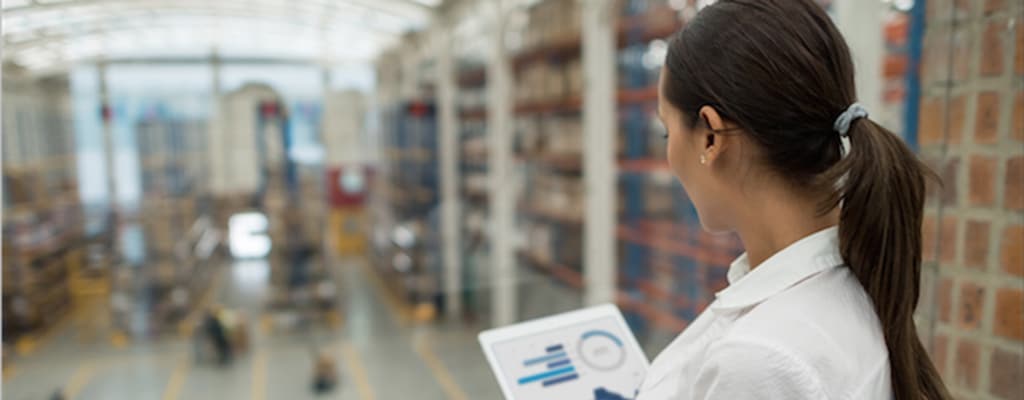
Trend Insight
Building Connections
Wired Brand Lab in collaboration with TE Connectivity brings you this new article on the world of machine-to-machine communications.
AUTHOR
WIRED Brand Lab in collaboration with TE Connectivity
Image credit: Getty Images/Moment RF
Originally published on Wired.com
Machine-to-Machine communication forms a vast plexus of precise data on land, at sea, in the air, and in space. Homes and offices and cars: connected. Products and environments and people: smarter, safer, greener.
Some of this is easy to imagine. Some of it still boggles the mind. A radical new type of interconnectivity has recently come to factories, casting the Industrial Revolution itself in a new light. Back then, society was transitioning from doing everything by hand to using new power sources for increased speed and efficiency. Large-scale factories hummed to life just as engines were starting to become more efficient. These advancements cycled into a second industrial revolution powered by oil and electricity, and finally, a third revolution fueled by digital technology.
As society continues to pursue more efficient production and ways to identify problems more intuitively, factories have become the latest frontier in machine-to-machine communications.
The Next Industrial Revolution
To operate at peak efficiency, every little parameter in the manufacturing space needs to be monitored every millisecond for real-time interoperability throughout production. Previously, these sprawling facilities were outfitted with older sensors that collected data without an Internet connection. Now we live in an era where end-to-end Ethernet-based data communication exists across the production pipeline. Industry experts refer to these vast interconnected networks as the Industrial Internet of Things (IIoT).
These new smart factories connect the physical world to the digital, connecting both the interface and the engineer and practically any machine and any cloud. From simple sensors to complex assembly robots, the machines in these networks generate raw data, analyze it, and process it into real-time visualizations of production. They’re increasingly making the big decisions, and with an array of information they can now nimbly sidestep inefficiency by simply knowing to pause immediately after energy use.
Through multimodal sensing, information about production errors can be instantly aggregated and acted upon. The digitally connected factory can respond to input from any part of the supply chain, including stores selling its products. By being able to easily access data from a product’s entire lifecycle, a manufacturer can also track how much it truly costs to make each unit. Armed with that knowledge, manufacturers are increasingly able to adjust their pricing in response to these real-time metrics.
We’re only at the cusp of this fourth industrial revolution. Products and sensors still need to be designed for use in the field by people who are not engineers. Bandwidth needs to increase and signals need to be more reliable. With truly constant communication, problems get spotted and addressed sooner, manufacturers can save power, and factories can be more flexible, producing a lot of standard products one day and small batches of a particular variant the next. As smaller and smaller elements connect—generating, transmitting, and analyzing data—processes get even more precise.
This newfound innovation can also provide a fix for older factories. Manufacturers can now use cutting-edge tech to make previously offline devices IIoT-compliant. All the data collected can now be processed with data from newer devices – integrating machines, controllers, and drives with networks and IT systems. With that, yesterday’s offline factories become the buzzing smart factories of tomorrow.
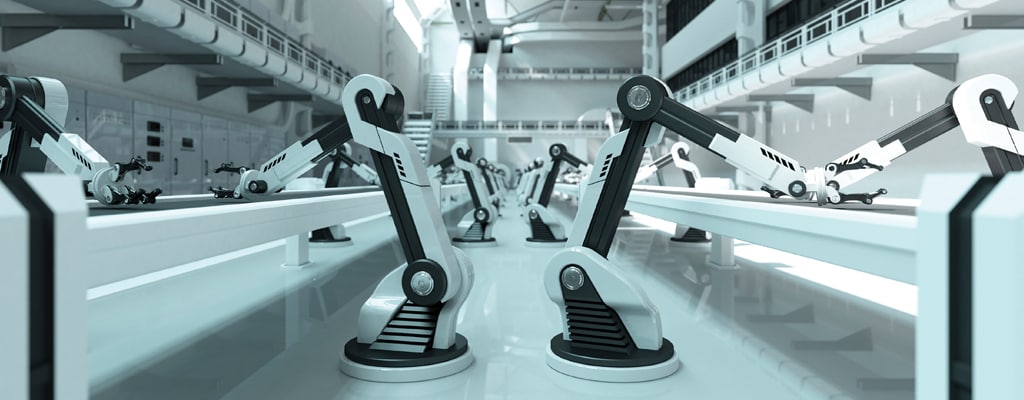
Data-Collecting Work Horses
The variety of applications for IIoT-related tech is nearly endless. It’s not just the factory where things are connected. A world of sensors honed to transmit from the extremes of technology are coming to our homes, workplaces, and beyond.
When spacecraft are prepping for takeoff, sensors are now assessing temperatures upwards of 1,700 degrees Celsius during engine ignition, while another networked sensor system ensures all that heat doesn’t melt the payload. Even the hulking 184-ton hull of these rockets is protected by sensors measuring the crushing aerodynamic force exerted at liftoff.
Or take the example of a high-tech Formula E electric race car zipping around the track at 140 miles per hour. While the vehicle is being evaluated during test laps, critical temperature and pressure data is traveling between the 200-kilowatt vehicle and the pit in a tight loop—and in near-real time. Additional diagnostic data tied to driver inputs and suspension performance is also collected, ready to be offloaded and analyzed by race engineers once a trial run is completed.
Formula E teams are even working to tighten this loop by making the flow of data between vehicles and engineers nearly seamless. With the imminent launch of Roborace, Formula E plans to bring an entire league of sensor-rich self-driving cars to the race track. In a world where a track full of high-powered autonomous super cars are making the split-second decisions, the data-driven bond between vehicle and crew becomes even more crucial.
Everything matters in racing; as it balances safety and the quest for greater and greater speeds, and more information means smarter decisions and a faster path to the checkered flag. Despite the fact that most people will never drive a race car, the data-based optimization of machines like this leads to functional improvements for the entire Internet of Things.
While the precision of these machine-to-machine conversations make sense in high-stakes settings like the race track, they’re also popping up in less likely places like office buildings. The newest connected buildings—like Amsterdam’s app-enabled Edge—are tuned to our behavior, providing data-rich patterns that machines use to make better informed decisions. Even now your thermostat, smartphone, lights, and security system are starting to communicate, and soon they’ll be limited only by how well they can play together.
For instance, let’s say you typically get home from work at 7 p.m. Your thermostat knows this and usually adjusts everything to your own environmental Goldilocks zone – just right. But what if you hit a little traffic? Your HVAC system will be wasting energy—and money—for half an hour. Thanks to machine-to-machine communications, we’re entering an era where your car can assess the situation, calculate the delay, and transmit an updated time of arrival to your home thermostat. In response, your thermostat will tailor its startup to your new estimated arrival. With just a little machine-to-machine chatter and intelligent decision-making, you saved some money and lowered your carbon footprint. Now multiply that by the U.S. Census-estimated 124 million households in the U.S, and you’ve got some serious impact.
An array of sensors are the data-collecting workhorses of this framework. Monitoring everything from humidity, position, pressure, vibration, and velocity to torque, temperature and motion, sensors collect the raw information that fuels machine learning. In an office setting, this would enable the lobby’s microcamera to feed video data into a management system that triggers solid-state downlights to switch on at the presence of visitors. The flow of people in and out of the building is effectively monitored, and an especially sophisticated system could even allow access based on the identity of the person it detects in the building.
Wherever we engage with modern tools—not just in the development of spacecraft and high-performance electrical powertrains—stakes are high. Energy management is tested and modified with a keen eye toward newfound efficiencies and safety. The ways we live, work, and play are being revolutionized by tiny components engaged in endlessly complex interactions—and they’re all powered by the hidden dialogue between our machines.
EXPLORE MORE TRENDS AND INSIGHTS