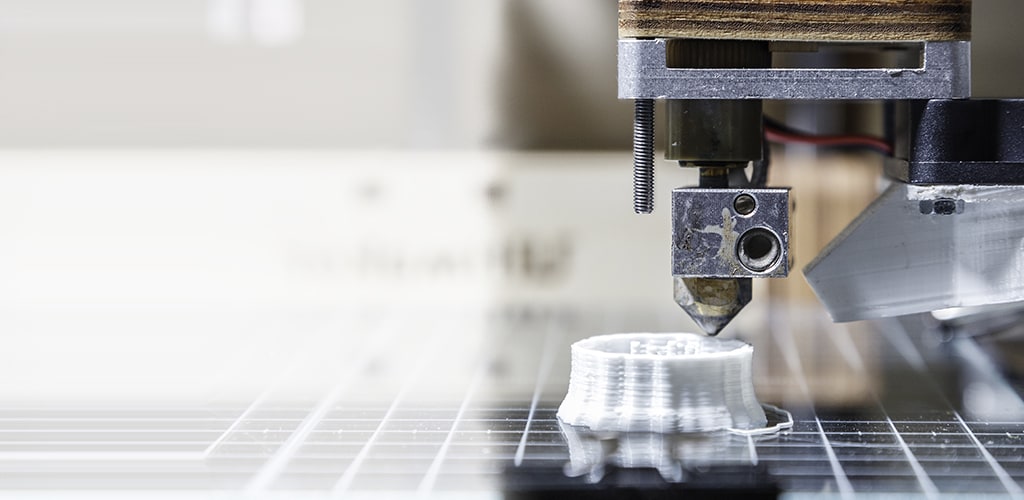
The Next Generation of Manufacturing Innovation
Conductive plastics provide a lighter, less expensive connectivity solution for next-generation electronics.
Authors:
Julia J. Wang, Staff Scientist, Composite Materials
Megan Beers, Staff Scientist, Composite Materials
From paper clips to food packaging, garments, medical implants, computers, automobiles, and spaceships, plastic products are ubiquitous. Thanks to low cost, light weight, easy and versatile processability, and outstanding resistance to moisture and chemicals, plastics have replaced many traditional materials, such as metals, ceramics, and glasses, in new product development in many industries. However, most plastics are electrically and thermally insulating by nature and therefore cannot be used as electrically or thermally conductive components in electric and electronic products. It is known that there are a few intrinsically conductive polymers (ICPs) such as polyaniline, which are promising for some practical applications, but in general ICPs have limited electrical conductivity and, unlike thermoplastics, cannot be melt processed.
Compared with metals, conductive plastics offer greater design freedom for product engineers.
Over the past decades many electrically conductive plastic products have been developed. These have included functions ranging from electrostatic discharge (ESD) prevention to electromagnetic/radio frequency interference (EMI/RFI) shielding and even signal transmission. These electrically conductive plastics are typically thermoplastics filled with electrically conductive particles, which take advantage of the benefits of plastics combined with the electrical conductivity of the fillers. Such electrically conductive plastics also generally exhibit improved heat dissipation over conventional plastics, although electrically insulating and thermally conductive plastics are of wider interest for applications in which thermal management is important, the examples of which may be found in automotive electronics, light emitting diodes (LED), and photovoltaics (PV). Both types of conductive plastics can be processed by conventional techniques such as injection molding and extrusion, as well as new additive manufacturing technologies such as 3D printing, into various form factors and sizes, (e.g., connector housings, ground planes, tubing and tapes). Compared with metals, conductive plastics offer greater design freedom for product engineers.
Challenges and Limitations
Conductive plastics are neither strictly metals nor plastics. As a matter of fact they exhibit lower conductivity than metals and compromised mechanical properties compared with plastics. Common electrically conductive fillers include: (1) carbon based materials, e.g., carbon black, graphite, carbon nanotubes, and graphene; (2) metals, e.g., silver, copper, nickel, tin, aluminum, and stainless steel, all of which are available in fibers, flakes, dendrites and spheroids; (3) combinations of these, (e.g., nickel coated carbon fiber, and silver coated aluminum powders). The challenges for electrically conductive plastics technology lie in the limited conductivity of the carbon-based fillers, the relatively high cost and weight of precious metals, and oxidation and corrosion issues with copper and aluminum, as well as the increasing difficulty in materials processing and the compromised mechanical properties of the materials at high filler concentrations. For electrically insulating and thermally conductive applications, typical fillers can be hexagonal boron nitride, aluminum nitride, and alumina, to name a few. The main challenge of the industry is to achieve high thermal conductivity, ideally isotropic, within the limits of the processability and mechanical properties.
Conductive Plastics at TE
The TE Connectivity (TE) Enterprise Technical Center Materials Group has developed a proprietary electrically conductive plastics materials platform. This platform is enabled by innovative intermetallic filler technology, judicious selection of polymers, and mastery of processing art.
TE's Electrically Conductive Plastics
Six Advantages
- High conductivity, up to 1% of International Annealed Copper Standard (IACS)
- Excellent processability, suitable for injection molding, extrusion, 3D printing
- Light weight, ~ 50% or more weight savings compared with metals
- Competitive cost
- Oxidation resistance
- Potential solderability
Benefits of TE's electrically conductive plastics. Compared with commercial materials in the industry, which typically use carbon black powder, carbon fiber, stainless steel fiber, or silver containing fillers, TE’s electrically conductive plastics are generally more processing friendly, have higher conductivity and functional performance, and provide significant cost savings. For electrically insulating and thermally conductive plastics, TE Enterprise Technical Center Materials Group has also developed materials that exhibit over 10 W/mK in-plane and up to 1 W/mK through-plane thermal conductivity, together with the processing know-hows for various applications. Our conductive plastic compounds are used in injection molding, extrusion, and 3D printing applications.
Conductive Plastics for Injection Molding Applications
TE has developed injection moldable grades of electrically conductive plastics and demonstrated their use in various applications. A variety of thermoplastics can be used with the proprietary electrically conductive filler package, while the conductivity can be tuned according to the target application requirements by adjusting the filler concentrations. The ability to be processed by injection molding opens up a wide range of application possibilities, including automotive, where environmental stability, weight savings, and mechanical performance are critical, as well as data and devices, where small and intricate form factors are often required in addition to high electrical performance.
An exemplary application of injection molded electrically conductive plastics is a connector housing with built-in EMI shielding functionality. Traditional methods for achieving EMI shielding functionality would be to employ metal shielding components by deposition, plating, stamping, etc., which can be costly and/or pose significant design constraints. Conductive plastics, on the other hand, offer a potentially cost-effective solution along with great design freedom. The housings can be molded separately, or over-molded directly onto current carrier structures. Alternatively, two-shot molding procedures can be used to incorporate the conductive plastic in specific areas of an otherwise electrically insulating plastic housing.
Functional testing of injection molded conductive plastic housings for a representative connector has demonstrated comparable performance to a metal shielded plastic housing. Figure 1 shows the insertion loss and cross-talk data for injection molded conductive plastic housings made from two different conductive plastics (red and blue curves), in comparison with a reference part made with a traditional insulating plastic housing and metal shielding. The conductive plastic housings provide nearly equivalent performance to the reference part.
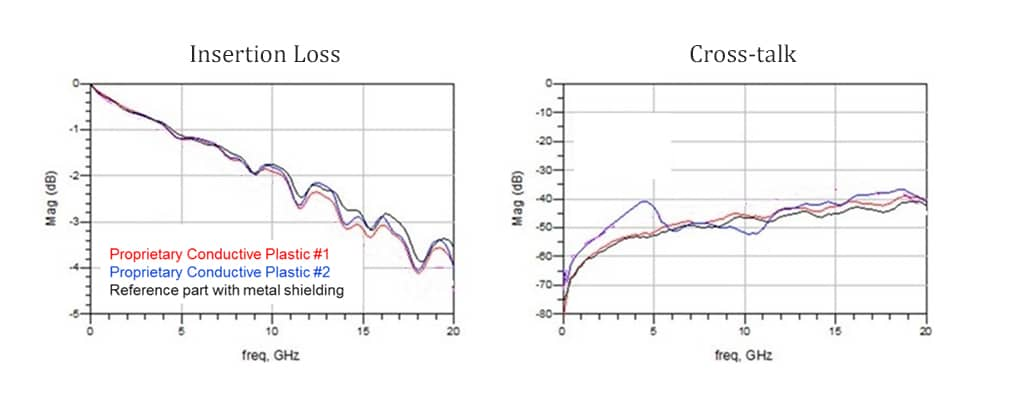
Figure 1: Insertion Loss and Cross-talk Data for Injection Molded TE Conductive Plastic Housings
TE has also developed electrically insulating and thermally conductive plastics, which can be injection molded. They have found potential applications such as connector housings and heat sinks, where new generation product designs often involve complex form factors and demand greater design freedom than what traditional metal components can offer.
While conductive plastics can be injection molded like traditional thermoplastics, it is important to keep in mind that the injection molding parameters can have a significant impact on the final conductive properties of the part. For example, the shear forces experienced during molding affect how the conductive particles are aligned and distributed in the material. This can lead to the conductivity varying throughout the part depending on the flow pattern, and also to the conductivity varying depending on the direction in which it is measured. Therefore, it is important to consider the specific functionality requirements in conjunction with the flow patterns that will be experienced during processing when designing the geometry of the part. And it is equally important to optimize the processing conditions to achieve the desired properties.
Conductive Plastics for Extrusion Applications
While it is well-known that the high conductivity of conductive plastics is often achieved with the drawbacks of high viscosity, rigidity and brittleness of the materials, there are relatively few discussions on the particular challenges that such drawbacks pose for extrusion related applications, such as conductive tubing and tapes. To make useful thin wall products by these continuous melt processes, it is necessary for the conductive plastics to have high tensile elongation and high flexibility, in addition to high conductivity, which is a big challenge for the formulation and the processing. In fact most commercially available conductive plastics are only recommended for injection molding applications and are unsuitable for extrusion related applications. Those available in the market for extrusion are mainly carbon black containing plastics, whose conductivity levels are often orders of magnitude lower than TE extrusion grade conductive plastics.
TE electrically conductive plastics for extrusion are homogeneous synergistic blends of selected thermoplastics, a proprietary conductive filler package, and other additives, accomplished by the combination of material science, polymer processing science and art. The resistivity and tensile elongation of the conductive plastic compounds can be tuned. For example, at a resistivity of 1E-3 ohm.cm, the typical tensile elongation at break value is around 300%, while lower resistivity or higher conductivity may be achieved at the expense of lower tensile elongation. The excellent electrical and mechanical properties of these conductive plastics make them great candidates for new generation product development in many applications, such as tubing, wire and cable, consumer devices, and so on.
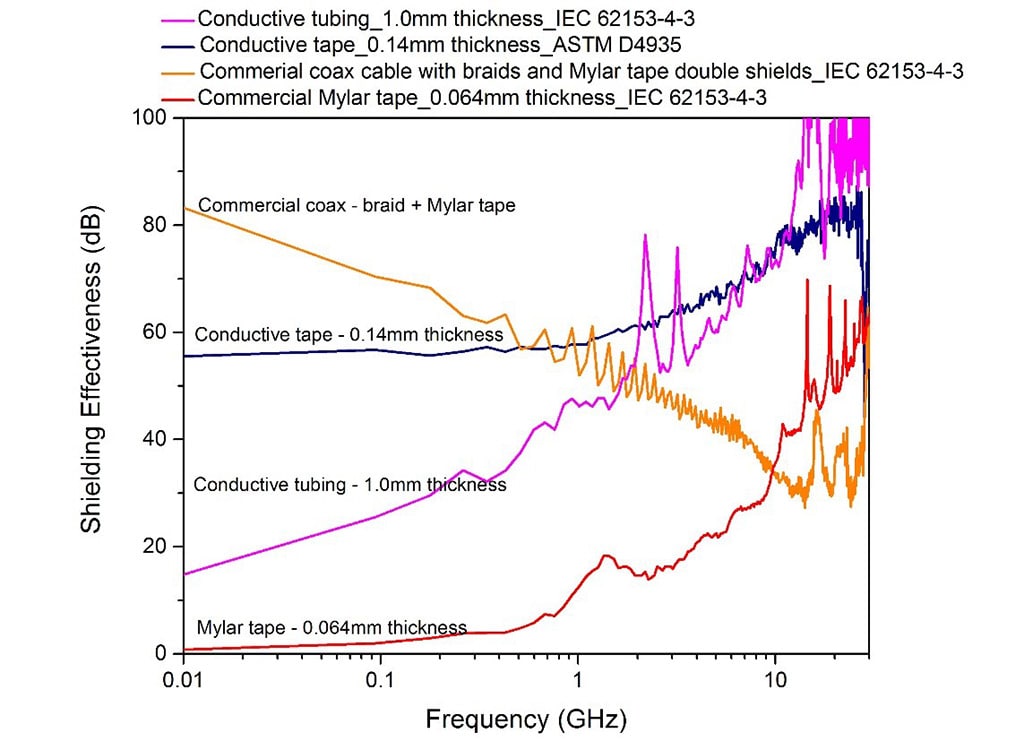
Figure 2: EMI Shielding Effectiveness of TE Conductive Tubing and Tape
As examples, the TE conductive plastic compounds have been extruded into tubing and tapes, which can be used as EMI shielding materials, alternative or complementary to the conventional metal braids and tapes in wire and cable products, with projected weight and cost savings. The shielding effectiveness data of TE conductive plastic tubing and tape are shown in Figure 2, in comparison with a commercial coax cable, double shielded by metal braid and aluminized Mylar polyester tape, as well as a commercial Mylar polyester tape alone. The results demonstrate excellent EMI shielding performance of the conductive plastic tubing and tape in the microwave/GHz frequency range, which is very desirable for today’s high speed data transmission devices.
Besides being made into tubing and tapes, the TE conductive plastics may also be co-extruded or tandem extruded directly onto wire and cable, taking advantage of the existing cable manufacturing lines and providing the opportunity to remove or reduce the braiding of conventional cabling process.
Another exemplary application of TE conductive plastics could be the solder-free joining of electronic components, to provide electrical continuity with a simple, inexpensive and residual-free solution.
As commonly understood by the industry, conductive plastics are prone to lose conductivity upon high shear, high drawdown ratio or expansion during the extrusion processes, due to damage of the filler morphology and/or the breakdown of the conductive network under such conditions. Besides the formulation science, mastery of the polymer processing art for highly filled systems is also required to achieve the desired properties.
Conductive Plastics for 3D Printing Applications
3D printing has become popular for rapid prototyping and even low volume manufacturing. Fused deposition modeling (FDM) is one of the most commonly used additive manufacturing processes and involves extruding thermoplastic filaments through a heated head and depositing the material into the desired structure. FDM-type 3D printing of conductive plastics, including electrically conductive plastics and electrically insulating/thermally conductive plastics, has generated a lot of interest for rapid prototyping of functional prototypes.
There are several different conductive plastic filaments for 3D printing on the market today. All of them contain carbon-based fillers, limiting their conductivities significantly. The most conductive filaments we have seen on the market have conductivities 5-6 orders of magnitude below IACS. The most conductive of these utilize expensive specialty fillers such as carbon nanotubes and graphene. The TE Enterprise Technical Center Materials Group has developed electrically conductive plastics for 3D printing based on a proprietary platform with conductivities up to 0.1% of IACS, a significant improvement over the currently available materials. TE has also developed 3D printable electrically insulating/thermally conductive plastics.
FDM printing poses several unique challenges for conductive plastics. The presence of the conductive particles may impede flowability through the nozzle in the heated head, leading to a tradeoff between flowability (larger nozzle is better) and part resolution (smaller nozzle is better). Furthermore, the inherent presence of boundaries between the layers of a printed part may decrease the conductivity of the part as well as other important properties such as mechanical strength. The printing parameters should be optimized to minimize these effects.
Building Next-Gen Conductivity
Conductive plastics provide a lighter weight and less expensive solution for new electric and electronic products. TE's Enterprise Technical Center Materials Group offers a proprietary platform of high performance conductive plastics, together with state-of-the-art processing know-hows in injection molding, extrusion and 3D printing. At TE, we are enabling customers to build the next generation of transformative technology.