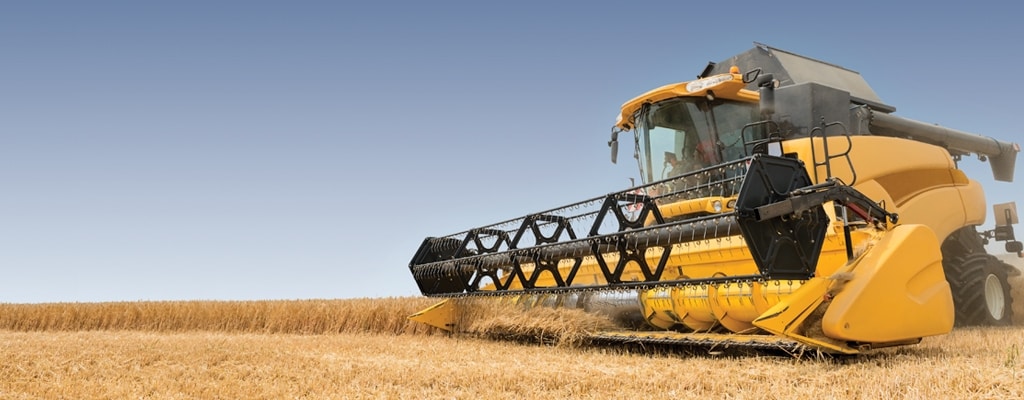
Trend Insight
How to Protect Your Connections?
In heavy industries, vibration, temperature extremes, chemicals, and fluids take their toll on electrical systems. Just one small leak or fault in an electrical system can stop farming operations, cripple a military vehicle, or immobilize a fire truck.
Harsh environment connectors feature several design elements to help protect connections. These features include durable contacts, watertight seals, rugged metal or thermoplastic shells, and a firm, secure locking mechanism. Applications for these types of connector products include ECUs, joysticks, industrial and marine engines, control boxes, lights, and CAN systems, just to mention a few.
Protect Electrical Connections
Connector bodies must be able to stand up to the conditions that they will face in the field and at the worksite. Rugged all-metal bodies and corrosion-resistant thermoplastic shells must be manufactured from high-quality materials selected for their ability to withstand years of environmental exposure. Metal connectors should be built to withstand the force and shock of hard impacts that the connectors face in rough environmental conditions. High-grade thermoplastic connectors need to be engineered to be flame resistant and chemical resistant. Many rugged connectors are available in rectangular or cylindrical body shapes. For harsh environments, they should feature wide operating temperature ranges, secure locking mechanisms, and a positive contact retention system.
Fluid-resistant seals are crucial for connectors in harsh environments. Heavy-duty silicone seals and grommets must work together providing redundant barriers to contamination by fitting tightly around wire insulation and the connector interface. They must be resistant to most common industrial and engine fluids and retain their flexibility across a wide temperature range. A gastight, watertight reliable environmental seal that prevents corrosion and contamination from interrupting the continuity of flow is preferred.
Connectors can be held together by push-latches, threaded coupling rings, lever locks, or tightened together by jackscrews.
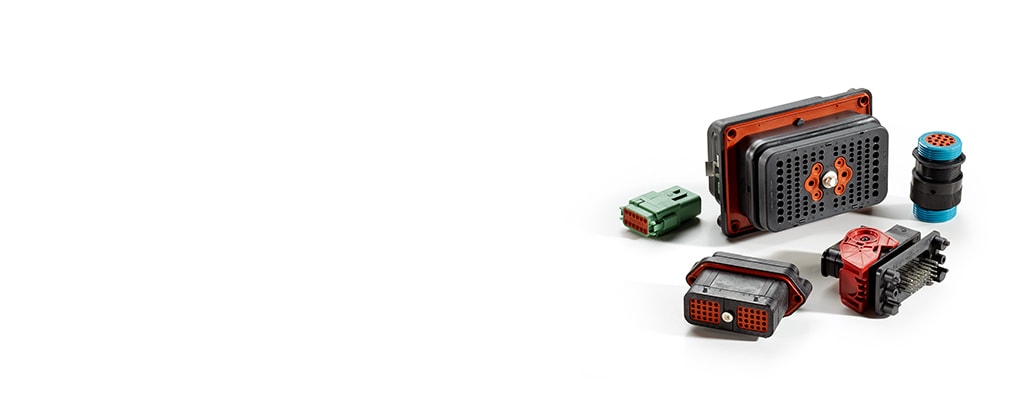
Proper contact alignment is another important aspect of environmentally sealed electrical connectors for harsh environment applications. Secondary locks that snap into or onto the mating face of a connector are often used to help make sure that the contacts slide together properly when they are mated. Wedgelocks and terminal position assurances (TPA) provide additional stability to both the contact barrel and the mated connectors. Many connector wedge locks and TPAs are offered with keying options, further enhancing their design flexibility.
A firm, secure locking mechanism that can withstand vibration and shock is critical to maintaining a steadfast connector engagement in rugged applications. Connectors can be held together by push-latches, threaded coupling rings, lever locks, or tightened together by jackscrews. The locking mechanisms should be easy to engage and disengage and give an audible or tactile signal when they are securely fastened. Once fastened, the locking mechanisms are able to prevent disengagement due to vibration or impact.
Common contacts, tooling, and processes
Design consistency on wiring harnesses streamlines production and field service. Common elements to simplify assembly are contacts, tooling, and processes. When they are common across several connectors, then the time spent on training is reduced, and production is streamlined and simplified. Consistency in production creates a higher quality finished product with less downtime and fewer warranty claims.
Contacts are the heart of the connectors. They are essential in signal and power continuity and if they fail, the systems and applications can fail as well. A common contact system improves performance, reliability, and maintainability by reducing changes in the assembly of the wire harness. The use of a common contact system eliminates many of the failures reported in harnesses where hundreds of different terminations are used. The variation among the contacts is the size of the terminal, which is dictated by the wire gauge. To help confirm a proper crimp and achieve the highest performance specifications, contacts must be crimped with proper tooling.
The strength, accuracy, and overall reliability of a crimped contact should be controlled by the crimp tool, not the operator.
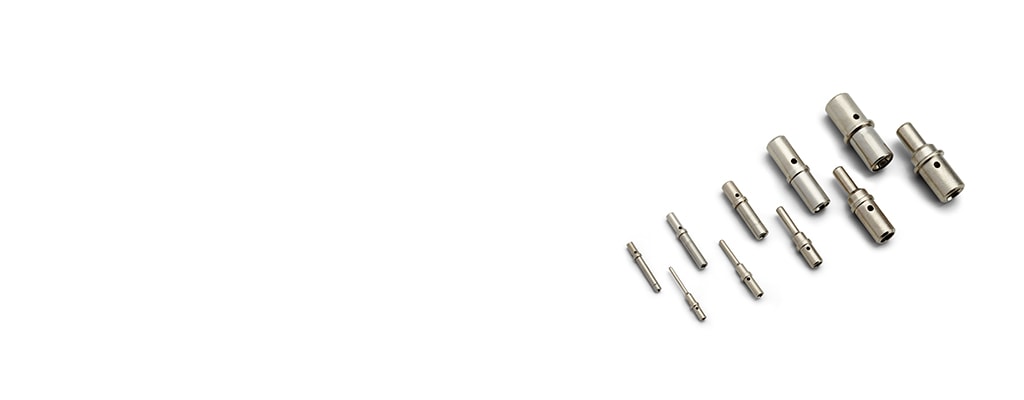
Terminations should be crimped in the field exactly the same as in the factory, using the same tools and the same techniques, and with the same ease of operation and certainty of results. The strength, accuracy, and overall reliability of a crimped contact should be controlled by the crimp tool, not the operator.
Common processes simplify connector assembly. When using connectors that have common contacts and tooling, harness builders can quickly move to another series without having to go through a lengthy training program. This cuts down on the time and the costs associated with learning new procedures. Process consistency significantly reduces assembly time and simplifies field service.
DEUTSCH Connectors
Since even a small degradation in electrical connections can be critical to industrial vehicles, manufacturers are turning to TE Connectivity’s DEUTSCH industrial environmentally sealed electrical connectors to help keep their equipment running. DEUTSCH connectors have the rugged features and the common contacts, tooling, and processes that equipment manufacturers need. No matter the environment, our DEUTSCH industrial connectors provide the innovative solutions demanded by harsh conditions. They are available in different shapes, latching mechanisms, mounting styles, and materials to meet diverse application requirements.
Our dedication to quality and innovation has created a unique system of easy-to-use connectors to simplify processes from start to finish.
-
www.connectorsupplier.com
A version of this article originally appeared in Connector and Cable Assembly Supplier - February 22, 2017