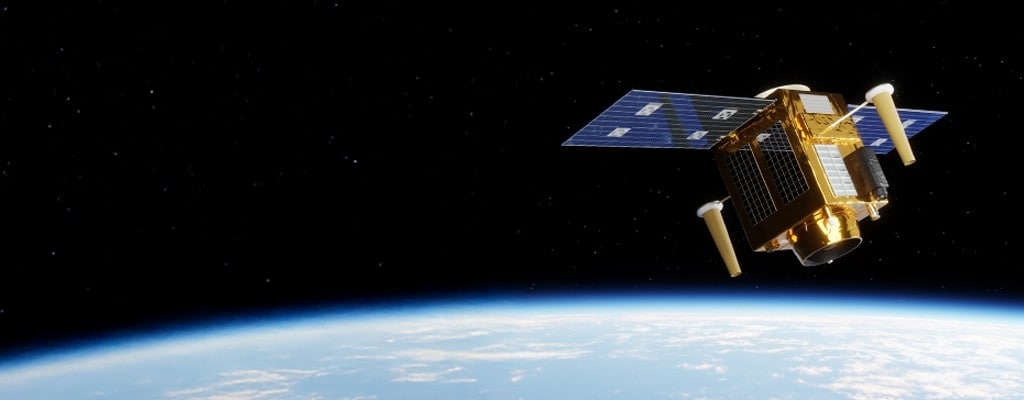
White Paper
Temperature Sensing and Measurement in Satellites and Spacecraft
Essential sensor selection and integration factors
This paper is intended to provide engineers with comprehensive insights into the challenges, selection criteria, and integration of NTC (Negative Temperature Coefficient) thermistors and platinum RTDs (Resistance Temperature Devices) in satellite design. We will explore the specific application challenges of these temperature sensors in space, outline the criteria for selecting the appropriate sensor for various applications, and discuss best practices for their integration and placement. We will illustrate real-world applications of temperature sensors in several well-known programs from around the world. Finally, we will examine future trends such as miniaturization, machine learning, and adaptive sensing, evaluating their potential advantages and tradeoffs in space applications.
TE Connectivity
Temperature Sensors
Internationally Qualified Sensors: For nearly five decades, TE has supplied temperature sensors to NASA and ESA, adhering to stringent GSFC (Goddard Space Flight Center) S-311-P-18 standards required by NASA as well as ESA’s requirements.
Proven performance: Our sensors were included in historic space missions such as Pioneer 10 spacecraft launched in 1972 and the 2011 Juno mission to Jupiter, as well as many other exploratory missions. Our deep experience and commitment to innovation confirm our temperature sensors meet the rigorous demands of space missions, providing reliable performance and contributing to the success of various aerospace projects.
INTRODUCTION
In the past NASA, ESA and various national space agencies were the dominant users of spacecraft components. Suppliers custom-made and produced components for these agencies in relatively small quantities. However, the commercialization of the space industry has dramatically changed the design, development, and implementation of sensors and other components designed for the extreme conditions of space.
In 2023, the industry deployed more than 2,800 satellites, the majority of which are in Low Earth Orbit (LEO). Leveraging extensive experience with national space agencies, we offer cost-effective temperature sensors for the commercial market that rival the accuracy and dependability of sensors designed for legacy spacecraft. The focus remains on future innovations and applications to support this expanding market.
While sensors such as thermal infrared and microwave sensors are deployed in satellites to collect external data, we will focus on temperature sensors intended for applications within spacecraft. These internal sensors are critical to the robust operation of instruments and mechanisms within satellites.
We will explore the challenges associated with applying NTC (negative temperature coefficient) and RTD (resistance temperature detector) temperature sensors in extreme space environments. We will examine factors that influence sensor selection, as well as providing guidance for sensor integration as well as placement.
After reviewing general case studies of specific temperature sensor applications, the paper considers potential future innovations and trends in the temperature sensor industry and discusses advantages and tradeoffs associated with their implementation.
DESIGN CHALLENGES
Design Challenges for Temperature Sensors in Spacecraft
Temperature sensors are critical components in all types of spacecraft. Monitoring internal and external temperatures, they provide data essential to the vessel’s reliability, safety and efficiency. These instruments play key roles such as:
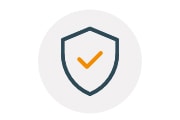
Maintaining Structural Integrity
Temperature sensors track the temperature inside and outside the spacecraft’s hull, confirming that systems to maintain the strength and durability of the hull are within tolerance.
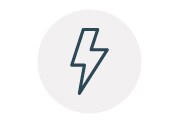
Power System Supervision
Monitoring the temperature of solar arrays and batteries and implementing thermal management systems confirms that the spacecraft has the power necessary to complete its mission.
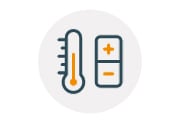
Environmental Management
Temperature sensors help regulate internal environments, helping maintain conditions required for crew and/or equipment.
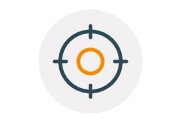
Instrument Calibration
Accurate calibration of all instrumentation relies on accurate reference temperatures provided by these sensors.
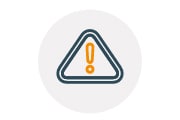
Emergency Overrides
Temperature sensors are used to activate alarms, automatic recovery procedures or emergency shutdown systems.
Spacecraft present unique design challenges for integrating thermistors and RTDs. Temperatures can vary from near absolute zero in the shade to 250°C while the absence of air in the vacuum of space prevents convective heat transfer for temperature management. Radiation can degrade materials causing issues with sensor accuracy. Engineers must account for mechanical stresses from a variety of sources to prevent faulty readings or sensor failure.
Volatile compounds emitted by material outgassing under vacuum conditions can deposit on surfaces interfering with the performance of sensors and other sensitive equipment. Finally, there are formidable power constraints in spacecraft, which highlights the importance of budgeting power demands. Your trusted sensor supplier can offer advice for specific situations; however, the following paragraphs discuss common challenges along with methods for addressing them.
Thermal Variations
Managing thermal variations is both a critical application for temperature sensors and a significant challenge for implementation. Spacecraft experience extreme temperature swings from -270°C to +250°C depending on which side is facing the sun. These extreme temperatures can affect the functionality and performance of many components throughout the vessel, so it is important to implement thermal management to limit exposure of the sensors to extreme thermal cycling. Designers must select sensors designed to withstand the expected temperature ranges at the sensors while considering equipment failures that may lead to excursions.
Absence of Convective Heat Transfer
Unique thermal conditions require thoughtful consideration when applying temperature sensors in spacecraft. Radiant and conductive transmission modes replace convection as the primary mode of heat transfer due to the absence of an atmosphere. This can lead to uneven temperatures that impact the sensor’s accuracy. Therefore, engineers must locate sensors strategically to compensate and choose appropriate sensor materials, mounting hardware and methods. Using active thermal control, such as heaters and coolers, will help to maintain the best operating conditions.
Radiation
The presence of gamma ray, proton and heavy ion radiation can cause degradation of the materials used in instruments and sensors causing inaccurate readings. These errors can compromise the operation and safety of the satellite.
To address this challenge, specify radiation-hardened temperature sensors and include robust materials such as in the sensor design. Utilize redundant sensors along with periodic autocalibration and consider algorithms to compensate for radiation-induced errors.
Mechanical Stresses
Spacecraft experience vibration and shock that can affect temperature sensors, during launch, orbital maneuvers and re-entry. Thermal cycling may also introduce stress in sensors. These stresses may cause the accuracy of temperature sensors to drift if materials are not specified. Where possible, mount discreet sensors in robust enclosure or use a full probe assembly to protect from shocks and vibrations and/or include flexible mounting techniques. Employing calibration and compensation algorithms can also address accuracy. Also, redundant sensors provide a backup to signal issues with readings.
Material Outgassing
Vacuum conditions and high temperatures can cause materials to emit volatile compounds which coat surfaces. Over time, these coatings can significantly affect operation of other onboard equipment. To prevent this issue, materials designed to minimize outgassing should be used throughout the spacecraft. Where material changes are not feasible, employ space-grade coatings to prevent this issue. Performing a thermal vacuum bakeout of components and materials prior to installation also helps to prevent this issue.
Power Constraints
Spacecraft have limited power budgets due to the size and efficiency of their solar panels and the capacity of their battery systems. Sensors that require continuous power for operation can reduce the power available for other systems. To reduce power demands, utilize low power sensors like thermistors or RTDs where possible. Implement smart power management to prioritize allocation. Optimize insulation to reduce active thermal management requirements.
With long standing experience implementing spacecraft sensor technology, TE Connectivity is positioned to leverage their extensive knowledge base to supplement your engineering resources. Below we continue to explore sensor application topics with sensor selection.
SELECTION CRITERIA
Selection Criteria for Temperature Sensors in Spacecraft
Selecting temperature sensors for spaceflight requires careful consideration of the extreme thermal environments spacecraft encounter. During launch, temperatures range from -40°C to +250°C. In Low Earth Orbit (LEO), they can vary between -100°C and +250°C. Deep space temperatures can drop to nearly absolute zero (-270°C), while atmospheric re-entry can expose spacecraft to over 1,650°C. This section explores the criteria for choosing NTC thermistors and platinum RTDs, with examples of their applications. Experienced sensor suppliers can provide valuable insights and access to sensors that have been rigorously tested for specific conditions, however the following provides general information about selection criteria.
NTC THERMISTORS | PLATINUM RTDS | |
---|---|---|
Accuracy and Stability |
|
|
Response Time |
|
|
Power Consumption |
|
|
Size and Weight |
|
|
Cost Effectiveness |
|
|
Temperature Range |
|
|
NTC - Operating Temperature Range is -60°C to +160°C. Storage Temperature Range is -60°C to +160°C.
RTD - Operating Temperature Range is -170°C to +170°C. Storage Temperature Range is -170°C to +170°C.
INTEGRATION & PLACEMENT
Integration and Placement of Temperature Sensors in Spacecraft
Selecting temperature sensors for spaceflight requires careful consideration of the extreme thermal environments spacecraft encounter. During launch, temperatures range from -40°C to +250°C. In Low Earth Orbit (LEO), they can vary between -100°C and +250°C. Deep space temperatures can drop to nearly absolute zero (-270°C), while atmospheric re-entry can expose spacecraft to over 1,650°C.
This section explores the criteria for choosing NTC thermistors and platinum RTDs, with examples of their applications. Experienced sensor suppliers can provide valuable insights and access to sensors that have been rigorously tested for specific conditions, however the following provides general information about selection criteria.
NTC Thermistors
Locate thermistors as close as possible to the critical components being monitored to confirm accurate readings of solar arrays, batteries, electronics, and propulsion system components. Use thermally conductive (minimal outgassing) adhesives or mechanical fasteners that can withstand the expected conditions including shock vibrations and temperature fluctuations. Ensure good thermal contact between the thermistor and the surface being measured. Where possible, use thermal grease compatible with the environment (minimal outgassing) to improve conductive heat transfer. Protect thermistors from radiation and electromagnetic interference (EMI) with shielding materials or by placing them in a shielded enclosure.
Platinum RTDs
For high-temperature environments, use RTDs specifically designed to withstand extreme temperatures. Implement thermal bridges or insulation to reduce exposure of RTDs to high temperatures while providing accurate measurements. Regular calibration is crucial to prevent sensor drift. Automatic calibration software routines should be considered for long-duration missions. Install multiple RTDs in critical areas to provide redundancy.
General Recommendations
Choose a sensor provider with a proven record of supplying sensors for space missions. Thorough testing including thermal cycling, shock, vibration, outgassing and radiation exposure testing are critical to confirm that sensor designs are space qualified before integration. Integrate the sensor data into the spacecraft’s thermal management system for real-time monitoring and control. Maintain detailed documentation of sensor placement, calibration procedures and testing results for troubleshooting and reference on future missions.
CASE STUDIES
Landsat Program [USA]
Objective: Long-term Earth observation for monitoring land use, deforestation, urbanization and natural disasters. Managed by NASA and USGS, the Landsat series has been providing continuous data since 1972.
NTC Thermistor applications in Landsat 8 (2013) and 9 (2021): NTC thermistors are integrated into the thermal control systems to monitor and regulate the temperature of the Operational Land Imager (OLI) and the Thermal Infrared Sensor (TIRS). Both instruments require precise temperature management to collect high quality data. Engineers designed these thermistors to operate reliably in harsh space conditions including exposure to radiation, vacuum and extreme temperature fluctuations.
Copernicus Sentinel Missions [Europe]
Objective: Comprehensive Earth observation for environmental monitoring, climate change and disaster management. Operated by the European Space Agency (ESA), the Sentinel satellites provide high-resolution imagery and data for various applications. This program was officially implemented in 2014.
Sentinel-1 satellites are equipped with synthetic aperture radar (SAR) instruments that require precise thermal management to ensure reliable data collection. RTDs are used to monitor and control the temperature of these instruments which is crucial for maintaining accurate radar measurements. Multiple RTDs are used at critical points to maintain instrument reliability.
Galileo GNSS [Europe]
Objective: Providing high-precision global navigation services. Operated by ESA, Galileo offers accurate positioning and timing services for civilian and commercial use. The first satellites in this mission were launched in 2005 with 30 satellites in the current constellation.
NTC thermistors are embedded in the solar arrays of these satellites, protecting the photovoltaic cells from overheating while also providing feedback for performance optimization. Platinum RTDs are essential for maintaining the precise temperature control required for accurate atomic clock operation. These clocks provide highly accurate global positioning and timing.
Iridium NEXT [Global]
Objective: Global satellite communication network. This constellation includes 66 active satellites along with additional spares to provide voice and data coverage to satellite phones, pagers and integrated transceivers around the globe.
Both NTC thermistors and platinum RTDs monitor the satellite’s batteries. RTDs are highly accurate, providing stable measurements over a wide temperature range. NTC thermistors are sensitive to rapid temperature changes which trigger immediate action to protect the satellite’s batteries. The combination of platinum RTDs and NTC thermistors confirm that the batteries operate within their optimal temperature range, preventing overheating and extending their life.
Hubble Space Telescope [USA/Europe]
Objective: Observing astronomical phenomena and deep space. Joint NASA and ESA mission, Hubble has provided groundbreaking data on the universe since 1990.
A combination of NASA qualified NTC thermistors and strain gauges monitor the structural health of the Hubble Space Telescope. Detecting rapid temperature changes along with material deformation, these sensors collaborate to quickly trigger mitigations to confirm the structural integrity of the satellite. In the three decades between this mission and the newer James Webb Space Telescope, the structural health monitors saw new developments in temperature sensors that improved sensitivity and range as well as enhanced durability and reliability.
Mars Reconnaissance Orbiter [USA]
Objective: Studying the atmosphere and terrain of Mars. Launched in 2005 and operated by NASA, this satellite relays high resolution imagery and data on the planet’s climate and geology to scientists back on earth.
NTC thermistors aboard this satellite provide critical sensitivity to its thermal management system. When it first arrived, the MRO entered a highly elliptical orbit around Mars which lasted more than 35 hours. After about six months of aerobraking, a maneuver that uses the planet’s atmosphere correct its orbit, the duration of the orbit is approximately 112 minutes. During this time period, the system must manage extreme changing temperature patterns. Also, in Mars orbit, sensors are exposed to more cosmic and solar radiation. In addition, due to the long duration of the initial flight as well as the intended length of the mission, there were power constraints on the satellite. NASA qualified NTC thermistors with extended range and improved accuracy were employed.
FUTURE TRENDS
As the age of industrial satellites evolves, there are several emerging trends in temperature sensor technology that have potential implications in space. The following highlights a few of these technologies and their likely contributions along with inherent risks that should be considered when adopting new technologies in this high-stakes industry.
Miniaturization is leading to the development of smaller, lighter sensors that consume less power. Taking advantage of semiconductor manufacturing techniques, these sensors are being introduced across the technology landscape from automotive to medicine. In space however, these smaller sensors can introduce vulnerability due to possible instability from these lower mass devices.
Machine learning may enhance the accuracy of sensors by compensating for predicted changes, while adaptive sensing can dynamically adjust sensor parameters to increase performance. In satellite applications, both technologies promise to absorb scarce computational resources and power. This is a substantial risk in an industry that was standardized in 1990’s era microprocessors. These new technologies introduce the possibility of new and unexpected failure modes that can impact the mission’s success.
Many of today’s satellites rely on microprocessors based on older, well proven designs such as Pentium-class and PowerPC 750. Engineers choose these processors based on their reliability and ability to withstand severe conditions beyond the Earth’s atmosphere.
CONCLUSION
NTC thermistors and platinum RTDs are critical components in today’s spacecraft, confirming the reliability, safety, and efficiency of important systems. This paper highlighted unique challenges these sensors face in space, including extreme thermal variations, the absence of convective heat transfer, radiation exposure, mechanical stresses, material outgassing, and power constraints. Understanding these challenges can help engineers make informed decisions when selecting and integrating temperature sensors into designs for satellites and other spacecraft.
The selection criteria for these sensors emphasize the importance of accuracy, stability, response time, power consumption, size, weight, and cost-effectiveness. Integration and placement of temperature sensors require careful consideration of the spacecraft’s thermal environment and the specific requirements of critical components. Best practices include strategic sensor placement, robust mounting techniques, and the use of shielding materials to protect against radiation and electromagnetic interference.
Through case studies, this paper has illustrated the successful application of temperature sensors in various highprofile missions, such as the Landsat Program, Copernicus Sentinel Missions, Galileo GNSS, Iridium NEXT, Hubble Space Telescope, and Mars Reconnaissance Orbiter. These examples demonstrate the importance of reliable temperature sensing in achieving mission success.
Looking ahead, future trends such as miniaturization, machine learning, and adaptive sensing offer exciting possibilities for enhancing sensor performance. However, these innovations must be balanced against the need for long-term reliability and the potential risks associated with new technologies.
In conclusion, the successful implementation of temperature sensors in spacecraft relies on a deep understanding of the challenges, careful selection and integration, and collaboration with experienced suppliers. By leveraging these insights, engineers can ensure the continued success and advancement of space missions.