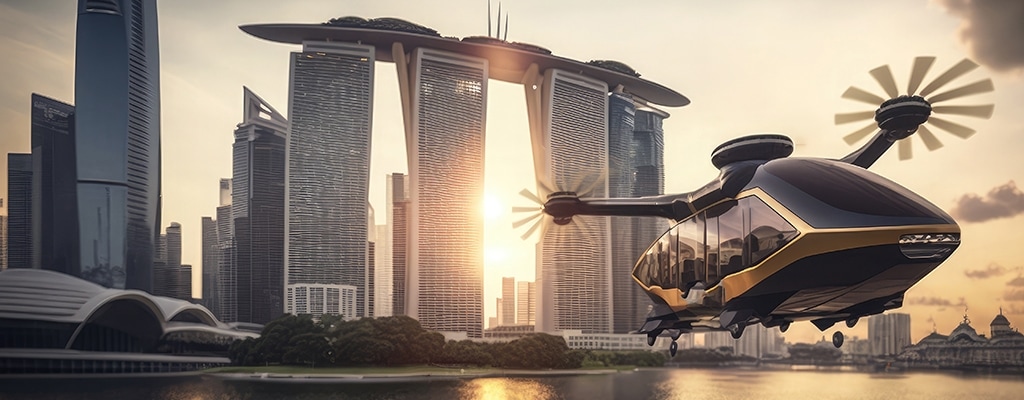
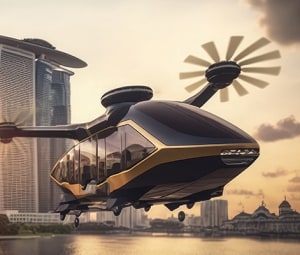
We’re still in the exploration phase... still seeing innovation in how these aircraft are going to be configured and put together. ...There’s still innovation at the system level and we will, I think, see in the very near-term innovation coming down to the component level as well.
March 4, 2024
Innovation in eVTOL technology is addressing the practical operational and maintenance needs crucial for operability and serviceability. This is happening most crucially in charging infrastructures, battery technologies, and remote services. The focus is scaling the technology for global adoption. In this interview with Martin Cullen (TE Senior Manager, Business Development, Aerospace) and Matt McAlonis (TE Engineering Fellow, Aerospace), they share insights on the challenges system architectures, the maintenance requirements for operating eVTOLs, and the need for regulatory and infrastructure standardization to support global adoption.
Where is innovation happening in eVTOL architectures?
Martin: These eVTOL designs have been in work for a good number of years to certain degrees of maturity with each different manufacturer. We’re still in the exploration phase to understand what these architectures are going to be looking like. We are still seeing innovation in how these aircraft are going to be configured and put together. Evidently, still the prime source of innovation is in the battery technology. Whether it’s cell chemistry, or battery packing, how you connect that to the rest of the electrical power system. There’s still innovation at the system level and we will, I think, see in the very near-term innovation coming down to the component level as well. At the moment, it is still at the system level, very much focused on the battery. And what’s past that stage, as a certified aircraft, we’ll see the second stage of looking at the component and how that can be innovated for future benefits.
What does maturity in eVTOL architectures look like?
Martin: It’s converging. Like I said, there’s so many different configurations out there and there’s different applications where you see an optimized air frame, optimized configuration that will fit better in some of these cases more than others. And over time we’ll eventually see a convergence of what the best configuration is for that particular use case. We have things to think about, like. Redundancy. What is the redundancy of systems in each of these configurations? How you have dual or triple systems between individual power packs and most of the inverters. How you control that through the PDUs, the power distribution units. There’s still going to be some optimization, some innovation on that level of architecture, including the charging system. We’re seeing different systems where there’s one, two, or four chargers on the aircraft. How that is managed, how different failure systems are managed is still yet to be worked out. We’ll see some convergence of optimized design as the aircraft is used the first two or three years of operation.
What must be addressed before eVTOLs are a viable technology for mass transit?
Martin: What we have to consider here, first of all, is what is mass transit. The eVTOL is not there for mass transit. That’s going to be your buses, coaches, and trains. That’s what mass transit is. What we will see are different mobility routes that come out with eVTOLs. Going across deserts, or lakes, or mountain regions. And as we start seeing those use cases, you have to think about how are these aircraft going to be maintained, serviced out there at the Point B destination. You’ve got to think about infrastructure, you have to think about repair, services and the people who are going to be doing it. You have to think about how they’re going to get components and other repair equipment to these locations.
Physically it’s a bit of a catch 22 of understanding how these aircraft are going to be operated, what kind of infrastructures and people you need at these locations. And then how you’re going to expand that to different areas, different routes. It’s going to be a bit of a catch 22 involving capability needs, as these operations are explored essentially. Again, with all of this domain, from components and subsystems to the airframes to the actual in-service operation and how passengers are going to get onto the aircraft. I think it’s still going to be a bit of ‘find out and see’ when the rubber hits the road [better analogy; as things take-off].
How can this be addressed without compromising the design?
Matt: There is a lot of technology that is new and pure electric propulsion is something that needs, in space and aerospace terms, a technology readiness level to be considered reliable and repeatable. Some of the things we’re looking at in some of these new aircraft are things like flexing and articulating motors, which most aircraft have a static motor on there. We make a lot of things like wire and cable systems that aren’t initially designed to have that type of flexure in them. There’s innovation happening with the types of aircraft, the design of aircraft. We need data to understand what maintenance looks like. Right now, when an aircraft lands it goes through some routine inspections but inspecting things like the cables typically isn’t part of the process today.
As we think about draining a system, so to speak, and even the ranges of these batteries, the electrical integrity of electricity on the top of the charge and the bottom of the charge is different. How far down can you take your batteries and still be capable of an emergency loop or a redivert? As we think about the electrical systems and getting data on these systems is very important to get to that technical maturity level.
What do you think is limiting OEM capacity and adoption at scale?
Matt: When you think about these early nascent designs that are just starting to fly, one or two aircraft are flying in service, we live in a highly regulated industry. And it has to be because if you have a failure, it could be fatal. It’s not just the crash of the aircraft. It’s also when high power electricity is used and fails it is very explosive and dramatic. When you think about the lightning bolts that – if you have a failure that could occur – you need to keep things safe. There’s a lot of new technology; power levels that typically haven’t been seen before. They’re typically in the range of three times in terms of what our current aircraft are seeing in terms of the voltages. With these high-voltage systems, we have to make sure we have the right testing to make sure the systems are safe and reliable, and again understand that maintenance. When you push innovation, you really need to understand not just how it works but also how it fails. What are the degradation mechanisms that need to be looked at.
When you think about scaling – so scaling and building these aircraft are different. The manufacturing processes and methods are new. How we wire them and install electrical motors versus traditional aircraft engines is different. Those are things that we have to have new processes, like how do I have to take my batteries in and out, that’s not part of the standard maintenance. Or how do I inspect some of these systems. This all has to be studied, it has to be approved by the FAA, and we need the ground maintenance infrastructure to be available as well. You have new types of mechanics and technicians that have to be trained. There are so many things that need to be certified. When you think about aerospace in general, there are several types of certification. One is your design, one is how you make it, one is how you test it, and one is how you use it in operations. All four of those areas have to be considered and have confidence in them.
How might these advancements affect connector design going forward?
Matt: Electrical connectivity is essential here. What we do with customers is we put a schematic together from the charger to the energy storage area to the power switching area, the whole way to the inverters and motors and all that connectivity in between and how they manage their harness. When you think about all that content, that’s weight. The first thing we look at is to make sure it’s weight optimized. There are different things like the geometries we play with and how that can conduct electricity more efficiently and amperage more efficiently. We have to look at the electrical fields around these components. We want to make sure that they’re light as possible, but they have to be as robust as possible. If something like a charger is being mated to every time, that doesn’t necessarily have to be, that’s not being charged in flight. That’s not as a concern for vibration for us, but the things that are connected to the battery that have to be reliable in flight, that’s where we typically will focus and optimize those things.
When we deal with flight, we also have things like takeoff, landing, cruise where we’re looking at all the different vibration profiles and the current carrying profiles during different situations in flight. We do thorough analysis on these things, but again we try to use our engineering analysis tools and simulation tools to make sure we have optimized product. Weight is the thing that is very different with conventional aircraft, where you’re burning fuel. Your batteries don’t get any lighter when they discharge so you’re literally carrying around dead weight. That’s an area we really have to focus on is our materials we use for weight reduction.
What is needed to stably maintain eVTOLs over time?
Martin: Again, I think that’s a place where we don’t have all the answers. There’s a lot of experienced helicopter operators have been operating for decades in remote locations. They have a good understanding but when it comes down to high voltage applications that fly in harsh environments, there’s going to be unique instances that they’ve never experienced before. A lot of these aircraft have tilt rotors. You have bearings now moving, you have cable that is flexing. These aircraft are flying in sand and dust environments. Sand gets everywhere. Dust gets everywhere. So how does it get into the aircraft and how is it going to impact its operation? There’s a lot required for repair and maintenance for any aircraft. It comes down to what processes do you have, what people do you have? Do you have a supply chain in replace for repairs? It takes up to four years for an aircraft mechanic to be certified. What training is there for an electric aircraft mechanic? Is there a certified eVTOL mechanic out there? I don’t think so. Because we’re still going through that process. I think we need to bring across the experience from the helicopter operators. We have to look for potential weak points of the aircraft that we think we can apply our knowledge and our help to design these aircraft. And also, how can we support the considerations about the design for repair. Access, for example. How you disconnect quickly and easily and how you get to the right level of maintainability for these aircrafts. We’re going to have to learn as we go in these instances.
What operational and maintenance needs to be defined?
Martin: What comes to mind to me is inspection. You’ve probably seen pilots go around the aircraft before takeoff to do a safety check on the aircraft. If you’ve got a PPL – private policy license – you fly yourself. The first time you fly in the aircraft you have to do a thorough check. The second time you fly the same day, you can do a lower-level check. What level of inspection is going to be required before you take off with your passengers? How are you going to monitor the ingress and egress of passengers that could damage the propellers or another part of the airframe? The required regular inspection and the number of safety checks before you fly each time? There’s going to be quirks, there’s going to be distinct requirements on these aircraft that you won’t see elsewhere, from inspections of let’s say propeller tips all the way down to looking at the electrical system itself. I think that’s the first thing that we need to get understood in this industry.
What operational and adoption concerns are top of mind for OEMs?
Matt: I think it’s similar to the automotive EVs of today, which is charging. When you need to charge where you land – these are very portable aircraft that could land anywhere there’s a flat space – the question is how much charge is left to get you to a charger. And then when you land, what kind of charger is there? There’s a really interesting thing we learned last week at the Vertical Flight Society event – The Transformation of Vertical Flight – and it was about chargers. Two companies emerged and said, “Pick mine.” They had different interconnects; they had different systems. And you want to charge as fast as possible. But when you charge fast, that means it gets very hot. And if the connectors are hot, and if the batteries are getting hot, where are the batteries located? In some of the designs we’ve seen, batteries are literally surrounding the passengers. We’ve seen batteries that are up in the wings. So can you imagine how that will look like if you’re in a fuselage waiting to take off and it’s getting very warm and uncomfortable.
There are things like that which are still going to be thought through. There’s a lot of work needed to supply this power. You have the physical infrastructure on the ground, if you’re landing on a roof, is that building wired for this megawatt type of charging system that’s needed? It’s probably not today. There’s a lot of things like that which need to be worked through. The other question I would think about is can you even charge in the rain, and what does that look like? There are so many new things that will have to be vetted out before the operational is certified.
What can manufacturers do to make eVTOLs feasible long-term?
Martin: In terms of service and repair and operations, as Matt touched on, it’s standardization, particularly of charging and the infrastructure required. That can be from the particular mating profile of the charger of the connector, to the data download, the CAN bus protocol for instance that might be used. We’re kind of familiar with OBD2 in automotive. Do we have something similar in aerospace that is standardized? Do we have a common way of using the same charging system protocol but with different charging inlets amongst eVTOL aircraft types themselves? Are there any security type concerns of connecting these aircraft to chargers, maybe some that are remote or even part of a busy area?
There’s the security aspect, there’s the data integration, the standardization of charging, standardization of operations. If we look at current commercial protocols, you cannot refuel while passengers are onboard, for example. Does that mean you cannot charge your electric aircraft with passengers are onboard, or how far do they have to be away from it? There’s some regulations and standards that have to be put in place and well-communicated to put in the design of these aircraft, and also help the operation processes be quick and allow these aircraft to operate as intended.
What does the charging infrastructure look like for eVTOLs?
Martin: Matt kind of touched on this with the different types of proprietary IP charging elements. I’ve seen many companies come to market with their idea of charging units, remote charging units at large airport locations through to remote helipads or parking lots or the top of skyscrapers. It hasn’t been implemented yet. There’ve been trials done and experimentation done with these. I think it depends on each case. If you’re shuttling back and forth from an airport, then you can use the airport facilities. That’s fairly straightforward. They have a good infrastructure of high-power connectivity there. When you start looking at remote vertiport and if they’re charging somewhere, how do you put infrastructure in there? It can’t be heavy; it has to be lightweight. You need to have it without much maintenance. Just as these platforms may be individualized for use case, I think you’ll see a charging infrastructure be optimized for particular use case as well.
What are challenges to making this infrastructure available at scale?
Martin: Again, I think we touched a little bit about standardization. How can we be certain that we don’t end up in a BetaMax-type situation where everyone’s investing huge amounts of infrastructure into one type of connector, one type of charging system? How can we be brave enough to provide the numbers that are going to be required? Because as we all see today, traveling from the west coast to the east coast in the USA, or traveling through Europe, there’s so many different providers for EV. You have to have so many different apps. In Europe, sometimes you need actual physical cards to use charging stations. I think the issue is more about process and standardization rather than the type of technology itself. I think we have the technical capabilities today to do it. I think it’s the community coming together to make sure we can provide those solutions. We see companies like Beta that have their own charging network in place. Companies like Archer putting forward their version of what charging solutions may be. We can’t have all these different types of infrastructure at every single location, and I think we want to see interoperability of aircraft at a vertiport. Can we come to a consensus on how we do that? And that’s still very much to be matured as we go through the initial operation and learn the in-service reality.
What is needed before eVTOLs are profitable?
Matt: The market is new, the product designs are new, and you need economies of scale to happen and right now they’re making one-offs. Any time you make just one of something, it’s very expensive to do that. You’re seeing a lot of evolution in how they’re thinking about building and making and getting their manufacturing and supply chain stable. I think that’s important for profitability but the other thing that I think is a really interesting piece of this ecosystem of profitability is electricity in California is very different in cost than it is in other places. How that plays into this business is going to be really significant. I think there’s going to have to be a little help here in operation and profit. But manufacturing again needs a state of maturity and stability because there are new things being built and understood until they get production lines scaled up. We’ll have to wait to see some profit there.
Even from personal comfort and you as a passenger making that choice – I want to fly or travel this way. It’s a new thing and no one is doing it today. What will it take for you, how bad does traffic have to be, or will you feel safe getting into one of these vehicles that are brand new? Those are a couple elements that it will be interesting to see how they play out.
Martin: I can add to that. Cost comes in more-so for consideration when you have people involved. Within the aerospace industry, that comes down to how often do you have to maintain an aircraft. The maintenance per flight hour is a big, key parameter. That’s where eVTOL does in particular have its main advantage over helicopter and light aircraft use. They are Simple systems compared to traditional aircraft.
The second one is design for manufacture, design for assembly. How can systems, how can components be designed to speed up manufacturing time, repair time. That’s the second phase of eVTOL maturation. We’ll start seeing some optimized airframes, optimized components that really move us more to an automotive style production line that we currently don’t see in aerospace, where you’re building 70/80 passenger aircraft a month. But that dwarfs in comparison with the automotive industry with what they’re doing with thousands a month. We’re going to be somewhere in between. But I think there’s some work for us as engineers to look at how we can reduce the operation of the labor cost involved with eVTOL manufacture.
What regulations could prevent or accelerate adoption globally?
Martin: We’re seeing quite a divergence right now with what EASA is stipulating and what the FAA is stipulating. The FAA’s approach to regulation is picking and choosing from existing certification groups and procedures. EASA on the other hand is evolving a completely new certification process for eVTOL. They’re not harmonized. There’s some work that hopefully they can become more harmonized in a couple years’ time. 2026 is a target, I’ve seen. But at the moment they do require quite a different approach to the level of safety of the system.
At the moment, Europe is stipulating a higher safety requirement 10 to the minus nine (?), and in the FAA it depends, it’s 6, it’s 7, it’s 8 depending on the application (?). They’re also stipulating 45 minutes charge for landing divert time. but that is longer than most eVTOL aircraft are designed to fly for right now. That doesn’t quite tie up. EASA and FAA are not harmonized. Does that mean aircraft certified in the USA cannot fly in Europe? It looks like that might be the case at the moment. Does that mean European aircraft are inherently more costly to build and therefore to buy than a US counterpart? Does that put European manufactures at a lower level of attractiveness in the market? The two different approaches are definitely looking to be cost complications for global uptakes for one standard of regulatory oversight. Therefore, the design, the operation of these aircraft. At the moment, I think we have a situation where the operation of and the global uptake could be impacted on regulations rather than technology.
What did you learn about at the 2024 Vertical Flight Society show?
Matt: For me, we usually have a cast of characters that are involved in this industry that we’re familiar with. We had a booth at the show and right behind us were two eVTOLs from a company I had not heard of yet. They were for sale. There’s so much happening, and we met a lot of new people there. There’s so much happening in this industry, it’s tough to keep an eye on everything there. But there are new players in here that just emerged. You just never know. There are the top big brands that you’re very familiar with, but there are other players in there that are introducing products. That was a very interesting thing.
The one thing I want to say in terms of regulation were the Paris Olympics. I think that was a real milestone that a lot of companies had their eye on it for flying. Having operational service. The one thing that happened is the city officials in Paris said “no, you can’t fly them here.” And it wasn’t because of a technical risk. They just didn’t want to see them or hear them in their city. Those are things that I think caught some people by surprise. I think there needs to be a higher degree of comfort level with this as a form of transportation.
Martin: For me, I was kind of surprised at not being surprised in some ways. I thought there may be some kind of eureka, some kind of grand announcement about the progress of testing, the progress of certification. I can tell they’re still working. I can tell there’s people not wanting to give too much away at the moment. There was a lot of discussion: aerodynamics, the vibration fields of these aircraft. I think that was great to see [that discussion]. For me, the vibration environment seems a bit of an unknown. It’s great that’s being talked about. I was a little surprised we were uncertain about things at the time of certification. When I say we, I mean the industry. I think there is an opportunity we’re we expected to see some kind of eureka moment of meeting at the certification requirements. And I feel 2024 it's still yet to happen. Maybe in 2025 at an event we’ll see that announcement.
Where is TE in the eVTOL system architecture?
Matt: TE’s focus is on connectivity, especially electric connectivity and power switching. We have a team now that I lead. It’s called Advanced Systems and Architecture. This is literally what we do. We sit with customers, help physically map out what they’re trying to connect, and how that works. Every piece of this is vital. You can’t have any weak leak in that system. Our customers sometime come to us with things they’ve chosen that I can challenge them. “Why did you pick that? It’s not consistent with some of these higher reliability products.” They may have borrowed it from automotive-grade type product which has a very different expectation. If you have a problem with your car, pull over to the side of the road. If you have a problem when you’re flying, that’s something that’s a much more serious situation.
Martin mentioned before about the need for redundancy, what does that look like? In critical aircraft systems, sometimes it’s double redundant or triple redundant. That’s all weight. And at some point, you become too heavy, and you can’t fly, and you don’t have range. Where we look in the architecture are everything that ends on the wires with a lug on it. Is that weight optimized for you, and the size of the cable? Is that the proper gage conductor inside of it? The types of insulation we put on top of it. Is that as thick as it needs to be for the voltage you’re running? Or can it be reduced because you’re at a lower altitude and you have different phenomena occurring at high altitude then you do at low altitude. We walk through the whole architecture with our customers to make sure they have the right products for reliability, but also the right products for weight optimization.
How is TE supporting eVTOL manufacturers with their tech road maps?
Matt: The one thing that we do, I think because we have other markets at TE outside of aerospace, we can communicate some of this technology that can be adopted into eVTOL. The EVs driving today have already thought through things like charging and cooling systems while they are charging. We can help bring innovation in those spaces where we already have some industries that are ahead of aerospace. That is one advantage where TE can help bring other engineers from our company and have these conversations. Our roadmaps, we typically look at five to 10 years from now. NASA has some roadmaps not just with eVTOL, but how do we get electric propulsion in larger aircraft, like regional and other wide-bodied. There is a roadmap with some timing on that.
Part of what we look at is not just the electrical element of it, but other areas of sustainability. There’s a current wave of thinking around hydrogen, also sustainable aviation fuels, and a lot of different elements in the technology development. Again, we talked about infrastructure. If you’re now going to switch fuels or go with hybrid type of aircraft, you still have to figure out with that looks like for operation, maintenance, and long-term reliability.
How is TE helping companies address challenges such as weight?
Matt: Outside of safety, weight is the biggest topic that we talk to our customers about. What that enables us to do is go through the types of materials they’re considering. Just a basic example is a lot of traditional power systems are run with copper wire. We have aluminum wire that’s certified to run in aerospace, and it’s about half the weight of it. You have to size the gauges of your materials to be appropriate to handle the current. Those are some of the things we’re doing with new materials. Materials and there’s an area of what we call generative design. We can use computer models to do analysis of the actual parts and make sure we don’t have too much material in there. It helps us reduce weight typically 30 to 50% if we run through that type of analysis.
What is TE doing to be more agile in addressing customer requirements?
Matt: Agile just means you don’t need to get it perfect to give your customers a sample. Be early in your concepts and prototypes, and we have ways to do that today with things like 3D printing, where we can show our concepts usually within 24 hours where we talk about an idea. We can model it and show them a sample of it – a real sample that they can play with and get their hands on. When we think about agility, it’s about doing our due diligence on the design end of it and then be very quick with manufacturing methods and prototypes before we have to scale up for mass production.
How is TE using its capabilities to drive innovation?
Martin: This is what is exciting about eVTOL. It’s a super catalyst for innovation and technology development, particularly in aerospace. If you look at our products in the aerospace business unit, we have relays, cables, connectors, fiber optics, about a dozen product types that work in eVTOL straight of the shelf. If you look at our design capabilities behind that, if you look at our manufacturing capabilities behind that, relays are about high-power switching, connectors are about high tolerance mating wire and cables is about materials and electrical phenomena and how you design the material constitution for that. If you strip down to the fundamentals behind those products, you have an amazing array of capabilities that TE has great potential to excel in future components. Combining these capabilities for real value innovation for products, for capabilities for our customers eventually. That’s what we’re here for. We’re here to develop new products, new technologies for our customers to create some exciting platforms. For us, within aerospace, we, TE, have that fundamental potential.
But then the great thing about TE is we’re very broad in the markets we serve in, as Matt mentioned. From devices in a cellphone to components in a car or in satellites or in rockets. We thoroughly have a broad expertise that we can rely on, and that we can bring into this new domain that perhaps we never thought about before. That’s what I’m really excited about. Going back to the fundamentals underlying the products we sell, what can we do and create in this amazing new chapter for TE.
What does an eVTOL future look like?
Martin: Hopefully for me it means I can get to the airport in 20 minutes, not two hours. I travel a lot. I’m used to using buses and trains and coaches, so I’d like to slip out to the airport and get to my home in Bristol pretty quick. That would be a very good thing for me personally. Being physically connected to different parts of the world has great potential for society as a whole. To go places, get better services, seeing different parts of the world. That to me would be a great future to look forward to.
Matt: I agree, Martin. The amount of time we waste in traffic… last year we were at the Paris air show and the Paris air show was just a few miles from our hotel. And because of traffic, it took four hours to get there. When I think about eVTOL future, I think about having that ability to have flexibility in traveling. If I can call an eVTOL to pick me up and fly over everything like that. You think about some of the futuristic movies like Blade Runner and things like that, you’re floating around in a three-dimensional travel option. I think about that as that can be our future, and it’s exciting that TE can be part of some of these inflections in the world like that.
Which eVTOL trends is your team watching?
Matt: For me I’d say I’m excited about evolution in the battery technology. Until we get the energy density to the point where we don’t have to worry about weight, and if we can come up with a magical battery that’s lighter. There are things like that are really critical to innovate and to get us to the point where that’s no longer a concern. That’s one of the areas where I’m enthusiastic to see if there’s new chemistries and if we can leverage things like AI to calculate the proper chemistry for better battery technology and safe technology, that’s what I’m looking forward to.
Martin: For me, in terms of actual eVTOL technologies, there’s the optimization, becoming effective and efficient with components and subsystems. With the move away from hydraulics, fuel within traditional aerospace, some of the technologies in the future are about combining the products functionalities, combining with systems thinking. Thinking about how you’d integrate with a carbon composite airframe with wire and cable. I think there’s a real openness actually to try things differently. I think it’s brought about an exploration phase in aerospace that almost anything can be possible with the technologies and capabilities we have today with digital engineering for example, and agile design process. For me, it’s a blank sheet, almost, when you look at what can be done in this new domain.
What do you expect will drive technology integrations and engineering partnerships?
Matt: One of the things we absolutely saw was alliances in the charging networks. And that’s what everyone needs. Everyone needs a charger. If you can get consensus on what’s the best way that’s not overdesigned, overkill, and optimized. That’s certainly one. I think there are questions about autonomy. Do these things need a pilot or not? Perhaps there would be convergence in how they operate and some of those technical pieces like standard batteries. Maybe charging isn’t the answer, maybe it’s swapping the battery out is the answer. There’s a lot of things like that we’ll see in the next few years. I thought it was interesting that the designs are converging. There used to be a lot of different types, but they seem to be converging into the articulating section of the motors and also the ones that don’t. They’re just used for lift and they often park them, and then they’ll turn the articulating ones for flight. We are seeing a lot of things like that partnering in recent times.
Martin: It’s interesting because there’s two factions. There are companies that want to do everything eVTOL themselves, from designing to operating the aircraft. And then you’ve got others that are more traditional with using a supply chain to get to the experts for say motor subsystems. I think we’ll see, as the mass ecosystem matures, a refinement of those partnerships. I think we’ll see a greater in depth desire to be partnered for providing services and supply chains into these companies and the end user. I think we’ll explore more of that. I think there’s still more to be explored rather than be exploited for anyone’s true benefit. There’s still the experimentation phase to come out. We’ll find out what partnerships work, what the emphasis is. It’s going to be an interesting time of potentially some acquisitions as well in the eVTOL industry. I wouldn’t be surprised to see some of those partnerships begin to converge.
Matt: One more thing I would say when we think about engineering partnerships with eVTOL is we do see a tight alliance with some of the automotive EVs. And because they have that experience, some are now aligning themselves with some of the eVTOL makers, which makes sense. You see companies like Hyundai and Porsche and some of these other types of brands that do have their partner with flying vehicles as well.
Martin: Matt brings up a good point with startups. We’re also seeing a lot of automotive partnerships and automotive is driving a lot of this early technology growth. You ask yourself, where are the aerospace primes? Where are Boeing and Airbus and Leonardo? They’re coming later and waiting to see what the market is doing. They are there – the traditional aerospace Is there – but perhaps with a wiser head, they’re waiting to see how this market plays out and what their role is.
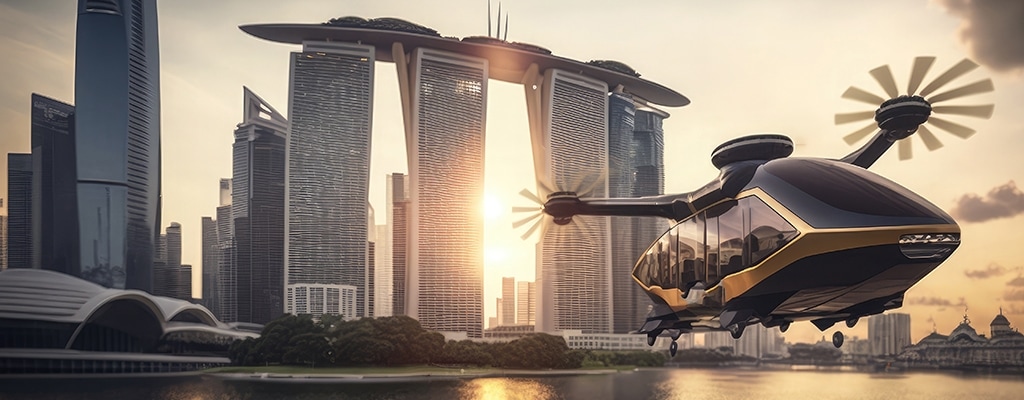
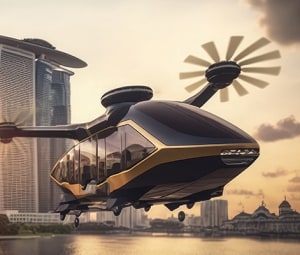
We’re still in the exploration phase... still seeing innovation in how these aircraft are going to be configured and put together. ...There’s still innovation at the system level and we will, I think, see in the very near-term innovation coming down to the component level as well.
March 4, 2024
Innovation in eVTOL technology is addressing the practical operational and maintenance needs crucial for operability and serviceability. This is happening most crucially in charging infrastructures, battery technologies, and remote services. The focus is scaling the technology for global adoption. In this interview with Martin Cullen (TE Senior Manager, Business Development, Aerospace) and Matt McAlonis (TE Engineering Fellow, Aerospace), they share insights on the challenges system architectures, the maintenance requirements for operating eVTOLs, and the need for regulatory and infrastructure standardization to support global adoption.
Where is innovation happening in eVTOL architectures?
Martin: These eVTOL designs have been in work for a good number of years to certain degrees of maturity with each different manufacturer. We’re still in the exploration phase to understand what these architectures are going to be looking like. We are still seeing innovation in how these aircraft are going to be configured and put together. Evidently, still the prime source of innovation is in the battery technology. Whether it’s cell chemistry, or battery packing, how you connect that to the rest of the electrical power system. There’s still innovation at the system level and we will, I think, see in the very near-term innovation coming down to the component level as well. At the moment, it is still at the system level, very much focused on the battery. And what’s past that stage, as a certified aircraft, we’ll see the second stage of looking at the component and how that can be innovated for future benefits.
What does maturity in eVTOL architectures look like?
Martin: It’s converging. Like I said, there’s so many different configurations out there and there’s different applications where you see an optimized air frame, optimized configuration that will fit better in some of these cases more than others. And over time we’ll eventually see a convergence of what the best configuration is for that particular use case. We have things to think about, like. Redundancy. What is the redundancy of systems in each of these configurations? How you have dual or triple systems between individual power packs and most of the inverters. How you control that through the PDUs, the power distribution units. There’s still going to be some optimization, some innovation on that level of architecture, including the charging system. We’re seeing different systems where there’s one, two, or four chargers on the aircraft. How that is managed, how different failure systems are managed is still yet to be worked out. We’ll see some convergence of optimized design as the aircraft is used the first two or three years of operation.
What must be addressed before eVTOLs are a viable technology for mass transit?
Martin: What we have to consider here, first of all, is what is mass transit. The eVTOL is not there for mass transit. That’s going to be your buses, coaches, and trains. That’s what mass transit is. What we will see are different mobility routes that come out with eVTOLs. Going across deserts, or lakes, or mountain regions. And as we start seeing those use cases, you have to think about how are these aircraft going to be maintained, serviced out there at the Point B destination. You’ve got to think about infrastructure, you have to think about repair, services and the people who are going to be doing it. You have to think about how they’re going to get components and other repair equipment to these locations.
Physically it’s a bit of a catch 22 of understanding how these aircraft are going to be operated, what kind of infrastructures and people you need at these locations. And then how you’re going to expand that to different areas, different routes. It’s going to be a bit of a catch 22 involving capability needs, as these operations are explored essentially. Again, with all of this domain, from components and subsystems to the airframes to the actual in-service operation and how passengers are going to get onto the aircraft. I think it’s still going to be a bit of ‘find out and see’ when the rubber hits the road [better analogy; as things take-off].
How can this be addressed without compromising the design?
Matt: There is a lot of technology that is new and pure electric propulsion is something that needs, in space and aerospace terms, a technology readiness level to be considered reliable and repeatable. Some of the things we’re looking at in some of these new aircraft are things like flexing and articulating motors, which most aircraft have a static motor on there. We make a lot of things like wire and cable systems that aren’t initially designed to have that type of flexure in them. There’s innovation happening with the types of aircraft, the design of aircraft. We need data to understand what maintenance looks like. Right now, when an aircraft lands it goes through some routine inspections but inspecting things like the cables typically isn’t part of the process today.
As we think about draining a system, so to speak, and even the ranges of these batteries, the electrical integrity of electricity on the top of the charge and the bottom of the charge is different. How far down can you take your batteries and still be capable of an emergency loop or a redivert? As we think about the electrical systems and getting data on these systems is very important to get to that technical maturity level.
What do you think is limiting OEM capacity and adoption at scale?
Matt: When you think about these early nascent designs that are just starting to fly, one or two aircraft are flying in service, we live in a highly regulated industry. And it has to be because if you have a failure, it could be fatal. It’s not just the crash of the aircraft. It’s also when high power electricity is used and fails it is very explosive and dramatic. When you think about the lightning bolts that – if you have a failure that could occur – you need to keep things safe. There’s a lot of new technology; power levels that typically haven’t been seen before. They’re typically in the range of three times in terms of what our current aircraft are seeing in terms of the voltages. With these high-voltage systems, we have to make sure we have the right testing to make sure the systems are safe and reliable, and again understand that maintenance. When you push innovation, you really need to understand not just how it works but also how it fails. What are the degradation mechanisms that need to be looked at.
When you think about scaling – so scaling and building these aircraft are different. The manufacturing processes and methods are new. How we wire them and install electrical motors versus traditional aircraft engines is different. Those are things that we have to have new processes, like how do I have to take my batteries in and out, that’s not part of the standard maintenance. Or how do I inspect some of these systems. This all has to be studied, it has to be approved by the FAA, and we need the ground maintenance infrastructure to be available as well. You have new types of mechanics and technicians that have to be trained. There are so many things that need to be certified. When you think about aerospace in general, there are several types of certification. One is your design, one is how you make it, one is how you test it, and one is how you use it in operations. All four of those areas have to be considered and have confidence in them.
How might these advancements affect connector design going forward?
Matt: Electrical connectivity is essential here. What we do with customers is we put a schematic together from the charger to the energy storage area to the power switching area, the whole way to the inverters and motors and all that connectivity in between and how they manage their harness. When you think about all that content, that’s weight. The first thing we look at is to make sure it’s weight optimized. There are different things like the geometries we play with and how that can conduct electricity more efficiently and amperage more efficiently. We have to look at the electrical fields around these components. We want to make sure that they’re light as possible, but they have to be as robust as possible. If something like a charger is being mated to every time, that doesn’t necessarily have to be, that’s not being charged in flight. That’s not as a concern for vibration for us, but the things that are connected to the battery that have to be reliable in flight, that’s where we typically will focus and optimize those things.
When we deal with flight, we also have things like takeoff, landing, cruise where we’re looking at all the different vibration profiles and the current carrying profiles during different situations in flight. We do thorough analysis on these things, but again we try to use our engineering analysis tools and simulation tools to make sure we have optimized product. Weight is the thing that is very different with conventional aircraft, where you’re burning fuel. Your batteries don’t get any lighter when they discharge so you’re literally carrying around dead weight. That’s an area we really have to focus on is our materials we use for weight reduction.
What is needed to stably maintain eVTOLs over time?
Martin: Again, I think that’s a place where we don’t have all the answers. There’s a lot of experienced helicopter operators have been operating for decades in remote locations. They have a good understanding but when it comes down to high voltage applications that fly in harsh environments, there’s going to be unique instances that they’ve never experienced before. A lot of these aircraft have tilt rotors. You have bearings now moving, you have cable that is flexing. These aircraft are flying in sand and dust environments. Sand gets everywhere. Dust gets everywhere. So how does it get into the aircraft and how is it going to impact its operation? There’s a lot required for repair and maintenance for any aircraft. It comes down to what processes do you have, what people do you have? Do you have a supply chain in replace for repairs? It takes up to four years for an aircraft mechanic to be certified. What training is there for an electric aircraft mechanic? Is there a certified eVTOL mechanic out there? I don’t think so. Because we’re still going through that process. I think we need to bring across the experience from the helicopter operators. We have to look for potential weak points of the aircraft that we think we can apply our knowledge and our help to design these aircraft. And also, how can we support the considerations about the design for repair. Access, for example. How you disconnect quickly and easily and how you get to the right level of maintainability for these aircrafts. We’re going to have to learn as we go in these instances.
What operational and maintenance needs to be defined?
Martin: What comes to mind to me is inspection. You’ve probably seen pilots go around the aircraft before takeoff to do a safety check on the aircraft. If you’ve got a PPL – private policy license – you fly yourself. The first time you fly in the aircraft you have to do a thorough check. The second time you fly the same day, you can do a lower-level check. What level of inspection is going to be required before you take off with your passengers? How are you going to monitor the ingress and egress of passengers that could damage the propellers or another part of the airframe? The required regular inspection and the number of safety checks before you fly each time? There’s going to be quirks, there’s going to be distinct requirements on these aircraft that you won’t see elsewhere, from inspections of let’s say propeller tips all the way down to looking at the electrical system itself. I think that’s the first thing that we need to get understood in this industry.
What operational and adoption concerns are top of mind for OEMs?
Matt: I think it’s similar to the automotive EVs of today, which is charging. When you need to charge where you land – these are very portable aircraft that could land anywhere there’s a flat space – the question is how much charge is left to get you to a charger. And then when you land, what kind of charger is there? There’s a really interesting thing we learned last week at the Vertical Flight Society event – The Transformation of Vertical Flight – and it was about chargers. Two companies emerged and said, “Pick mine.” They had different interconnects; they had different systems. And you want to charge as fast as possible. But when you charge fast, that means it gets very hot. And if the connectors are hot, and if the batteries are getting hot, where are the batteries located? In some of the designs we’ve seen, batteries are literally surrounding the passengers. We’ve seen batteries that are up in the wings. So can you imagine how that will look like if you’re in a fuselage waiting to take off and it’s getting very warm and uncomfortable.
There are things like that which are still going to be thought through. There’s a lot of work needed to supply this power. You have the physical infrastructure on the ground, if you’re landing on a roof, is that building wired for this megawatt type of charging system that’s needed? It’s probably not today. There’s a lot of things like that which need to be worked through. The other question I would think about is can you even charge in the rain, and what does that look like? There are so many new things that will have to be vetted out before the operational is certified.
What can manufacturers do to make eVTOLs feasible long-term?
Martin: In terms of service and repair and operations, as Matt touched on, it’s standardization, particularly of charging and the infrastructure required. That can be from the particular mating profile of the charger of the connector, to the data download, the CAN bus protocol for instance that might be used. We’re kind of familiar with OBD2 in automotive. Do we have something similar in aerospace that is standardized? Do we have a common way of using the same charging system protocol but with different charging inlets amongst eVTOL aircraft types themselves? Are there any security type concerns of connecting these aircraft to chargers, maybe some that are remote or even part of a busy area?
There’s the security aspect, there’s the data integration, the standardization of charging, standardization of operations. If we look at current commercial protocols, you cannot refuel while passengers are onboard, for example. Does that mean you cannot charge your electric aircraft with passengers are onboard, or how far do they have to be away from it? There’s some regulations and standards that have to be put in place and well-communicated to put in the design of these aircraft, and also help the operation processes be quick and allow these aircraft to operate as intended.
What does the charging infrastructure look like for eVTOLs?
Martin: Matt kind of touched on this with the different types of proprietary IP charging elements. I’ve seen many companies come to market with their idea of charging units, remote charging units at large airport locations through to remote helipads or parking lots or the top of skyscrapers. It hasn’t been implemented yet. There’ve been trials done and experimentation done with these. I think it depends on each case. If you’re shuttling back and forth from an airport, then you can use the airport facilities. That’s fairly straightforward. They have a good infrastructure of high-power connectivity there. When you start looking at remote vertiport and if they’re charging somewhere, how do you put infrastructure in there? It can’t be heavy; it has to be lightweight. You need to have it without much maintenance. Just as these platforms may be individualized for use case, I think you’ll see a charging infrastructure be optimized for particular use case as well.
What are challenges to making this infrastructure available at scale?
Martin: Again, I think we touched a little bit about standardization. How can we be certain that we don’t end up in a BetaMax-type situation where everyone’s investing huge amounts of infrastructure into one type of connector, one type of charging system? How can we be brave enough to provide the numbers that are going to be required? Because as we all see today, traveling from the west coast to the east coast in the USA, or traveling through Europe, there’s so many different providers for EV. You have to have so many different apps. In Europe, sometimes you need actual physical cards to use charging stations. I think the issue is more about process and standardization rather than the type of technology itself. I think we have the technical capabilities today to do it. I think it’s the community coming together to make sure we can provide those solutions. We see companies like Beta that have their own charging network in place. Companies like Archer putting forward their version of what charging solutions may be. We can’t have all these different types of infrastructure at every single location, and I think we want to see interoperability of aircraft at a vertiport. Can we come to a consensus on how we do that? And that’s still very much to be matured as we go through the initial operation and learn the in-service reality.
What is needed before eVTOLs are profitable?
Matt: The market is new, the product designs are new, and you need economies of scale to happen and right now they’re making one-offs. Any time you make just one of something, it’s very expensive to do that. You’re seeing a lot of evolution in how they’re thinking about building and making and getting their manufacturing and supply chain stable. I think that’s important for profitability but the other thing that I think is a really interesting piece of this ecosystem of profitability is electricity in California is very different in cost than it is in other places. How that plays into this business is going to be really significant. I think there’s going to have to be a little help here in operation and profit. But manufacturing again needs a state of maturity and stability because there are new things being built and understood until they get production lines scaled up. We’ll have to wait to see some profit there.
Even from personal comfort and you as a passenger making that choice – I want to fly or travel this way. It’s a new thing and no one is doing it today. What will it take for you, how bad does traffic have to be, or will you feel safe getting into one of these vehicles that are brand new? Those are a couple elements that it will be interesting to see how they play out.
Martin: I can add to that. Cost comes in more-so for consideration when you have people involved. Within the aerospace industry, that comes down to how often do you have to maintain an aircraft. The maintenance per flight hour is a big, key parameter. That’s where eVTOL does in particular have its main advantage over helicopter and light aircraft use. They are Simple systems compared to traditional aircraft.
The second one is design for manufacture, design for assembly. How can systems, how can components be designed to speed up manufacturing time, repair time. That’s the second phase of eVTOL maturation. We’ll start seeing some optimized airframes, optimized components that really move us more to an automotive style production line that we currently don’t see in aerospace, where you’re building 70/80 passenger aircraft a month. But that dwarfs in comparison with the automotive industry with what they’re doing with thousands a month. We’re going to be somewhere in between. But I think there’s some work for us as engineers to look at how we can reduce the operation of the labor cost involved with eVTOL manufacture.
What regulations could prevent or accelerate adoption globally?
Martin: We’re seeing quite a divergence right now with what EASA is stipulating and what the FAA is stipulating. The FAA’s approach to regulation is picking and choosing from existing certification groups and procedures. EASA on the other hand is evolving a completely new certification process for eVTOL. They’re not harmonized. There’s some work that hopefully they can become more harmonized in a couple years’ time. 2026 is a target, I’ve seen. But at the moment they do require quite a different approach to the level of safety of the system.
At the moment, Europe is stipulating a higher safety requirement 10 to the minus nine (?), and in the FAA it depends, it’s 6, it’s 7, it’s 8 depending on the application (?). They’re also stipulating 45 minutes charge for landing divert time. but that is longer than most eVTOL aircraft are designed to fly for right now. That doesn’t quite tie up. EASA and FAA are not harmonized. Does that mean aircraft certified in the USA cannot fly in Europe? It looks like that might be the case at the moment. Does that mean European aircraft are inherently more costly to build and therefore to buy than a US counterpart? Does that put European manufactures at a lower level of attractiveness in the market? The two different approaches are definitely looking to be cost complications for global uptakes for one standard of regulatory oversight. Therefore, the design, the operation of these aircraft. At the moment, I think we have a situation where the operation of and the global uptake could be impacted on regulations rather than technology.
What did you learn about at the 2024 Vertical Flight Society show?
Matt: For me, we usually have a cast of characters that are involved in this industry that we’re familiar with. We had a booth at the show and right behind us were two eVTOLs from a company I had not heard of yet. They were for sale. There’s so much happening, and we met a lot of new people there. There’s so much happening in this industry, it’s tough to keep an eye on everything there. But there are new players in here that just emerged. You just never know. There are the top big brands that you’re very familiar with, but there are other players in there that are introducing products. That was a very interesting thing.
The one thing I want to say in terms of regulation were the Paris Olympics. I think that was a real milestone that a lot of companies had their eye on it for flying. Having operational service. The one thing that happened is the city officials in Paris said “no, you can’t fly them here.” And it wasn’t because of a technical risk. They just didn’t want to see them or hear them in their city. Those are things that I think caught some people by surprise. I think there needs to be a higher degree of comfort level with this as a form of transportation.
Martin: For me, I was kind of surprised at not being surprised in some ways. I thought there may be some kind of eureka, some kind of grand announcement about the progress of testing, the progress of certification. I can tell they’re still working. I can tell there’s people not wanting to give too much away at the moment. There was a lot of discussion: aerodynamics, the vibration fields of these aircraft. I think that was great to see [that discussion]. For me, the vibration environment seems a bit of an unknown. It’s great that’s being talked about. I was a little surprised we were uncertain about things at the time of certification. When I say we, I mean the industry. I think there is an opportunity we’re we expected to see some kind of eureka moment of meeting at the certification requirements. And I feel 2024 it's still yet to happen. Maybe in 2025 at an event we’ll see that announcement.
Where is TE in the eVTOL system architecture?
Matt: TE’s focus is on connectivity, especially electric connectivity and power switching. We have a team now that I lead. It’s called Advanced Systems and Architecture. This is literally what we do. We sit with customers, help physically map out what they’re trying to connect, and how that works. Every piece of this is vital. You can’t have any weak leak in that system. Our customers sometime come to us with things they’ve chosen that I can challenge them. “Why did you pick that? It’s not consistent with some of these higher reliability products.” They may have borrowed it from automotive-grade type product which has a very different expectation. If you have a problem with your car, pull over to the side of the road. If you have a problem when you’re flying, that’s something that’s a much more serious situation.
Martin mentioned before about the need for redundancy, what does that look like? In critical aircraft systems, sometimes it’s double redundant or triple redundant. That’s all weight. And at some point, you become too heavy, and you can’t fly, and you don’t have range. Where we look in the architecture are everything that ends on the wires with a lug on it. Is that weight optimized for you, and the size of the cable? Is that the proper gage conductor inside of it? The types of insulation we put on top of it. Is that as thick as it needs to be for the voltage you’re running? Or can it be reduced because you’re at a lower altitude and you have different phenomena occurring at high altitude then you do at low altitude. We walk through the whole architecture with our customers to make sure they have the right products for reliability, but also the right products for weight optimization.
How is TE supporting eVTOL manufacturers with their tech road maps?
Matt: The one thing that we do, I think because we have other markets at TE outside of aerospace, we can communicate some of this technology that can be adopted into eVTOL. The EVs driving today have already thought through things like charging and cooling systems while they are charging. We can help bring innovation in those spaces where we already have some industries that are ahead of aerospace. That is one advantage where TE can help bring other engineers from our company and have these conversations. Our roadmaps, we typically look at five to 10 years from now. NASA has some roadmaps not just with eVTOL, but how do we get electric propulsion in larger aircraft, like regional and other wide-bodied. There is a roadmap with some timing on that.
Part of what we look at is not just the electrical element of it, but other areas of sustainability. There’s a current wave of thinking around hydrogen, also sustainable aviation fuels, and a lot of different elements in the technology development. Again, we talked about infrastructure. If you’re now going to switch fuels or go with hybrid type of aircraft, you still have to figure out with that looks like for operation, maintenance, and long-term reliability.
How is TE helping companies address challenges such as weight?
Matt: Outside of safety, weight is the biggest topic that we talk to our customers about. What that enables us to do is go through the types of materials they’re considering. Just a basic example is a lot of traditional power systems are run with copper wire. We have aluminum wire that’s certified to run in aerospace, and it’s about half the weight of it. You have to size the gauges of your materials to be appropriate to handle the current. Those are some of the things we’re doing with new materials. Materials and there’s an area of what we call generative design. We can use computer models to do analysis of the actual parts and make sure we don’t have too much material in there. It helps us reduce weight typically 30 to 50% if we run through that type of analysis.
What is TE doing to be more agile in addressing customer requirements?
Matt: Agile just means you don’t need to get it perfect to give your customers a sample. Be early in your concepts and prototypes, and we have ways to do that today with things like 3D printing, where we can show our concepts usually within 24 hours where we talk about an idea. We can model it and show them a sample of it – a real sample that they can play with and get their hands on. When we think about agility, it’s about doing our due diligence on the design end of it and then be very quick with manufacturing methods and prototypes before we have to scale up for mass production.
How is TE using its capabilities to drive innovation?
Martin: This is what is exciting about eVTOL. It’s a super catalyst for innovation and technology development, particularly in aerospace. If you look at our products in the aerospace business unit, we have relays, cables, connectors, fiber optics, about a dozen product types that work in eVTOL straight of the shelf. If you look at our design capabilities behind that, if you look at our manufacturing capabilities behind that, relays are about high-power switching, connectors are about high tolerance mating wire and cables is about materials and electrical phenomena and how you design the material constitution for that. If you strip down to the fundamentals behind those products, you have an amazing array of capabilities that TE has great potential to excel in future components. Combining these capabilities for real value innovation for products, for capabilities for our customers eventually. That’s what we’re here for. We’re here to develop new products, new technologies for our customers to create some exciting platforms. For us, within aerospace, we, TE, have that fundamental potential.
But then the great thing about TE is we’re very broad in the markets we serve in, as Matt mentioned. From devices in a cellphone to components in a car or in satellites or in rockets. We thoroughly have a broad expertise that we can rely on, and that we can bring into this new domain that perhaps we never thought about before. That’s what I’m really excited about. Going back to the fundamentals underlying the products we sell, what can we do and create in this amazing new chapter for TE.
What does an eVTOL future look like?
Martin: Hopefully for me it means I can get to the airport in 20 minutes, not two hours. I travel a lot. I’m used to using buses and trains and coaches, so I’d like to slip out to the airport and get to my home in Bristol pretty quick. That would be a very good thing for me personally. Being physically connected to different parts of the world has great potential for society as a whole. To go places, get better services, seeing different parts of the world. That to me would be a great future to look forward to.
Matt: I agree, Martin. The amount of time we waste in traffic… last year we were at the Paris air show and the Paris air show was just a few miles from our hotel. And because of traffic, it took four hours to get there. When I think about eVTOL future, I think about having that ability to have flexibility in traveling. If I can call an eVTOL to pick me up and fly over everything like that. You think about some of the futuristic movies like Blade Runner and things like that, you’re floating around in a three-dimensional travel option. I think about that as that can be our future, and it’s exciting that TE can be part of some of these inflections in the world like that.
Which eVTOL trends is your team watching?
Matt: For me I’d say I’m excited about evolution in the battery technology. Until we get the energy density to the point where we don’t have to worry about weight, and if we can come up with a magical battery that’s lighter. There are things like that are really critical to innovate and to get us to the point where that’s no longer a concern. That’s one of the areas where I’m enthusiastic to see if there’s new chemistries and if we can leverage things like AI to calculate the proper chemistry for better battery technology and safe technology, that’s what I’m looking forward to.
Martin: For me, in terms of actual eVTOL technologies, there’s the optimization, becoming effective and efficient with components and subsystems. With the move away from hydraulics, fuel within traditional aerospace, some of the technologies in the future are about combining the products functionalities, combining with systems thinking. Thinking about how you’d integrate with a carbon composite airframe with wire and cable. I think there’s a real openness actually to try things differently. I think it’s brought about an exploration phase in aerospace that almost anything can be possible with the technologies and capabilities we have today with digital engineering for example, and agile design process. For me, it’s a blank sheet, almost, when you look at what can be done in this new domain.
What do you expect will drive technology integrations and engineering partnerships?
Matt: One of the things we absolutely saw was alliances in the charging networks. And that’s what everyone needs. Everyone needs a charger. If you can get consensus on what’s the best way that’s not overdesigned, overkill, and optimized. That’s certainly one. I think there are questions about autonomy. Do these things need a pilot or not? Perhaps there would be convergence in how they operate and some of those technical pieces like standard batteries. Maybe charging isn’t the answer, maybe it’s swapping the battery out is the answer. There’s a lot of things like that we’ll see in the next few years. I thought it was interesting that the designs are converging. There used to be a lot of different types, but they seem to be converging into the articulating section of the motors and also the ones that don’t. They’re just used for lift and they often park them, and then they’ll turn the articulating ones for flight. We are seeing a lot of things like that partnering in recent times.
Martin: It’s interesting because there’s two factions. There are companies that want to do everything eVTOL themselves, from designing to operating the aircraft. And then you’ve got others that are more traditional with using a supply chain to get to the experts for say motor subsystems. I think we’ll see, as the mass ecosystem matures, a refinement of those partnerships. I think we’ll see a greater in depth desire to be partnered for providing services and supply chains into these companies and the end user. I think we’ll explore more of that. I think there’s still more to be explored rather than be exploited for anyone’s true benefit. There’s still the experimentation phase to come out. We’ll find out what partnerships work, what the emphasis is. It’s going to be an interesting time of potentially some acquisitions as well in the eVTOL industry. I wouldn’t be surprised to see some of those partnerships begin to converge.
Matt: One more thing I would say when we think about engineering partnerships with eVTOL is we do see a tight alliance with some of the automotive EVs. And because they have that experience, some are now aligning themselves with some of the eVTOL makers, which makes sense. You see companies like Hyundai and Porsche and some of these other types of brands that do have their partner with flying vehicles as well.
Martin: Matt brings up a good point with startups. We’re also seeing a lot of automotive partnerships and automotive is driving a lot of this early technology growth. You ask yourself, where are the aerospace primes? Where are Boeing and Airbus and Leonardo? They’re coming later and waiting to see what the market is doing. They are there – the traditional aerospace Is there – but perhaps with a wiser head, they’re waiting to see how this market plays out and what their role is.