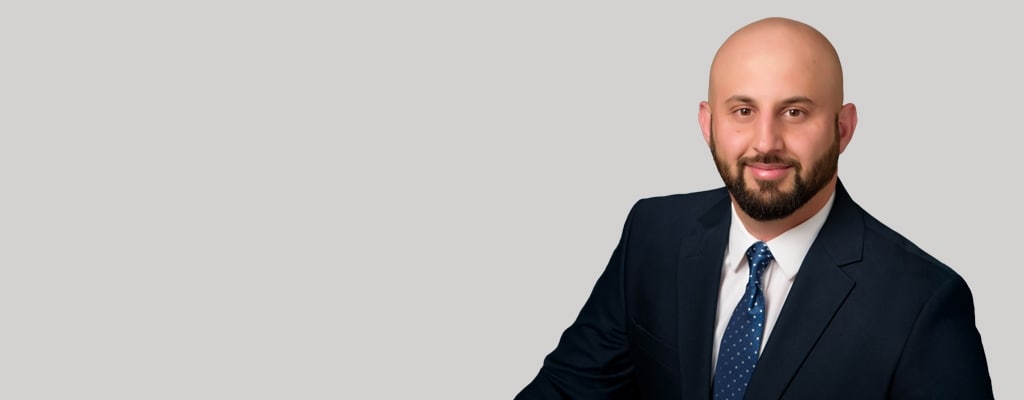
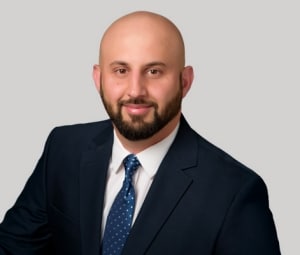
I enjoy solving complex problems that sit at the intersection of design, manufacturability, and performance—especially when those solutions contribute to developing medical devices that can improve patient outcomes.
Jamal joined TE to work on technologies that make a real difference in patients’ lives —backed by a technically strong, collaborative team. He’s driven by solving complex problems and helping shape the development and manufacturing of medical components that balance design, manufacturability and performance. Turning tough engineering challenges into scalable, patient-focused solutions for his customers is what he enjoys the most.
Why did you choose to join TE? What makes you stay here?
I joined TE because I saw the opportunity to work on products that directly impact patients' lives, with the support of a technically strong and well-resourced organization. What’s kept me here is the ability to contribute meaningfully—not just within engineering, but across functions. I’ve been given the space to lead, improve systems, and help shape how we think about product development and manufacturing. That kind of trust and ownership makes a big difference.
What do you enjoy most about your work?
I enjoy solving complex problems that sit at the intersection of design, manufacturability, and performance— especially when those solutions contribute to developing medical devices that could improve patient outcomes. Collaborating cross-functionally with global teams, and mentoring younger engineers, adds even more purpose to the technical challenges.
What has been your most interesting project to work on at TE?
One of the most interesting projects I’ve worked on at TE involved developing a highly complex metal assembly for a next-generation medical device. The geometry and performance requirements pushed the limits of what was manufacturable, requiring close collaboration across design, manufacturing, and supplier teams. We had to rethink traditional metal forming, joining, and inspection methods, and engineer around tight tolerance stack-ups while still ensuring long-term reliability. It was a great example of how deep technical engagement and practical problem-solving come together to deliver a solution that meets both design intent and real-world production constraints.
What are the biggest challenges customers face?
Medical device OEMs are under pressure to move fast without sacrificing quality or compliance. A recurring challenge is translating complex medical device requirements into components that are manufacturable at scale. There’s also a growing need for clean, fast technical communication—an area TE is in a strong position to support due to our deep application and process knowledge.
What personal traits are essential for today’s engineering challenges?
Curiosity, systems thinking, and the ability to communicate across disciplines. Being adaptable and data-literate is increasingly important, but just as critical is knowing when to ask the right questions and how to balance trade-offs. A good engineer today needs to be technically strong, but also collaborative and grounded.
What types of engineering changes do you expect to see over the next five years?
Over the next five years, engineering for medical components and subassemblies will shift toward systems-level thinking, with a strong emphasis on tighter tolerances, advanced manufacturing compatibility, and automation-ready design. Engineers will need to account for specialized materials, full traceability, and increasingly complex subassemblies—all while meeting faster development cycles through simulation and AI-driven tools. Sustainability and regulatory compliance will also play a growing role in material and process choices. Ultimately, success will come from integrating manufacturability, quality, and scalability into the design process from the beginning.
How does TE approach innovation, in a way that directly translates to the solutions we provide to customers?
TE embeds innovation into every stage of development—from customer engagement to internal prototyping. We don’t innovate for the sake of novelty; we focus on solving the right problems. Our strength lies in deep technical partnerships, rigorous validation, and the ability to industrialize solutions quickly. Whether it's co-developing components or proactively designing for manufacturability (DFM), we turn ideas into dependable, scalable solutions.
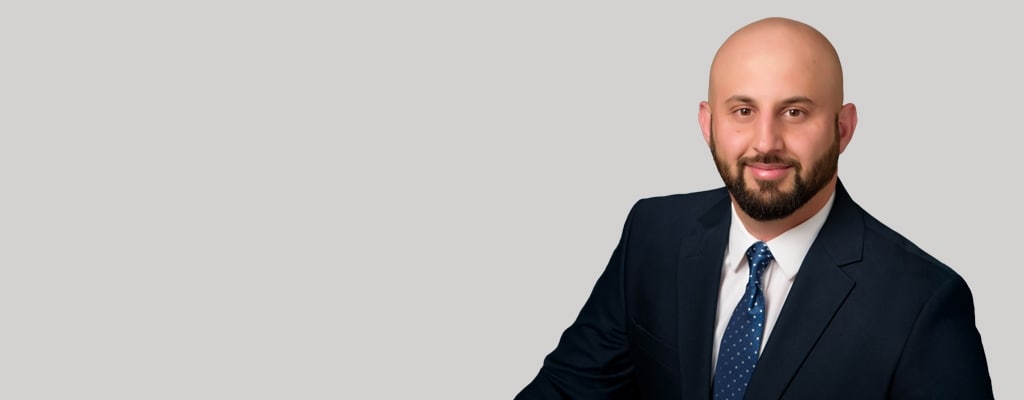
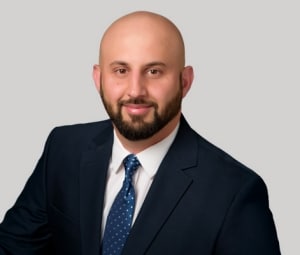
I enjoy solving complex problems that sit at the intersection of design, manufacturability, and performance—especially when those solutions contribute to developing medical devices that can improve patient outcomes.
Jamal joined TE to work on technologies that make a real difference in patients’ lives —backed by a technically strong, collaborative team. He’s driven by solving complex problems and helping shape the development and manufacturing of medical components that balance design, manufacturability and performance. Turning tough engineering challenges into scalable, patient-focused solutions for his customers is what he enjoys the most.
Why did you choose to join TE? What makes you stay here?
I joined TE because I saw the opportunity to work on products that directly impact patients' lives, with the support of a technically strong and well-resourced organization. What’s kept me here is the ability to contribute meaningfully—not just within engineering, but across functions. I’ve been given the space to lead, improve systems, and help shape how we think about product development and manufacturing. That kind of trust and ownership makes a big difference.
What do you enjoy most about your work?
I enjoy solving complex problems that sit at the intersection of design, manufacturability, and performance— especially when those solutions contribute to developing medical devices that could improve patient outcomes. Collaborating cross-functionally with global teams, and mentoring younger engineers, adds even more purpose to the technical challenges.
What has been your most interesting project to work on at TE?
One of the most interesting projects I’ve worked on at TE involved developing a highly complex metal assembly for a next-generation medical device. The geometry and performance requirements pushed the limits of what was manufacturable, requiring close collaboration across design, manufacturing, and supplier teams. We had to rethink traditional metal forming, joining, and inspection methods, and engineer around tight tolerance stack-ups while still ensuring long-term reliability. It was a great example of how deep technical engagement and practical problem-solving come together to deliver a solution that meets both design intent and real-world production constraints.
What are the biggest challenges customers face?
Medical device OEMs are under pressure to move fast without sacrificing quality or compliance. A recurring challenge is translating complex medical device requirements into components that are manufacturable at scale. There’s also a growing need for clean, fast technical communication—an area TE is in a strong position to support due to our deep application and process knowledge.
What personal traits are essential for today’s engineering challenges?
Curiosity, systems thinking, and the ability to communicate across disciplines. Being adaptable and data-literate is increasingly important, but just as critical is knowing when to ask the right questions and how to balance trade-offs. A good engineer today needs to be technically strong, but also collaborative and grounded.
What types of engineering changes do you expect to see over the next five years?
Over the next five years, engineering for medical components and subassemblies will shift toward systems-level thinking, with a strong emphasis on tighter tolerances, advanced manufacturing compatibility, and automation-ready design. Engineers will need to account for specialized materials, full traceability, and increasingly complex subassemblies—all while meeting faster development cycles through simulation and AI-driven tools. Sustainability and regulatory compliance will also play a growing role in material and process choices. Ultimately, success will come from integrating manufacturability, quality, and scalability into the design process from the beginning.
How does TE approach innovation, in a way that directly translates to the solutions we provide to customers?
TE embeds innovation into every stage of development—from customer engagement to internal prototyping. We don’t innovate for the sake of novelty; we focus on solving the right problems. Our strength lies in deep technical partnerships, rigorous validation, and the ability to industrialize solutions quickly. Whether it's co-developing components or proactively designing for manufacturability (DFM), we turn ideas into dependable, scalable solutions.