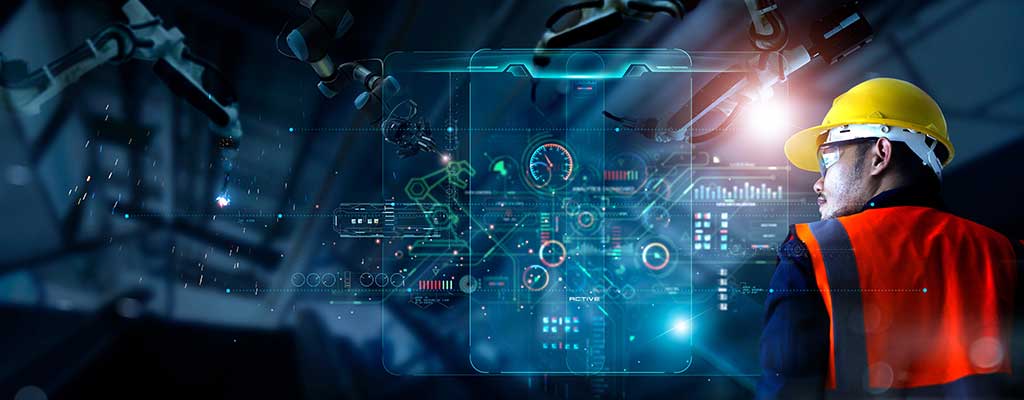
Which robot is right for your production environment?
Developing scalable automation solutions for increasing factory productivity and efficiency involves identifying the right type of factory robot.
Industrial robots increase factory efficiency and production by automating repetitive processes operated at high speeds. These programmable technologies are enabling operations supporting industrial IoT (IIoT) networks, artificial intelligence (AI) systems, business process management (BPM), and robotic process automation (RPA). Before investing in these technologies, it is helpful understand the functions which robots perform in the production environment.
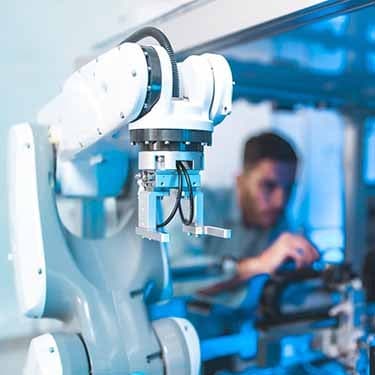
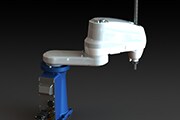
SCARA robots
SCARA robots have two parallel rotary joints and specialize in lateral movements. SCARA robots are well-suited for assembly applications as well as inserting parts into single-plane structures such as circuit boards. SCARA means Selective Compliance Articulated Robot Arm.
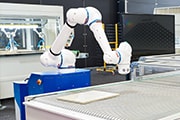
Articulated robots
Articulated robots are the most used industrial robot, accounting for around 60% of installations worldwide. They resemble a human arm and have a structure similar to shoulders, elbows, and wrists. Articulated robots have between two and ten joints, which provide flexibility to accomplish dynamic tasks. The arm may be attached to a gripper, which is analogous to a hand. The gripper can range from simple suction cups to complex options such as drill bits, lasers, and other specialized equipment. Articulated robots are used in many applications, most commonly for printing, packaging, welding, metalwork, machine tending, and material handling.
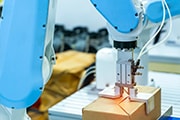
Cartesian robots
Cartesian robots, or linear robots, operate along three perpendicular axes: forward and backward (X), up and down (Y), and side to side (Z). Because their axes move in a straight line, Cartesian robots offer high accuracy, cost-effectiveness, and simplifies control systems. They are frequently used for material handling, 3D printing, loading and unloading machines, palletizing, drilling, welding and assembling products, and storage or retrieval.
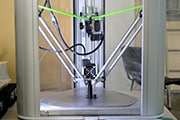
Delta robots
Delta robots have jointed parallelograms connected to a triangular base mounted above the workspace. Their three arms, controlled by motors, enable movement within a dome-shaped area. Their lightweight design allows for high-speed and high-precision applications that require a broad range of motion. Delta robots are commonly used in pick-and-place operations. Other uses include complex assembly tasks, dispensing materials such as adhesives and sealants with a very high degree of control and precision, and high-speed packaging, such as placing boxes and bags onto pallets for shipping and storage.
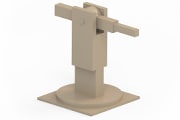
Polar robots
Polar robots, also called spherical robots, have an arm attached to one linear joint and two rotary joints that are connected to a base with a twisting joint. Cost-effective, these mid-20th century robot types operate using polar coordinates, offering a spherical range of motion. These are frequently used in die casting, injection molding, welding, and material handling. These robots are sometimes replaced by more versatile options such as articulated robot arms.