single VITA 46 VPX signal module. The SMPM is a miniaturized version of the SMP series connector that is 30 percent smaller with similar performance and has a compact push-pull blind-mate interface. While the SMPM connectors have a maximum operating frequency of 65 GHz, the VITA 67 standard requirement is a frequency range of DC to 26.5 GHz.
Faster, Denser I/O
Fast processing by embedded computing also requires faster input/out speeds to help prevent communication bottlenecks. As I/O speeds increase, issues of signal integrity and power budgeting create new challenges. Simply put, high-speed signals are harder to manage than low-speed signals. The higher the interconnection speed, the more difficult it is to manage return loss, insertion loss, crosstalk, and similar factors that can degrade signals. While an ideal cabling system would have no intermediate connections between boxes, the real-world need for production breaks and modularity necessitates connectors in the path.
A poorly designed connector will appear as a significant impedance discontinuity. The impact of the discontinuity is frequency dependent-return loss and crosstalk increase with frequency-meaning that high-speed I/O connectors must be more carefully designed. Attenuation in the cable and insertion loss in the connector are also frequency dependent, making power budgets more challenging at high speeds.

Figure 3: Three 10-Gbit/s connector families give designers more choices in meeting SWaP goals.
Size, weight, and power (SWaP) issues remain tantamount to providing persistent surveillance, a better fuel-to-weight ratio, and the potential for smaller UAVs. While smaller, lighter connectors help meet SWaP goals, miniaturization can't be accomplished at the expense of signal integrity or robust ruggedness. Traditional nanominiature and microminiature connectors already exist, but were not designed for high-speed signals. More recently, connectors supporting 10-Gb/s data have arrived in packaging ranging from nanominiature to traditional MIL-DTL-38999 shells. Figure 3 shows a size comparison of three such connectors.
Fiber Goes the Distance
Even as high-data-rate copper-based connectivity is evolving, fiber-optic transmission is finding increased use. Creating location-independent architectures means different subsystems must not be constrained by cabling distances. Optical fibers have the well-known advantages of long transmission distances, noise immunity, small size, and light weight. Fiber optics has also made strides in easier use, ruggedness, and choice. The VITA 66 standard, for example, offers a choice of: Ceramic ferrules for the best insertion loss and return loss performance; Noncontacting expanded beam termini for increased ruggedness; and MT ferrules for high fiber counts of 12 or 24 fibers per ferrule and multiple ferrules per module. The same options are available for a variety of military-style circular and rectangular connectors. As VPX continues to evolve, it gives designers new levels of flexibility and capabilities in meeting the sophisticated signal-processing needs of UAVs. Adapting and evolving commercial interconnection technology has proven to be the preferred way to meet the ever-increasing needs of embedded computing. Commercial technology often leads in achieving new levels of speed and density, needing only to be sufficiently ruggedized to meet the stricter requirements of high-reliability applications. While such ruggedization of commercial technology may not be a trivial matter, it often provides a lower risk and faster path to market than starting from scratch. Rather than reinventing new technology, you need only demonstrate that the existing technology-already widely used-works in a more rigorous environment.