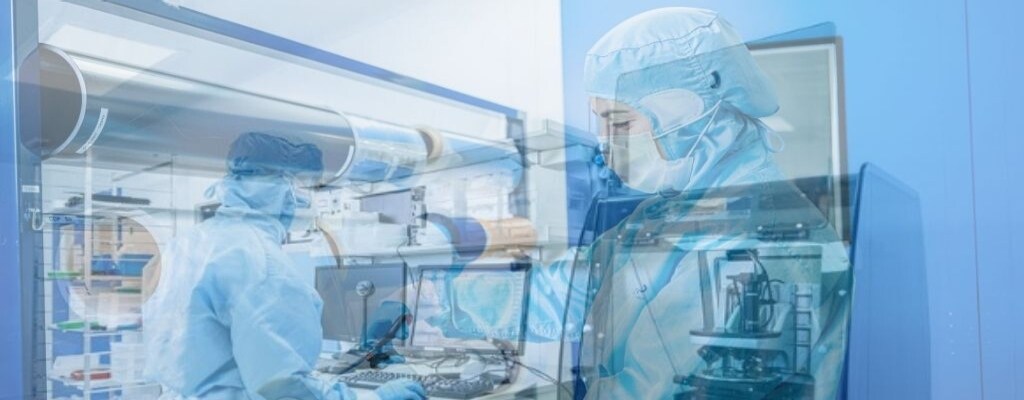
A Primer on Common Diagnostic Microfluidics Materials
Driven in part by COVID-19, interest in the development and manufacturing of microfluidic devices – particularly for disease detection and prevention – has greatly accelerated.
The science and technology underlying the development of microfluidic devices can be overwhelming. This is true even in the selection of materials used in these devices. Even those with advanced degrees and technical experience seek third-party expertise:
- What are the most often-used materials in microfluidics product development?
- Why have these materials been chosen?
- What are the advantages of one material over another?
While this article does not provide a comprehensive review of every material used in microfluidic devices (nor a history of material testing and development), it does take a foundational perspective and offers guidance for further investigation.
Common Microfluidics Materials and Their Uses
The materials used when developing microfluidics devices can have a large impact on the device itself. Microfluidics device developers must balance various considerations: Should the device be low cost? Easily reproducible? Is there a need for portability or disposability?
Will it be used in adverse environments? And, to add additional complexity: the material solution identified could be problematic for different regions due to national regulations about waste management.
A wide range of materials are used in microfluidic devices, but the more common fall into three basic categories:
- Inorganic
- Polymer
- Paper
Each of these materials have different qualities which must be considered in the development of any microfluidic device.
Know about our expertise in microfluidic development and material selection
Inorganic Materials for Use in Microfluidic Devices
Silicon was the first material used in microfluidics due to capabilities associated with wafer fabrication. It has high 3D structural resolution, high thermal conductivity, and can be fabricated in thin membranes. Silicon is useful for making structures within devices. Both silicon and glass offer high resolution capabilities for stationary applications versus mobile point-of-care devices. Conversely, they can be cost prohibitive for certain applications due to complicated fabrication processes that require a cleanroom environment and specialized devices.
Glass is an inflexible material that is ideal for its optical properties and its resistance to solvents and acids. Glass enables a greater range of working temperatures than polymer materials and requires high temperatures to produce. Glass can act as a thermal insulator. Fabrication costs for glass require wet chemistry and can be more expensive as well as more time consuming.
Ceramic devices can be produced at lower cost than silicon or glass. There is some use of ceramic materials in microfluidics, especially given their high thermal properties, excellent chemical resistance and structural integrity, and ability to achieve very small feature dimensions. However, they are most often used in electronic applications.
Polymers for Use in Microfluidic Devices
In general, polymers feature low-cost reproducibility. Depending on the fabrication process, polymers may not require cleanroom conditions. Because they can be molded into many different shapes, most polymers offer greater adaptability than other materials. This makes polymers preferable for lower-cost, disposable point-of-care devices.
PDMS (polydimethylsiloxane) is the most commonly used elastomer. It is known for being an excellent casting material. The advantages of PDMS include biocompatibility, gas permeability, flexibility, UV resistance, and optical clarity. It is also chemically inert and thermally stable. However, some research has shown that PDMS may suffer from absorption of solvents and collapses of channels after bonding.
PMMA (polymethylmethacrylate) is a transparent, low-cost thermoplastic that offers high UV resistance, low water absorption, and good abrasion resistance.
COC (cyclic olefin copolymer) is a thermoplastic that is stiff and strong. It has excellent optical transmission (including light transmission within the UV range), high heat resistance, excellent chemical resistance, and it is minimally absorptive of water. Despite its high cost, it is a go-to material for microfluidic devices requiring optical properties.
PS (polystyrene) is resistant to many chemicals and has excellent electrical properties. PS has been used in microfluidics for cell culture and has had many other uses in the biological and medical areas.
PC (polycarbonate) is a very common, highly transparent thermoplastic with high heat resistance, high stiffness, and strength. However, chemical compatibility is an issue as halogens, gases, some alcohols, and most hydroxides can graze the surface or even dissolve the plastic.
PTEG (polydimethylsiloxane) is a transparent thermoplastic that offers good impact and chemical resistance.
TPE (thermoplastic elastomer) is a soft thermoplastic that offers some of the qualities of both thermoplastics and elastomers. This material is made in strips which can be stored without product degradation for years and has off-the-shelf availability. This material offers optical transparency (if needed) and biocompatibility for implants and is a possible substitute for PDMS.
Hydrogels are chains of polymers with high water absorption rates that may be animal based, plant based, or synthetic.
Paper for Use in Low Cost Microfluidic Devices
Paper is a portable, low-cost option for medium to low complexity bioassays. It can be useful for lateral flow assays and has been used since at least the 17th century as test paper in chemical and biological fields.
Paper has the advantage of internal capillary force; therefore, no external pumps are required. It offers a higher surface-to-volume ratio than conventional microfluidics due to the porosity of the material. Paper-based microfluidics can be fabricated in several ways, including inkjet printing, screen printing, 3D printing, and paper folding, typically with the goal of creating a hydrophobic barrier. A potential drawback of using paper is reagent contamination during storage or transportation due to open channel design.