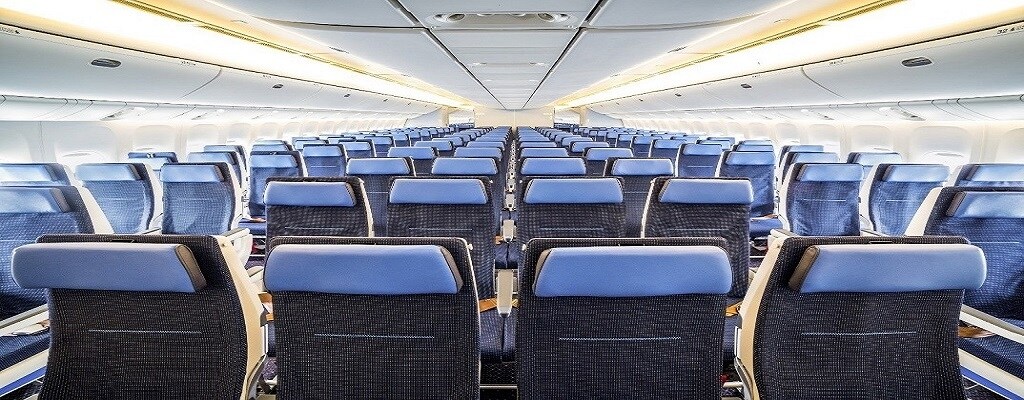
SPE & The Future of In-flight Entertainment
Mini-ETH interconnection system provides size, weight, and performances advantages for Aircraft Ethernet
Today’s passengers and crews are raising their expectations for in-flight entertainment (IFE), security monitoring, and other aircraft electronics. As a result, designers are being challenged to boost performance, reduce bulk, and increase standardization in cabin networks.But aircraft designers cannot meet these challenges with current Ethernet physicallayer standards. The automotive world found their solution in the recently introduced 100Base-T1 (IEEE 802.3bw) standard for Single Pair Ethernet (SPE). Now this standard has been referenced in the soon-to-bereleased ARINC 854 Cabin Equipment Network Bus standard—which is already implemented in Mini-ETH products from TE Connectivity (TE). Thanks to this Ethernet evolution, the Mini-ETH SPE solution can help meet demanding connectivity and size, weight, and power (SWaP) challenges in today’s—and tomorrow’s—aircraft.
CHALLENGES TO AIRCRAFT CONNECTIVITY
Today’s aircraft carry more electronics than ever. Designers must fit screens, sensors, data hubs, switches, solid-state drive (SSD) arrays, computers, IFE servers, and other electronics throughout the airframe and cabin. All those electronics require a lot of wiring. One report notes that stringing all the wiring in a widebody passenger jet from end-to-end would reach from London to Amsterdam or St. Louis to Chicago, nearly 480 kilometers (300 miles) long1. The report estimates that the combined weight of cabling and related harnesses amounts to 7,400 kg (16,280 lbs). That weight is nearly three percent of the maximum takeoff weight of an Airbus A330-200 aircraft2. Excess weight significantly affects fuel performance. For example, consider a Boeing B747-400 wide-body aircraft flying a 5,000nautical-mile average stage length for 3,000 flight hours per year. Carrying the weight of wiring and connectors (1,814 kg/4,000 lbs) consumes nearly 60,000 gallons of jet fuel every year3.The annual cost for that amount of fuel comes to nearly $115,800 USD4. The CO₂ emitted by burning that much fuel amounts to 2,785,200 kg (1,266,000 lbs) annually5 – equivalent to the emissions from 124 passenger vehicles6. To be more sustainable, the aircraft cabin network has to evolve—becoming smarter while growing lighter. Standardized cabin network design concepts are being developed and deployed to address SWaP and connectivity challenges. Modular, scalable distributed architectures promise greater flexibility than classic centralized IT network topologies. Wireless systems that can connect transceivers, antennas, and batteries are also being considered. The starting point for current and future connectivity options is the Ethernet network protocol. Thanks to its versatility, affordability, and universally accepted open standards, Ethernet is evolving at the physical layer to support the SWaP and performance needs of modern aircraft cabin networks
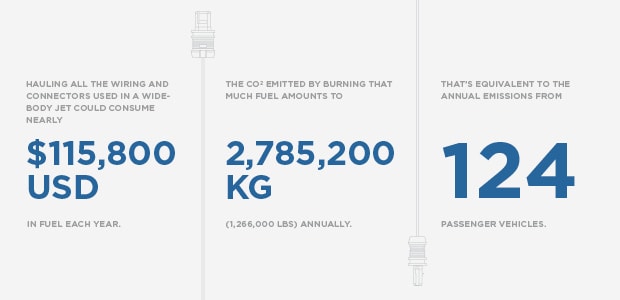
Transitioning Ethernet from Offices to Autos to Aircraft
The Ethernet physical (PHY) layer has evolved, significantly, changing as it moved from offices to automobiles to aircraft. First published in 1983, the initial Institute of Electrical and Electronics Engineers (IEEE) 802.3 standard—also known as 10BASE5—employed a PHY layer nicknamed “thicknet” for its hefty cable size that supported 10 Mbs transmission. Subsequent developments resulted in much thinner cable using two pairs of unshielded twisted wire in the 10BASE-T standard (published in 1990 as IEEE 802.3i).
The successors of 10BASE-T—100BASE-TX (100 Mbs), 1000BASE-T (1 Gbs), and 10GBASE-T (10 Gbs)—still contain four unshielded twisted wire pairs (UTP). Cable design evolved from Category 3 (a voice-grade UTP cable for telephone wiring and 10BASE-T Ethernet) to Category 6 (using four pairs of wire) and beyond. To fit automotive and aircraft needs, engineers have continued to shrink the Ethernet PHY layer.
In 2011, Broadcom Corporation released its BroadR-Reach standard allowing automotive manufacturers to standardize on an open, scalable 100 Mb/s Ethernet-based network protocol. The goal was to accommodate multiple electronic systems, such as advanced driverassistance systems (ADAS) for rear-view cameras and infotainment devices. A BroadR-Reach link offers two-way (full-duplex) operation at a 100 Mbs data rate over a single twisted pair of wires in cable lengths up to 15 m (49 ft). The two-wire design cuts connectivity costs and reduces cable weight nearly in half compared to four and eight wires in commercial-grade Ethernet cables.
The development of BroadR-Reach technology inspired the OPEN Alliance working group, a non-profit, open industry alliance of mainly automotive industry and technology providers, to define 100BASE-T1 as an “Automotive Ethernet” standard. (Broadcom is a promoting member of the OPEN Alliance that developed 100BASE-T1; TE is an adopting member.)
TE implemented 100BASE-T1 in a range of products developed specifically for Automotive Ethernet. The only differences between the BroadR-Reach and 100BASE-T1 standards are the types of PHY chips used at both ends of the link to transmit data. Published as IEEE 802.3bw in 2015, the 100BASE-T1 specification also supports 100 Mbs operation over a single balanced twisted pair cable.
The advantages of adapting Automotive Ethernet for aircraft are readily apparent. 100BASE-T1 standard defines a robust interconnection technology for rugged operating environments where temperature changes and vibration are encountered. It enables cost-efficient, in-vehicle network links and a distributed network architecture for mid-size data volumes and low latencies. It is also scalable up to the 1 Gbps performance of the 1000BASE-T1 specification, with future potential for 5 Gbps using alternative technologies.
As further evidence of robustness, the 100BASE-T1 standard is among several IEEE 802.3 SPE standards positioned as a platform for the Industrial Internet of Things (IIoT). Developments aim to enable Industry 4.0 connectivity by simultaneously delivering data (Ethernet) and remote power (Power-over-DataLine) over a two-wire cable.
Given the technological momentum, transferring the benefits of 100BASE-T1 from automobiles to aircraft was a “no brainer.” Accordingly, the recent ARINC 854 Cabin Equipment Network Bus specification developed by the Cabin Systems Subcommittee (CSS) references the 100BASE-T1 standard. CSS is organized under the Airlines Electronic Engineering Committee (AEEC)—itself operating under ARINC Industry Activities (ARINC IA), a program of SAE Industry Technologies Consortia (SAE ITC).
As a member of the CSS, TE developed a family of 100BASE-T1 products to meet ARINC 854 specifications. The result is the Mini-ETH interconnection system—an end-to-end, pointto-point, SPE solution with significant SWaP and performance advantages for networks in jet airliners and light aircraft.
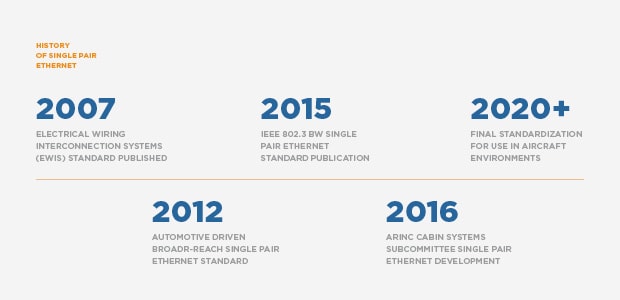
Realizing New SWaP and Performance Advantages with the Mini-ETH Interconnection System
The same TE expertise that developed MATEnet automotive interconnects—and a host of ARINC compliant interconnects for aircraft—is embodied in Mini-ETH technology. The result is an SPE platform that enables aircraft to fly smarter and lighter.
Mini-ETH interconnects are described under ARINC 854 specifications for the Cabin Equipment Network Bus. Compatible connectors and cables are described under ARINC Part Two and Part Three specifications, respectively.
A Mini-ETH interconnection solution reduces SWaP in next-gen aircraft network architectures without compromising signal integrity or network reliability. It provides electrical-wiringinterconnect-systems (EWIS) compliance along with significant SWaP, performance, and implementation advantages.
Significant weight saving & fuel saving advantage
How much could a Mini-ETH interconnection solution contribute to aircraft weight reduction? Let’s look at the earlier example about wiring weight and focus on the Ethernet portion of wiring in a widebody commercial jet. If a Mini-ETH cable/connector solution reduces Ethernet wiring weight by 50 percent, that would reduce the load by 50 kg (110 lbs). If that much weight was eliminated, then annual fuel costs would be cut by $3,185 per aircraft7.In the future, if avionics design moves to a distributed and modular approach as is currently being discussed, a Mini-ETH interconnection solution will also support and enable savings for those developments.
The following advantages provided by MiniETH technology apply to present-day cabinnetwork design:
- Connector Weight and Performance: The design of Mini-ETH connectors is based on the success of TE’s DEUTSCH 369 series connectors, a family of EWIS-compliant rectangular connectors that provide a robust solution in a small envelope. The 369 series connector design was itself based on TE’s DEUTSCH DMC-M series connectors, the classic modular cabin and avionics design used in aerospace applications for nearly three decades. In addition to compactness, the 369 series connector design also provides internal latching and an ergonomic push-button feature that reduces installation time and damage to both the connector and aircraft during installation. The design also offers additional security features that provide extra layers of protection to aircraft systems. Mini-ETH connectors offer as much as 41 percent weight savings compared to typical D-sub connectors. This reduction can eliminate up to 20 kg (44 lbs) or more per plane depending on the configuration and requirements of the network and other aircraft applications.
- Cable Weight and Size: Compared to 4-wire quadraxial cable commonly used for 100 Mbs Ethernet or octal cable with eight 24 AWG wire used in common Category 5e and 6a cable, two-wire Mini-ETH cable is up to 73 percent lighter (Figure 1). The smaller dimensions of Mini-ETH cables with 26 AWG wire improve space utilization. For example, switching from a quadraxial cable with four 24 AWG wires to a Mini-ETH cable with two 26 AWG wires shrinks the cable’s diameter by approximately 15 percent. The jacket construction of Mini-ETH cables is based on TE’s long experience with Raychem precision extruded high-temperature foamed dielectrics. Jacket materials are low smoke, meet the flammability requirements of FAR Part 25, and the toxicity requirements imposed by major aircraft manufacturers. Mini-ETH cabling is described under ARINC 800 Part 3 Specification of Cables. Anticipating further development of ARINC standards, Mini-ETH cables are also provisioned for future operation up to 1,000 Mbs.
- Link Length: Mini-ETH links are certified for 100 Mbs operation at 15 m (49 ft) lengths. Future provisions will enable 40 m (131 ft) lengths and speeds up to 1,000 Mbs.
- Robust Contacts and Lightweight Shells: Mini-ETH connectors employ standard Mil-Spec AS39029 contacts—a high-performance design suitable for harsh environments. These miniaturized contacts are particularly robust against vibration. The connector shell is constructed from rugged materials with strength similar to steel but 40 percent lighter. The combination of composite materials and machined contacts allows for operation in temperatures between -55 °C (131 °F) and up to 175 °C (347 °F)—suitable for aircraft cabin environments.
Nearly 70% Faster
Performance Advantages: Bandwidth, Speed, Signal Integrity, Crosstalk Resistance, Emi, And Lightning Strike:
Bandwidth and Speed: Complying with ARINC 854 adoption of 100BASE-T1 specifications, the MiniETH interconnection system is qualified for 200 MHz and 100 Mbs operation at 15 m (49 ft) link lengths. As future market needs emerge, a roadmap exists to support 1 Gbs and 10 Gbs data speeds, links up to 40 m (131 ft) long, and frequencies over 750MHz. The roadmap also includes new connector designs to accommodate higher frequencies and speeds—and already envisions 1000BASE-T1 for aerospace over longer run lengths.
Signal Integrity: Mini-ETH links have passed 100 Mbs testing over a total of six connections and passes. Impedance, propagation delay, insertion loss (IL), return loss (RL), and longitudinal conversion loss (LCL)/ longitudinal conversion transfer loss (LCTL) all comport with 100BASE-T1 requirements.
Crosstalk: The configuration of the twistedwire pair in Mini-ETH cables inherently minimizes crosstalk, providing the same crosstalk-noisereduction properties common with 100BASE-T1 links.
EMI: Mini-ETH immunity to electromagnetic interference (EMI) also aligns with 100BASE-T1 specifications.
Lightning Strikes: Along with supporting standard electrical signal characteristics, an aircraft interconnect system must also deal with lightning strikes as part of their performance requirements. Mini-ETH interconnection systems are capable of withstanding typical strikes up to 3.6kA.
Implementation Advantages: Easy Mating And Quick Terminations
Mating: The Mini-ETH interconnection system with TE DEUTSCH 369 series connectors meets the need for aircraft cabin connectivity in accord with EWIS best practices. Based on EN4165/ ARINC 809 connectors, Mini-ETH connectors are available in 3, 6, and 9 positions in a compact profile to suit a variety of applications. Installing and maintaining cabling is easy thanks to individually color-coded keying options. Each mated half of the connector can be configured with either male or female contacts, doubling the available keying configurations. The connectors’ rectangular shape and integral ribs permit space-efficient stacking. Cable ties can be used for versatile mounting without the need for additional lock-out fasteners. The scoop-proof interface is particularly suitable for blind-mating or low-visibility conditions. A button-latching mechanism secures mated connectors with an audible click to confirm a complete connection.
Termination time: Compared to a typical quadrax connector with a termination time of 15 to 20 minutes per pair, terminating a MiniETH 369 connector takes 2 to 5 minutes—nearly 70 percent faster. More importantly, the single pair of wires makes Mini-ETH terminations less complex and error prone
Advantages Of Value-Added Systems
Harness design: As a leading global connectivity supplier to the aerospace industry, TE can provide fully assembled harnesses as an integrated, “end-to-end” solution. Connectors and cables can be provided to meet demanding customer requirements while minimizing applied cost. TE supports all phases of an EWIS project—from design to prototype to production—by offering expert design, testing, manufacturing, and supply-chain support with the accountability of a “one-stop-shop.” TE engineers can offer valuable insights into the design of components and interconnected assemblies, guiding users to the right solution for their specific application. With TE HarnWare software, designers can produce high-quality harness assembly drawings, parts lists/bill of materials, labor estimates, connector platform drawings, wiring schematics, and more.
Testing: TE maintains specific test laboratories for insulation and protection (I&P), connectors and fittings (C&F), cable accessories, materials, and other areas. Rigorous testing protocols assure that products will meet exacting durability and performance requirements.
Manufacturing: All TE manufacturing facilities are certified under the AS9000 Aerospace Basic Quality System Standard, validating world-class methods that meet the aerospace industry’s stringent quality-system requirements. In addition to manufacturing discrete components, TE also offers complete, Commercial-Off-The-Shelf (COTS), Plug & Play assemblies that are ready to install and fully tested to meet ARINC 854 requirements.
Supply chain: The TE Aerospace, Defense and Marine business unit offers a fully integrated supply chain for cable assemblies, encompassing wire and cable, tubing, molded parts, devices, backshells, connectors, and identification. TE products include readily available and industryrecognized brands, such as Raychem, DEUTSCH, Polamco, and AMP.
Connecting a Mini-ETH Single Pair Ethernet Solution to Your Project
At the beginning of a design project, it is valuable to view interconnects holistically as part of the system. EVERY CONNECTION COUNTS in reducing aircraft SWaP and ensuring Ethernet network reliability. The Mini-ETH interconnect system offers an integrated family of products described under Aerospace ARINC standards. With the broad Mini-ETH portfolio, designers can achieve the optimum balance between performance, cost, and SWaP. And with a heritage in automotive, energy, and aerospace applications, TE offers practical insights to help designers handle demanding connectivity challenges. Tap our expertise in designing, manufacturing, and implementing all the components along the wire of the connected aircraft: sensors, monitors, IFE systems, video transceivers, Wi-Fi antennas, data links, and more. Our high-performing SPE Mini-ETH interconnection solution can help your Aircraft Ethernet connectivity project perform smarter and lighter.