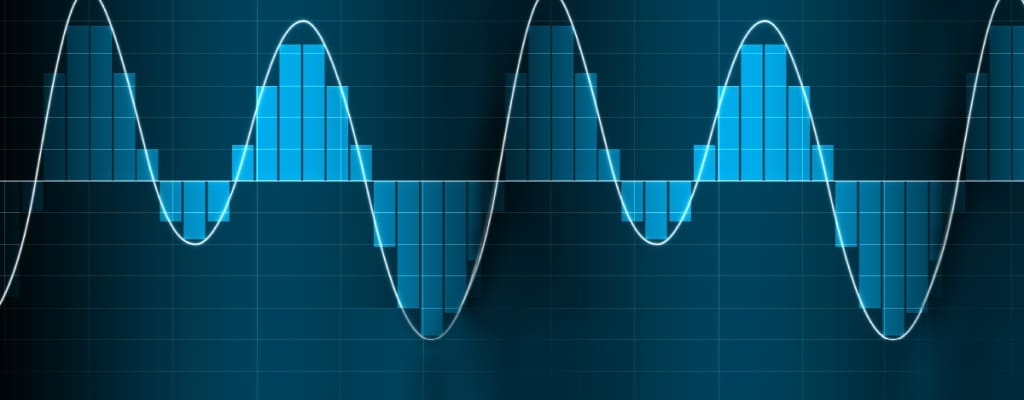
Trend Insight
Seven considerations for digital over analog sensors
Technology Comparison & Application Considerations
In the past, temperature sensing was primary performed by evaluation of analog sensor components like RTDs, NTCs or thermocouples. New use cases, like IoT (Internet of Things) support the implementation of digital temperature sensors in several industries like industrial controls, consumer devices, or medical instruments and systems. These requirements combine the ease of use with challenging performance and reasonable costs without the need for additional circuitries to bias the sensing components or determine the measured temperature. Additionally, no further calibration or linearization of the sensed signal is required to derive repeatable and reliable results.

Criteria Comparison to Analog Sensors
ACCURACY
ANALOG | DIGITAL |
---|---|
The total system accuracy must be considered since the measurement circuitry adds a certain error to the total error budget. Therefore, the stated accuracy of the sensing element is typically only 50% of the total error budget. | The sensor accuracy represents exactly the system accuracy since no further loss due to signal conversion is applicable. |
TEMPERATURE RANGE
ANALOG | DIGITAL |
---|---|
Ultra-low to ultra-high temperatures. | The usable temperature range of digital sensors is typically limited to -40°C to +125/+150°C. |
POWER CONSUMPTION
ANALOG | DIGITAL |
---|---|
Circuitries like current sources are used to bias the sensor component leading to a significant power consumption. Additional measurement errors introduced by self-heating also needs to be considered. | Power is primarily consumed only when measurements are taken. During power down states, there is minimal power consumption and negligible self-heating. |
DATA RELIABILITY
ANALOG | DIGITAL |
---|---|
The contact to the object to be measured and the lead resistance might impact the measurement accuracy and reliability due to degradation. Also, additional noise or drift of the analog to digital conversion are possibilities for erroneous readings. | The received data is either valid or null. Additionally, checksums (error detection algorithms) can be used to validate the memory content as well as the transmitted data itself. |
INTEGRATION EFFORT
ANALOG | DIGITAL |
---|---|
External circuitries needed to drive and evaluate the sensing component. Firmware to be developed to determinate the temperature with respect to the measured analog signals. | No additional external components needed except for a microcontroller with simple digital interfaces like I2C or SPI. |
SIZE
ANALOG | DIGITAL |
---|---|
Smallest sizes down to <1mm with two wire configurations available. | Ongoing reduction of silicon die and therefore package sizes. Package dimensions down to 1.5mm x 1.5mm. |
COSTS
ANALOG | DIGITAL |
---|---|
The total system costs consist of the sensing element itself accompanied with bias circuitry, quality A/D-converter, etc. | Digital temperature sensors are competitively priced and have declined in cost over the last few years. |

Measurement and Application Considerations
GENERAL
To achieve the most accurate temperature measurement results, below are our recommendations:
- Use a stable and noise free supply voltage
- Place a ceramic capacitor close to the supply pins (see datasheet)
- Keep supply lines as short as possible
- Isolate the sensor from any heat source which is not meant to be measured including electronics within the assembly.
- Avoid air streams if the PCB temperature is meant to be measured
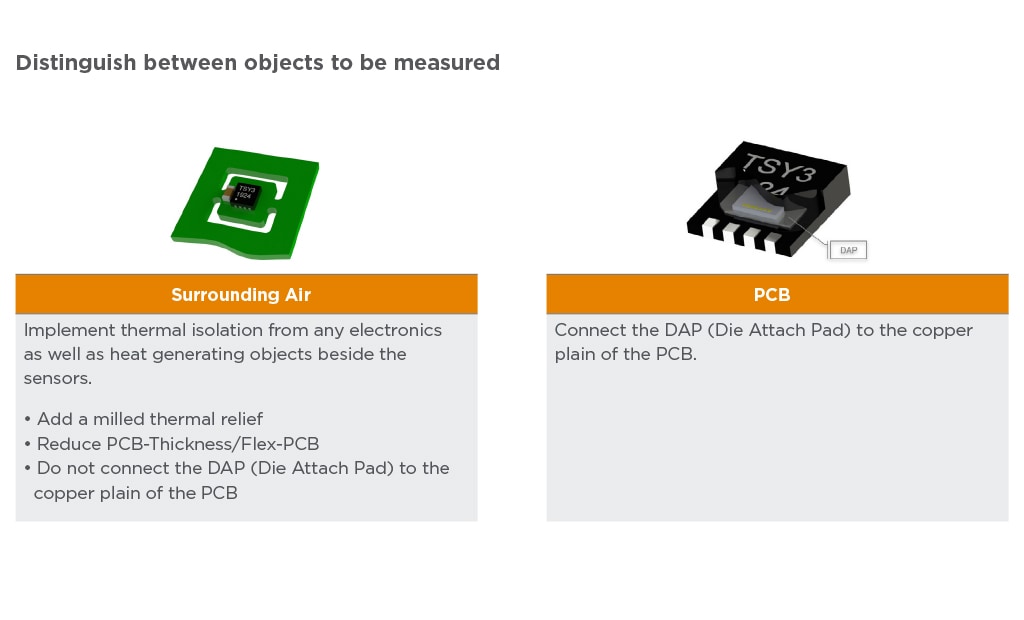

Self-heating
Self-heating is generated by the current consumed while the temperature measurement is performed. Digital temperature sensors, like TSYS03, limit this effect by low operating and very low stand-by current. Nevertheless, it is recommended to limit the measurement update rate to avoid self-heating and improve the life time for battery driven systems.
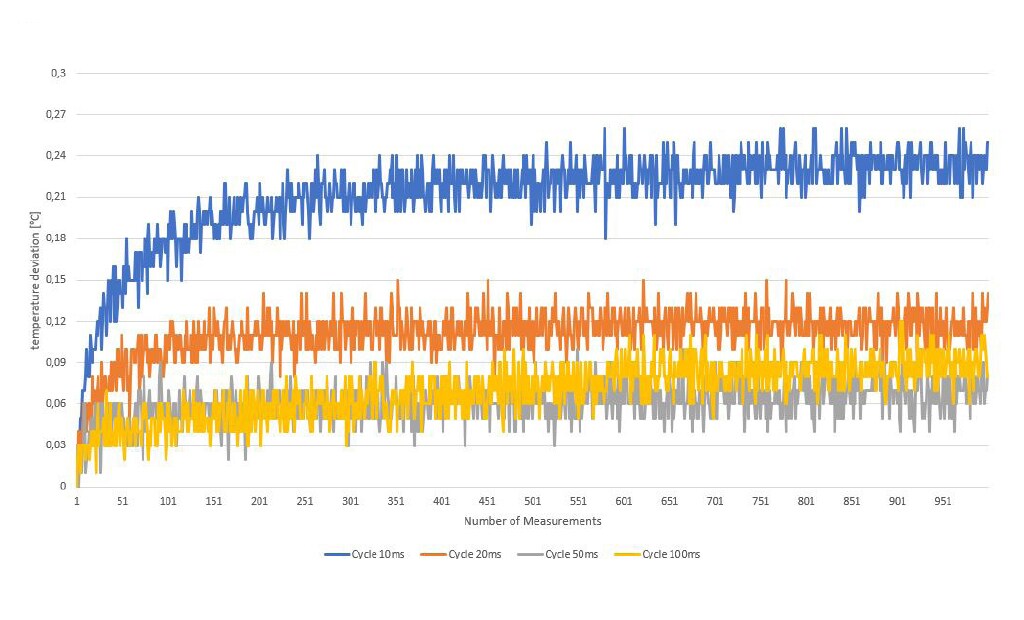

Time Constant
The resulting step response is determined by the thermal mass as well as the thermal conductivity of the sensor material as well as the medium the sensor is exposed to. Ongoing reduction of silicon die and therefore package sizes result in lower step responses. Both sensors were tested exposed to an air stream or a non-conductive liquid changing temperature from +25°C to +75°C.


Conclusion
Digital temperature sensors are a versatile solution to measure temperature in an accurate, reliable and costeffective way, meeting the demands of several applications and markets. TE Connectivity (TE) is one of the largest sensor companies worldwide, with innovative TE Connectivity Sensors that help customers transform concepts into smart, connected creations. Find out more about TE digital temperature sensor portfolio here.

