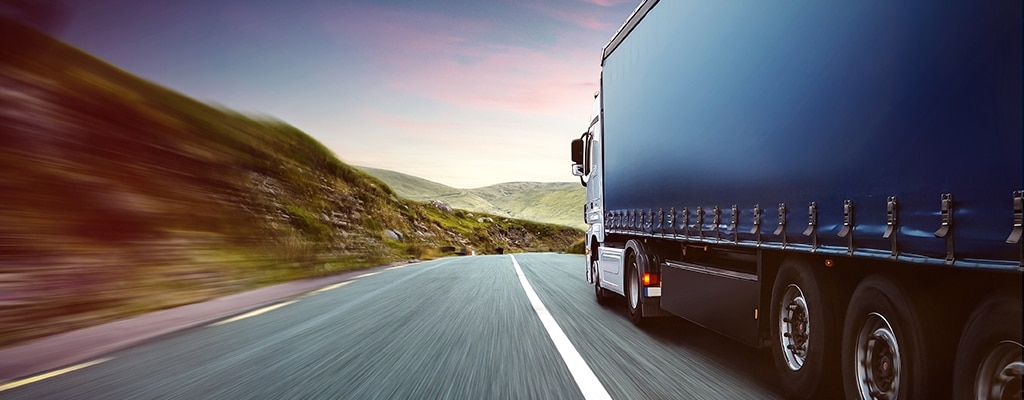
Trend Insight
AIR INTAKE COMBINATION SENSOR FOR ENGINE MANAGEMENT AND EMISSION REDUCTION
Recent environmentally-friendly standards and global demands for lower emissions and lower fuel consumption in gasoline and diesel engines require innovative combustion strategies whereby air intake humidity allows for closed loop monitoring.
Air intake humidity, temperature and pressure are three key parameters for engine management. It allows the user to find a balance in real-time between pollutant emissions, fuel consumption and engine power. One of the industry-leading combination sensors used for air intake humidity and pressure sensor is the TRICAN sensor from TE Connectivity (TE).

INTRODUCTION
The TRICAN air intake sensor is a humidity, temperature and pressure sensor designed and manufactured by TE Connectivity. This robust and mature off-the-shelf sensor answers automotive integration constraints, performance, and reliability. TE has sold over 12 Million humidity sensors serving the automotive, industrial, commercial truck, off road, and fuel cell markets. The first application was addressed in 2004.
Humidity control in air intake has demonstrated that the humidity ratio is conversely proportional to max pressure, engine torque, and NOx emissions.
Emission standards have become more and more severe over the years; less than 80mg/km of nitrogen oxide [1] are allowed for diesel engines as shown in figure 1.
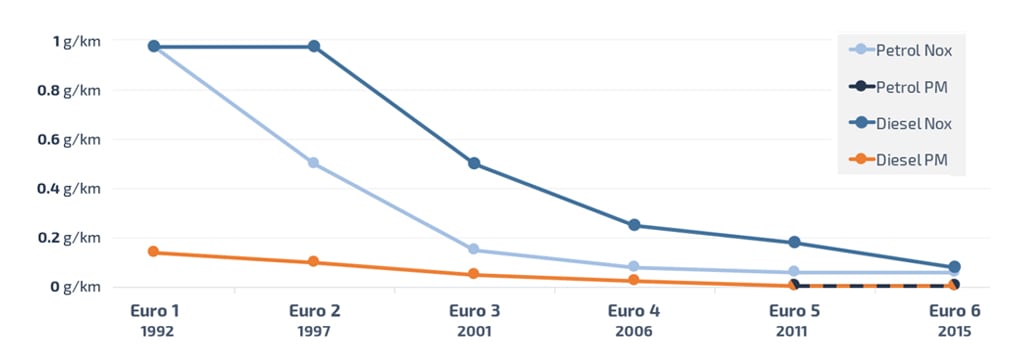
Figure 1: Emissions Standards Evolution
Air intake humidity control is one of the key technologies that enable vehicles to optimize the coordination of an air/fuel mixture and reduce exhaust gas emissions.

Humidity control in air intake has demonstrated that the humidity ratio is conversely proportional to max pressure, engine torque, and NOx emissions.
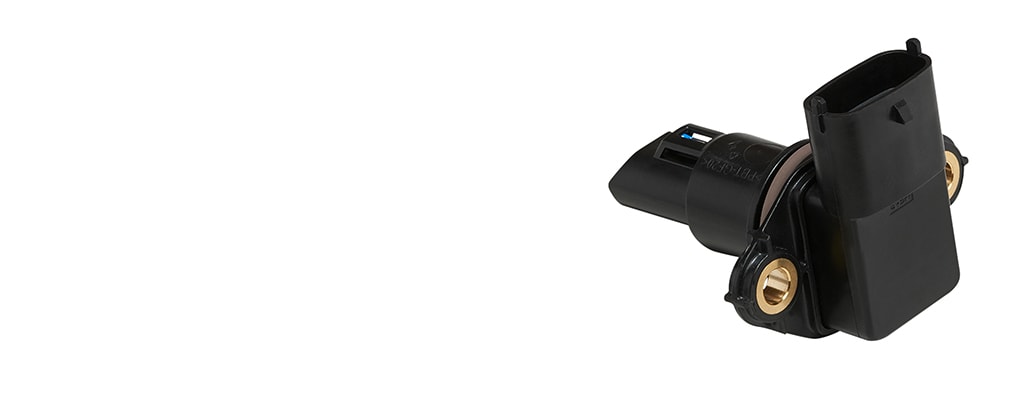

DEVICE DESCRIPTION
The TRICAN air intake sensor consists of a plastic housing, four-pin-connector and PCBA. The humidity cell accesses the air flow thru a PTFE membrane allowing the humid air to enter the cell and protect it from liquid contaminants or dust. The pressure and humidity sensors are designed and manufactured by TE Connectivity.
The TRICAN is a rugged, automotive-grade sensor optimized for high humidity and high temperature environments. It offers enhanced protection against pollution and quick recovery time after condensation, thanks to the heater near the humidity sensing element.
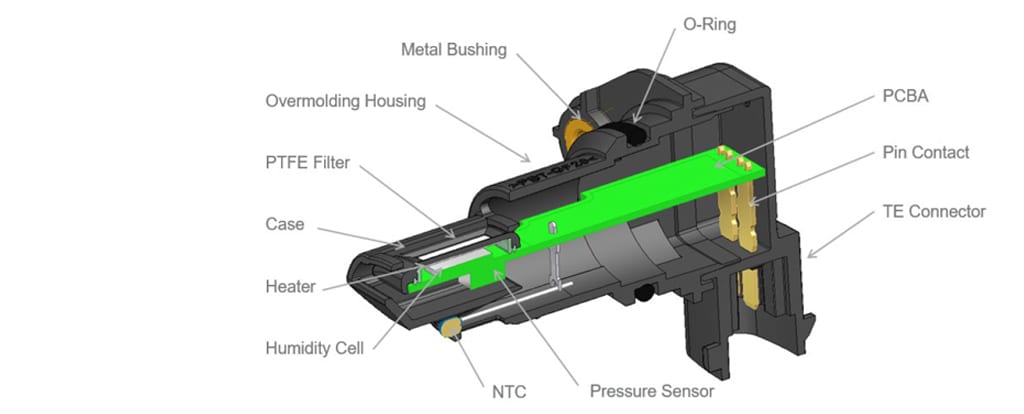
Figure 2: TRICAN sensor cross section
A signal conditioning stage is used on humidity and temperature signals allowing it to communicate a digital output. The pressure sensor ASIC communicates with the sensor microcontroller. The sensor has self-diagnostic capabilities where a status is published like short circuit, open circuit, or out-of-range diagnostic.
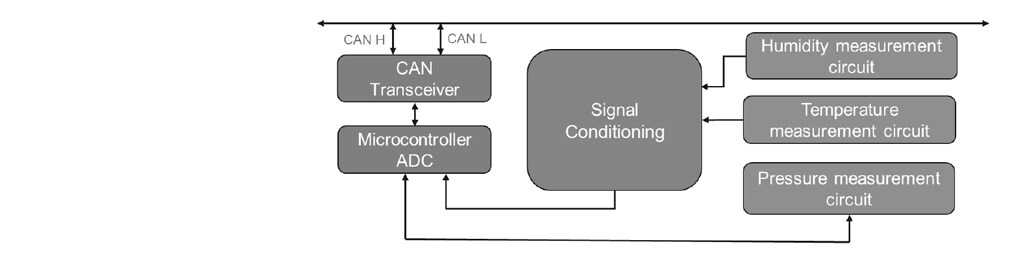
Figure 3: TRICAN sensor architecture
Sensor Output
The TRICAN sensor supports two-way-communication for system level plausibility diagnostic with another external sensor. Its digital output as per J1939, CAN2.0 can be configured to customer needs (CAN Frame).
TRICAN delivers relative humidity, specific humidity and dew point if requested. It also measures air temperature and intake pressure as shown in figure 4.
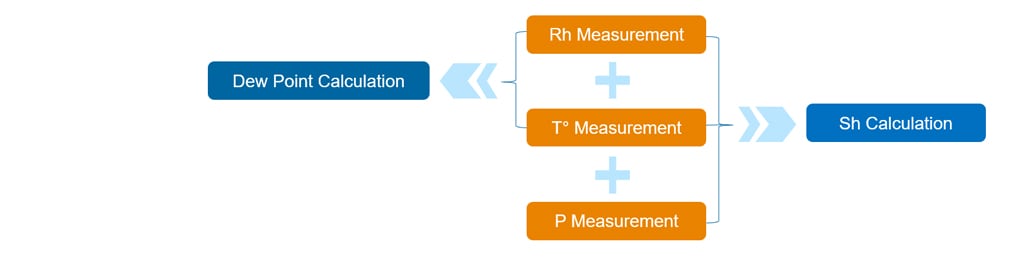
Figure 4: Specific humidity calculation
- Relative humidity (RH) is the ratio of the partial pressure of water vapor to the equilibrium vapor pressure of water at a given temperature.
- Specific humidity (Sh) is the ratio of the mass of water vapor to the total mass of the moist air parcel.
- Dew Point (DP) is the temperature to which the air must be cooled to become saturated with water vapor. When further cooled it will condense to form liquid water.
TE’s humidity cell is a unique high-performance sensor in terms of accuracy, robustness, response and recovery times. A thin dielectric polymer is trapped between an upper and lower electrode. The dielectric capacity is proportional to the measured humidity. Its position on the sensor allows for quick recovery time after condensation and strong protection against pollutants at the same time. Our humidity sensor offers one of the lowest hysteresis and fastest response time on the market today.
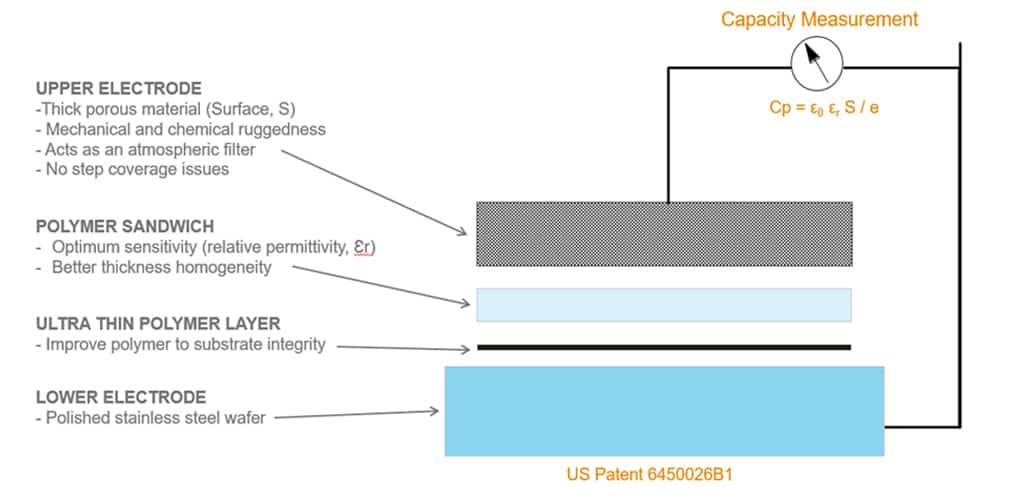
Figure 5: Humidity cell architecture

SPECIFICATIONS AND PERFORMANCE
The sensor offers a digital output with self-diagnostic capabilities. Its operating temperature range is from -40°C to +105°C and the humidity range is 0% to 100%. Three TRICAN versions allow for different power supplies; 5V, 12V and 24V.
Humidity Sensor Characteristics
Figure 6
TE’s pressure sensor is developed especially for ICT air intake. Its operating temperature range is from -40°C to +125°C and offers a pressure range up to 250kPa with very quick time response.
Pressure Sensor Characteristics
Figure 7
The temperature sensor is a negative temperature coefficient (NTC) soldered on the PCBA. It offers a temperature measurement range from -40°C to 105°C with an accuracy of ±0.5 °C.

TRICAN APPLICATIONS
The TRICAN sensor is used in different applications where humidity, pressure and temperature need to be monitored with high accuracy and quick response time. Main applications include:
Engine Management for Diesel and Gasoline
Humidity is known to affect air intake density thus affecting combustion [3, 4]. EGR loop adds humidity to the air intake. Humidity, temperature and pressure sensors allow for performance enhancement and fuel consumption optimization. It offers the following advantages:
- Injection adaptation
- Ignition timing adaptation
- Monitoring of EGR condensation to prevent from cylinder lifetime reduction
- NOx emissions reduction
- EGR loop control optimization
Engine Management for Natural Gas
In natural gas engines, maximum achievable power is a function of air intake humidity. An accurate air/fuel ratio in lean-burn engines is essential.
The excess of air reduces combustion temperature thus nitrogen oxide emissions reduced by half compared to a conventional NG engine. With the excess of oxygen, the combustion is more efficient because more power is produced from the same amount of fuel.
Lean-burn limit is a function of humidity and must be adapted in real-time to:
- Improve efficiency
- Reduce NOx emissions, knock & misfire
Virtual NOx
Virtual NOx estimation allows for high cost reduction due to the removal of the upstream NOx sensor. One of the major advantages is that the TRICAN accuracy is high even at cold start conditions where 50% of the driving cycle’s emissions are generated during cold start where NOx sensors are not efficient for at least 20 minutes. In these specific conditions, emissions are the highest and require a specific strategy.
In addition, temperature and pressure sensors at the intake can be replaced by the TRICAN allowing additional cost reduction.
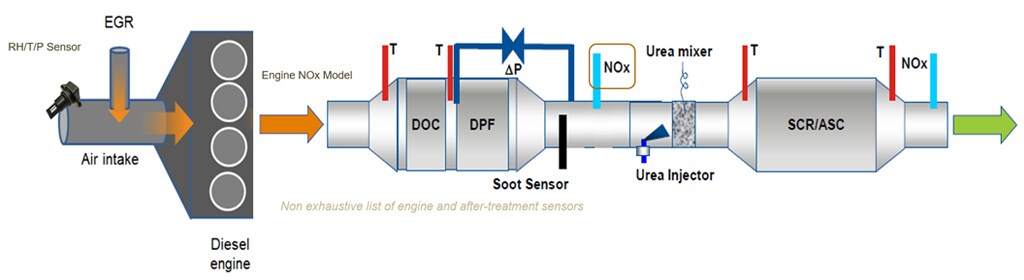
Figure 8: Engine architecture
Our humidity, pressure and temperature sensor completes or replaces upstream NOx sensors. It offers high accuracy, high reliability and limited drift over its lifetime. It is also used in an engine model in combination with upstream NOx sensor to offer system diagnostic capability and to monitor NOx accuracy over lifetime.
Fuel Cell
Optimum fuel cell performance requires High relative humidity or nearly saturated humidity (Rh>80%) is required to fuel cell performance. Proton Exchange Membrane permeability depends on its water content; therefore, relative humidity is one of the most important operation conditions affecting fuel cell performance and efficiency over the stack’s lifetime.
A humidifier is used at the inlet of the fuel cell to correct humidity rate. One of the main challenges for the sensor is at cold start when condensation can occur. Field experience in harsh environments such as trucks, construction machines and on/off-road applications where TE’s humidity cell is used, have proven to be a reliable solution which offers fast recovery time after condensation and high response time. Pressure is also a key parameter for power density control. The TRICAN sensor is thereby suitable for high humidity and temperature environments. Additionally, the sensing elements are protected against chemical contamination.

HUMIDITY IMPACT ON COMBUSTION ENGINES
As described in the previous section, air intake humidity affects engine efficiency in terms of max pressure [2], torque and pollutant emissions. The following section refers to an experimental study on a Renault K4M-700 four-cylinder gasoline engine, where specific humidity influence on engine torque and emission gases is highlighted [5, 6].
Humidity Impact on Engine Torque
Due to combustion speed reduction, cylinder max pressure decreases when specific humidity increases. As shown in figure 9, engine torque decreases by 5.5% when specific humidity increases from 10 to 40g/kg due to max pressure reduction. For conditions where specific humidity is 15 g/kg, if the measurement varies by 5g/kg, engine torque will drop by 1%.
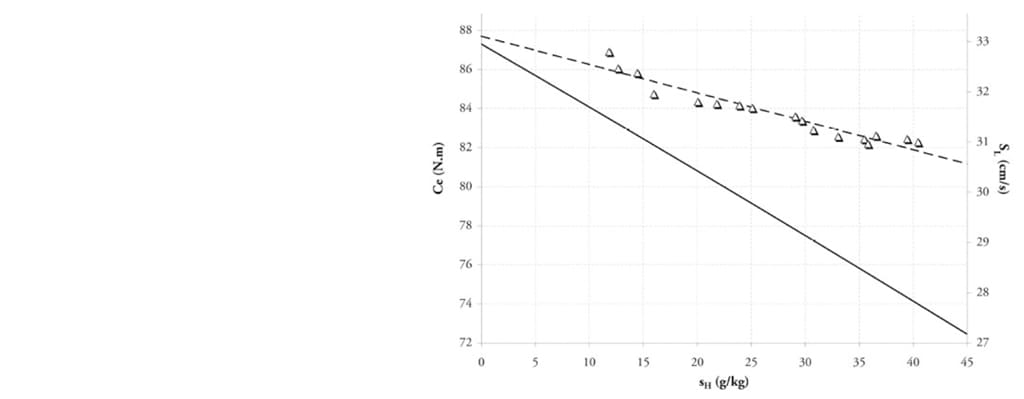
Figure 9: Engine torque as a function of intake specific humidity
Humidity Impact on Emissions
Hydrocarbon emissions arise from unburned particles due to wall extinction phenomena. They increase when air humidity increases, while carbon dioxide and nitrogen oxide decrease when air humidity increases.
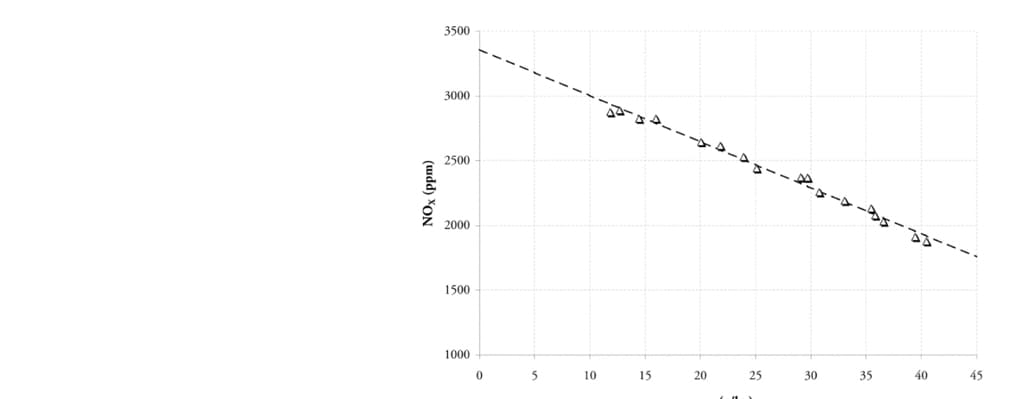
Figure 10: Nitrogen oxide as a function of intake specific humidity
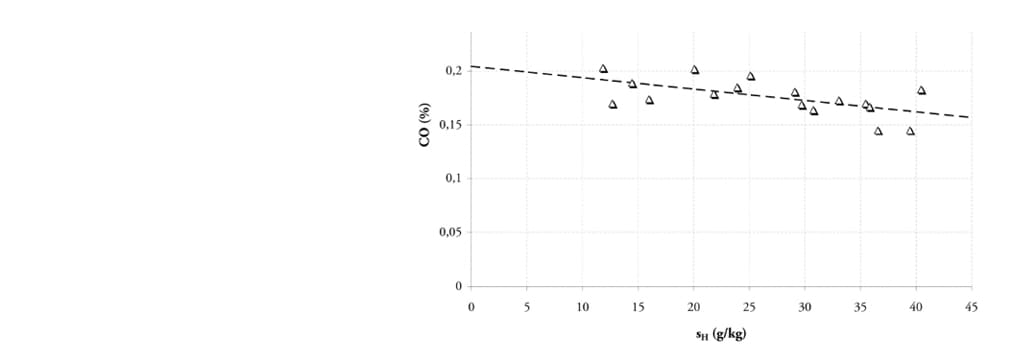
Figure 11: Carbon oxide as a function of intake specific humidity
For conditions where specific humidity is 15 g/kg, and the measurement varies by 5g/kg, the emissions impact is: 1.5% more hydrocarbons, 7.2% more nitrogen oxide, and 5.4% more carbon dioxide.
Adiabatic end-of-combustion temperature affects the amount of heat released during combustion and thus the work done by the piston which affects engine power.

CONCLUSION
Specific humidity monitoring is a key factor for engine management and fuel cell performance. Several advantages for humidity sensing devices have been demonstrated. It allows for accurate close loop control. High accuracy over temperature range is mandatory to meet emissions regulations.
Air intake humidity affects burned gas composition and pollutant emissions. Nitrogen oxide and carbon oxide emissions can be decreased by accurate monitoring of specific humidity.

REFERENCES
[1] caremissionstestingfacts.eu
[2] Influences of Charge Air Humidity and Temperature on the Performance and Emission Characteristics of Diesel Engines, Cherng-Yuan Lin, Yuan-Liang Jeng
[3] Advanced Combustion for Low Emissions and High Efficiency, Cracknell, R., Ariztegui, J., Barnes
[4] Water addition to gasoline, effect on combustion, emission, performance and knock, J.A. Harrington
[5] Etude numerique et experimentale de l’influence de l’humidité de l’air sur la combustion. Application aux strategies de reduction d’émissions polluantes et de consummation des moteurs à pistons, Yannick Duhé
[6] Effect of Ambient Temperature and Humidity on Combustion and Emissions of a Spark-Assisted Compression Ignition Engine, Yan Chang, Brandon Mendrea Jeff Sterniak, Sranislav Bohac
