TE のエンジニアが、電気自動車内の DC 急速充電に関する車両側の熱方程式について語ります。
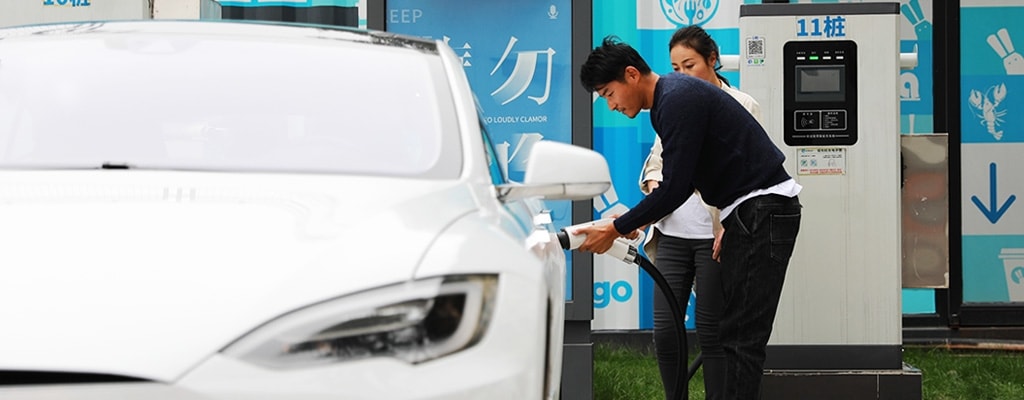
電化されたモビリティのイノベーション
トレンド
次世代の EV 技術
EV エンジニアは、低電圧データ接続ネットワークや高電圧駆動システムを進歩させるために、相互接続、スイッチング、およびセンサ技術を頼りにしています。これを達成するには、ますます統合化が進む集中化された車両ネットワークにおいてこれらの技術を並行して機能させる必要があります。
よく言われるように、次世代のモビリティ (より安全で、環境に優しく、接続性が高い輸送手段) を特徴付けるのは、電気とデータという 2 種類の燃料で動く自動車です。しかし、安全性、利便性、ユビキタス接続への要求から、車内に搭載されたデータ依存型のクラウド/センサ ベース アプリケーションの数はますます増えてますが、多くの消費者は、環境問題を憂慮しているにもかかわらず、依然として電気モビリティ技術を全面的に受け入れることにあまり積極的ではありません。
...「充電ポイントを車載バッテリーに接続する電気システム全体...のすべての導電性コンポーネントを機械的、電気的、熱的に正しく設計し、適切な寸法にする必要があります。」
ユーザの懸念
電気自動車 (EV) の潜在的ユーザの主要な関心事は、航続距離と充電の利便性です。 これらは、充電に要する時間と充電ポイントの利用可能性に関係しています。この点について、充電インレットを EV バッテリーを経由して電気モータにつなげるコネクタ コンポーネントとその接続性は、航続距離を伸ばす安全で信頼性の高いハイパワー急速充電を可能にするために重要な役割を帯びており、消費者の懸念を軽減する効果をもたらします。
今日、ハイウェイの給油所で一般に見られる直流電流 (DC) 急速充電ポイントでの自動車の充電は、充電電力とバッテリー容量によっては最長 1 時間かかり、この充電によって航続距離は約 300 km 追加されます。ただし、電気自動車業界の目標は、約 10 分でこれと同じ航続距離を追加することにあります。これは、内燃機関 (ICE) 自動車の走行距離と給油の間隔に匹敵します。
接続の課題
このハイパワー充電 (HPC) には、最大 500 A の電流を持つ 350 kW の DC 充電ポイントが必要です。 これは、EV の電気システム全体での最高の負荷状態を表します。大量の電力が要求される激しい加速でさえ、平均電流がこれほどのレベルに達することはありません。
このレベルの連続電流が流れると、EV パワートレイン内のすべてのコンポーネント (コネクタ、ケーブル) の固有電気抵抗によって高レベルの熱損失が起こり、自動車が停止中で自然対流冷却がない場合には、熱損失のレベルはさらに高くなります。
したがって、過負荷/過熱を防止するために、受動的または能動的な熱放散、あるいは制御された充電電流のディレーティング (負荷軽減) を促進する機能が、すべての導電性コンポーネントの設計および寸法設定の重要な要件となります。つまり、充電ポイントを車載バッテリーに接続する電気システム全体を機械的、電気的、熱的に正しく設計し、適切な寸法にする必要があります。
注目の EV 用途向けソリューション
大きな課題は、電流が高いほど、 同じ電圧レベルで過熱させずに電力を伝えるために必要なケーブル断面積は大きくなるということです。車両内では、これは主に重量と使用可能なスペースの問題になります。
たとえば、インレットとバッテリー間を接続する導体の断面積が 50 mm2 の場合と 95 mm2 の場合とでは、コスト、重量、体積の点で相当な違いがあります。HPC が現実的な命題となる場合、ケーブルやその他すべての電気コンポーネントのサイズを過度に大きくすることは避ける必要があります。
今日まで、充電中の高いピーク電流と走行時の低い電流の間で動的に変化する電流負荷プロファイル (すなわち、HPC の要件) は、実際には電気コンポーネントの設計に反映されていません。
既存の規格は、リレーや (スイッチ) ヒューズの設計に当初使用された静的な負荷ポイントに基づいています。これは、それらの負荷が発生する頻度とその重要性を反映した統計的手法によって決定されています。そのため、電流負荷値は静的な状態を表しており、対応する電気相互接続コンポーネントの設計は現実を反映していません。つまり、多くの場合、最大約 20% の安全マージンは見込まれていません。
当社のハイブリッド車および電気自動車向けのコネクティビティ ソリューションはパワートレインの全範囲をカバーしており、電力フローを安全に接続および保護するコネクタ、ヘッダ、リレー、コンタクタ、ハーネス、ディスコネクトを包括的に取り揃えています。TE の技術には、HV 補助モジュール、HV パワートレイン、バッテリー接続、充電インレットの 4 つの応用分野で数十年間培われてきた高電圧の発電、送電、配電の経験が活かされています。
バッテリー接続
350 kW を超える充電電力のピーク負荷に対応するためには、 これまでとは異なるアプローチで電気コンポーネントを設計する必要があります。TE では、コンポーネントによる温度上昇とシステム内の熱放散を常に動的に判断する新しい方法論を開発しています。
ほぼ現実に近い系統的な熱シミュレーションに基づけば、コンポーネントの設計をより早い段階で検査し、さまざまな動作モード中のコンポーネントの性能を耐用寿命全体を通して予測できます。これにより、コンポーネントを安全に長期間稼働させ、設計の工夫によって使いやすさを向上させることが可能になります。モデルベースの熱シミュレーションは、将来の負荷プロファイルの検証可能な基礎となり、高電圧/高電流経路に沿ったすべての相互接続コンポーネントの安全性、信頼性、耐久性を証明します。
内燃機関 (ICE) が従来の自動車の心臓部と見なされていたのと同様に、バッテリーは電気自動車の心臓部と考えられ、同じ設計課題の多くが当てはまります。
バッテリー電気自動車 (BEV) では、パワートレインにより多くの電力が必要となります。そのため、自動車基板ネットの物理層への統合が難しくなり、時には要件が矛盾することもあります。
次世代の EV パワートレイン接続を設計するには、充電インレット、高電圧コネクタ、リレー、コンタクタに加えて、EV バッテリー管理システム用の小型低電圧コネクタも必要です。
環境的影響に配慮しながら自動車に典型的なチャネルで高速接続を実現するオプションと、シミュレーション ツールを使用したチャネル分析の緊急性を示す実例をご覧ください。
車両のあらゆる動作モードにおいて、電力はバッテリーの内外を安全に流れる必要があります。 したがって、メインのバッテリー接続には (場合によってはセル モジュール間の接続にも)、ハイパワー充電サイクル中に最大 600 A の電流を数分間伝送し続ける能力が求められます。また、激しい加速中のかなり高いピーク電流も伝送できる必要があります。
バッテリー モジュール接続は、バッテリー保護 (過熱時のシャットダウン)、バッテリー管理 (SoC などの充電状態)、セルバランス維持 (さまざまな SoC レベルでのセル間の充電電圧の均一化) のための物理層も構成します。これらの機能を確保するため、個々のすべてのバッテリー モジュールには、フェイルプルーフを備えた電気接続を実装しなければなりません。
そのためには、高度に統合されたコンタクト システムが必要になります。このコンタクト システムは、車両の耐用寿命 (300,000 km、10 年など) にわたって完全な機能性を維持できるだけでは十分でなく、さらに振動負荷や温度負荷によってコンタクトの機械的および電気的特性に悪影響が及ばないようにする堅牢性も求められます。また、高電圧と高電力による潜在的な危険を排除してメーカと整備担当者の安全を保証するため、コンタクトは完全にタッチセーフでなければなりません。
一例を挙げると、TE の BCON+ モジュール コネクタ システムの第一の設計目標は、400 A の定電流 (と最大 1,200 A の短時間ピーク電流) と最大 1,000 V の電圧を扱えることと、-40°C ~ +80°C の一般的なバッテリー周囲温度で確実に動作させることにありました。主な課題は、電力損失と熱応力を可能な限り低減するために各接点での接触抵抗を最小限に抑え、グローバルな OEM 仕様に準拠した高い耐振動性によって耐用期間中の信頼性を達成することでした。
バッテリー管理
バッテリー管理システムは、 バッテリー パックの充電とその内部セルの放電を管理する電子システムです。バッテリーの動作が安全限度を超えないようにするため、セル モジュールからの温度および電圧信号とパックレベルの電流信号を監視し、それらの信号をセル モジュール環境の均衡化や制御を行う素子に転送します。
バッテリー管理システムは、バッテリーの最適な性能と安全性を確保するためにきわめて重要です。つまり、高い精度と信頼性で動作するとともに、非常に堅牢な構造でなければなりません。さらに、コンパクトかつ軽量で、バッテリー パック全体を可能な限り小さくすることも求められます。
接続性も、バッテリー管理を成功させる鍵です。信号はバッテリー管理コントローラ (BMC) に転送する必要があります。BMC で処理された信号はセル管理コントローラ (CMC) に送信され、セル間のバランスの維持や充電中の電力フローの制御に使用されます。
BMS の電子回路には、非常にコンパクトでありながら柔軟性も兼ね備えたコネクタ システムが必要です。バッテリー セルとセル コントローラの比率は容量や車両のエネルギ需要などのバッテリー設計要件によって異なることを考えると、コネクタ システムには、複数のコネクタ構成を組み替えることができる柔軟性が求められます。また、コネクタには、コンパクトで複雑なバッテリー形状の周囲に配線される FFC/FPC (フラット フレキシブル/プリント ケーブル) などのさまざまなケーブル タイプをサポートする柔軟性も必要となります。
さらに、このコネクタ システムでは、埃やアークによる短絡が生じないように、ピンとピンの間に安全な沿面・空間距離を確保することも要求されます。バッテリー モジュールは密閉されたコンポーネントとして供給されるため、メーカは、すべての内部コネクタが自動車グレードの厳しい堅牢性と信頼性の仕様を満たしていることを保証する必要があります。
注目の電力およびデータ ソリューション
次世代モビリティ向けのコネクティビティ ソリューションを理解することが大切です。 ケーブルとコネクタを構成する物理的な電力およびデータ ネットワーク層は、消費者が求める次世代のより安全で環境に優しいコネクテッド カーのバックボーンとして重要な役割を果たします。
これは、ますます統合化が進む集中化された (スマート) アーキテクチャにおいて、低電圧データ接続ネットワークと高電圧 (HV) 駆動システムをきわめて高い信頼性と安全性で並行して機能させなければならないことを意味します。
相互接続、スイッチング、およびセンサ技術はすべて、これを実現するイノベーションを生み出すための鍵となります。これらの分野で技術的に優れた広範な製品ラインナップと広い専門知識を持つ TE は、次世代モビリティ向けのコネクティビティ ソリューションの構築を目指す自動車技術企業にとって理想的なパートナーです。
著者
- Qiong Sun、副社長、グローバル自動車、ハイブリッド & E モビリティ ソリューション
- Uwe Hauck、製品管理ディレクタ、自動車、ハイブリッド & E モビリティ ソリューション
- Luis Puras Trueba、製品管理上級マネージャ、自動車、ハイブリッド & E モビリティ ソリューション
- Chris Yeadon、マーケティング上級マネージャ、自動車、ハイブリッド & E モビリティ ソリューション