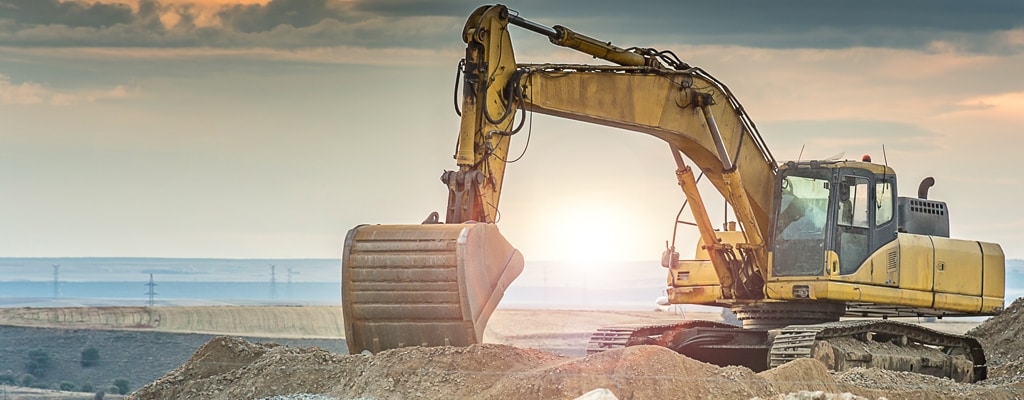
APLICACIÓN
LA PRESIÓN DE FUNCIONAMIENTO EN SISTEMAS Y CIRCUITOS HIDRÁULICOS
Durante las últimas dos décadas, la industria hidráulica se ha beneficiado de los avances en electrónica, la adopción generalizada de la IoT (Internet de las cosas), la reducción de costos en tecnología y la miniaturización de componentes. Además, la industria hidráulica ha observado un aumento en los desafíos durante la transición de los interruptores de presión tradicionales a sensores y transductores de presión, tales como aumentos de presión, temperaturas de funcionamiento más altas, implementación en entornos peligrosos y hostiles, y transitorios de presión. Estos son desafíos para los diseñadores e integradores de sistemas y pueden provocar retrasos en el proyecto o problemas de confiabilidad en el campo si no se abordan adecuadamente. Estos dispositivos de medición de presión también han evolucionado, desde el elemento de detección y el paquete mecánico general hasta la señal de salida electrónica y el acondicionamiento de la señal. En este documento revisaremos la tecnología detrás de los sensores de presión y transductores, los desafíos mecánicos comunes que enfrentan estos sensores y cómo funciona el transductor de presión M9100 de TE Connectivity (TE) en estos entornos desafiantes.
Tecnología de detección
Una mirada al interior del sensor
Desde el exterior, todos los transductores de presión se ven relativamente iguales; sin embargo, el elemento de detección del núcleo varía mucho entre los fabricantes de sensores. Uno de los enfoques económicos y tecnológicamente factibles más comunes es utilizar una galga extensométrica como elemento de detección para transferir la tensión mecánica que la presión induce en un diafragma a una señal de salida eléctrica precisa y repetible. TE utiliza su tecnología de galgas extensométricas Microfused en una configuración de puente de Wheatstone para transformar la tensión en una señal de salida de voltaje. TE diseñó el elemento de detección como un componente mecanizado único integrado con el puerto roscado. Este diseño optimizado proporciona una señal robusta del elemento de detección y brinda grandes niveles de sobrepresión y rendimiento de ruptura.
TE utiliza un proceso de unión de vidrio para fusionar las galgas extensométricas de silicio con un puerto metálico. Las galgas están posicionados de manera óptima para medir adecuadamente la tensión a medida que cambia la presión. Los procesos de unión de cables probados en la industria se utilizan para realizar conexiones entre las galgas y los sistemas electrónicos de acondicionamiento de señales. Las tecnologías competidoras en el mercado de sensores de presión hidráulica, como la deposición de película delgada, la película gruesa y las tecnologías basadas en cerámica, utilizan diafragmas por separado con elementos de detección de baja sensibilidad. Estas tecnologías requieren soldaduras adicionales en las rutas del fluido, juntas tóricas internas o pasos de procesamiento adicionales que pueden ocasionar largos plazos de entrega de la cadena de suministro. Las tecnologías alternativas pueden requerir altas tensiones en el elemento de detección para compensar la baja sensibilidad. Estas altas tensiones junto con la construcción de varias piezas pueden resultar en una reducción de la estabilidad y durabilidad a largo plazo. La tecnología de galgas extensométricas Microfused en TE ha sido probada en la producción de alto volumen durante décadas, tiene un bajo riesgo de interrupción de la cadena de suministro y ofrece una conexión de fluido robusta de una sola pieza, lo que reduce el riesgo de fallas internas del sensor y otros desafíos mecánicos.

Desafíos mecánicos
Como los transductores de presión se instalan como parte de un sistema hidráulico, se deben abordar y reconocer varios desafíos mecánicos dentro del diseño. A continuación se presentan las áreas típicas dentro de los sistemas hidráulicos que los diseñadores de sistemas deben considerar durante el proceso de diseño:
- Presión de funcionamiento
- Picos de presión
- Presión de prueba
- Conexiones de fluidos
- Presión de ruptura
- Choque mecánico/vibraciones
- Fatiga por presión
- Durabilidad frente a factores ambientales
Se aborda cada una de estas inquietudes en el diseño y la validación del sensor. Las clasificaciones de sobrepresión, las clasificaciones de presión de ruptura, el análisis de fatiga y el uso de amortiguadores de presión son parte del proceso de diseño en TE y se validan tanto a través de simulaciones y pruebas empíricas.
Rango de la presión de funcionamiento
En pocas palabras, este es el rango de presión que requiere control o retroalimentación del sistema. En condiciones de funcionamiento típicas, el sistema siempre se mantendrá dentro de este rango. Las presiones fuera de este rango normalmente no requieren una medición.
Presión de prueba
A menudo, en el diseño del sistema ocurren sucesos de presión que exceden el rango de medición necesario, pero no deben causar daños en el sistema. Por lo general, la expectativa es que después de un suceso de sobrepresión, el sistema volverá a su función normal. TE especifica la presión de prueba como la presión que se puede aplicar al elemento sensor sin causar un cambio permanente en la característica de salida o la precisión del transductor de presión.
Presión de ruptura
Puede haber modos de falla potenciales a nivel del sistema que podrían provocar que el sistema experimente presiones excesivas y corra el riesgo de fallar la contención de la presión. TE diseña y valida los transductores de presión tanto teórica como empíricamente para especificar la presión mínima que el sensor puede experimentar sin ruptura.
Fatiga por presión
La fatiga por presión típica se encuentra en sistemas donde hay una bomba o válvula que continuamente da como resultado fluctuaciones de presión en el sistema. Estas fluctuaciones varían en magnitud y frecuencia. Una bomba puede crear una oscilación de presión de alta frecuencia con muy baja magnitud, mientras que una válvula podría provocar un cambio de presión significativo, pero con menos frecuencia. En algunos casos, puede ocurrir lo contrario. Es imposible predecir cada comportamiento potencial del sistema, por lo tanto, el M9100 de TE se prueba desde 0 hasta ciclos de presión a gran escala de hasta 10 millones de ciclos y se valida a nivel teórico para confirmar que las tensiones se mantienen por debajo del límite de fatiga, lo cual proporciona una vida útil esencialmente ilimitada dentro del rango de operación y, a menudo, dentro del rango de presión de prueba. Cabe señalar que debido a que el elemento de detección de TE es mucho más sensible que las tecnologías de la competencia, el nivel de estrés es tan bajo que la fatiga por presión no es una preocupación.
Picos de presión
Posiblemente el desafío más oculto en un sistema hidráulico es la existencia de transitorios de presión de frecuencia muy alta, comúnmente conocidos como “picos de presión”, los cuales a veces se denominan efecto de golpe de ariete. Puede producirse un pico de presión durante el accionamiento de una válvula, ondas de presión impuestas debido a la arquitectura del sistema o el ingreso de aire en la bomba hidráulica. El pico de presión se caracteriza generalmente por un aumento extremadamente rápido de la presión (generalmente microsegundos) a amplitudes muy altas (potencialmente 10 veces más de presión de funcionamiento). La velocidad de un pico de presión puede ser tan rápida que un sensor de presión típico puede no ser capaz de detectar que el suceso ha ocurrido. Sin embargo, este fenómeno puede dañar permanentemente el transductor de presión y causar un cambio de cero permanente, una falla del sensor para responder a la presión o la ruptura del diafragma, lo cual provoca que el fluido se filtre en la carcasa del sensor. A menudo, los clientes no tienen el equipo adecuado para identificar adecuadamente los picos de presión en el sistema; sin embargo, la selección de un transductor de presión con la tecnología correcta ayudará. El sólido diseño M9100 de TE y el amortiguador opcional reducen los posibles modos de falla causados por picos de presión.
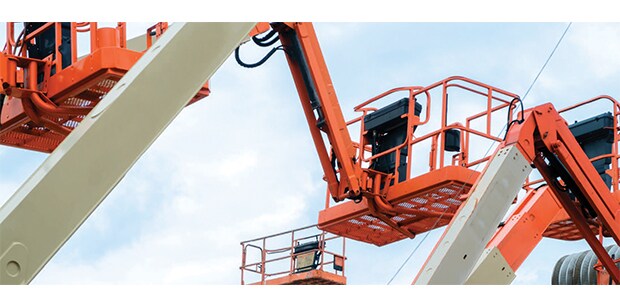
Conexiones de fluidos
Otra consideración mecánica es la conexión al circuito hidráulico. Hay varias opciones de conexión roscada que son populares entre las regiones globales, incluidas SAE (América del Norte), serie G (EMEA) y Metric (APAC). TE tiene una vasta experiencia con las normas históricas de la industria como SAE J1926 o ISO 1179, y continúa manteniéndose al día con los requisitos cambiantes. Cada conexión roscada también tiene sus propias clasificaciones; a medida que las altas presiones se vuelven más comunes dentro de la industria hidráulica, se deben tomar precauciones adicionales para garantizar que el transductor de presión esté correctamente clasificado, asentado y con el par de torsión adecuado.
Choque mecánico/vibraciones
El choque mecánico y la vibración se combinan tradicionalmente dentro de la industria de sensores. Los transductores de presión generalmente están expuestos a condiciones en carretera y todoterreno debido al entorno mecánico específico de las aplicaciones en las que se utilizan. Desde la vibración de alta frecuencia de un motor diésel hasta el choque de una carretilla elevadora que deja caer una carga completa al suelo, estas condiciones requieren que el transductor de presión sea inmune a los efectos adversos de “choque y vibración”.
Durabilidad frente a factores ambientales
La durabilidad frente a factores ambientales es fundamental para garantizar que cualquier producto pueda cumplir con las condiciones extremas del medio ambiente y proporcionar años de servicio confiable. En un sensor de presión se deben considerar el diseño mecánico y las opciones de materiales para garantizar la compatibilidad y la confiabilidad durante toda la vida útil, pero también debe tener en cuenta el impacto de estas condiciones ambientales en el rendimiento a largo plazo del sensor. Ahora que hemos visto los desafíos mecánicos comunes que enfrentan los sensores de presión, echemos un vistazo al sólido diseño del transductor de presión de alto rendimiento M9100 de TE pensado para responder a los desafíos mecánicos de la maquinaria hidráulica crítica.

Diseño robusto
El diseño resistente y el rendimiento fiable del transductor de presión M9100 satisfacen las necesidades de detección de presión de las aplicaciones de alto rendimiento. El sensor M9100 de TE es uno de los mejores de su clase en cuanto a durabilidad hidráulica. El M9100 fue diseñado teniendo en cuenta la simplicidad y la durabilidad para satisfacer o superar las necesidades de las aplicaciones más resistentes. Los diseños complejos que requieren múltiples placas de circuitos, cableado interno y varias interconexiones soldadas suelen ser más vulnerables a daños tempranos y a problemas de confiabilidad en el campo. El M9100 está diseñado para ser simple, compacto y duradero al eliminar tantos modos de falla como sea posible. El transductor de presión logra su tamaño compacto con un solo diseño de placa de circuito impreso. Todas las conexiones soldadas en el sensor están bien controladas por medio de equipos automatizados de recolección y colocación y soldadura por reflujo. No hay conexiones soldadas manuales ni interconexiones soldadas dentro del sensor, ni tampoco apilamiento de placas.
La estructura de diafragma de detección de acero inoxidable mecanizado de una sola pieza elimina los pasos adicionales de ensamblaje, como soldaduras y uniones. La construcción produce un bajo grado de tensión, lo que resulta en una excelente resistencia a la prueba, la ruptura, la fatiga y los picos de presión, lo que reduce el riesgo de problemas tanto durante el proceso de diseño como en el campo. El diseño del sensor Microfused presenta un diafragma extremadamente grueso en comparación con otras tecnologías. Esto permite que el sensor sea más resistente al daño por los picos de presión y contenga completamente estos sucesos de presión. Además, el M9100 de TE cuenta con un amortiguador integral opcional que puede reducir aún más la velocidad y la amplitud de un pico de presión. El diseño integrado elimina la necesidad de un componente separado. La estructura interna del sensor está sellada del entorno externo con una junta tórica. Este diseño protege a los componentes internos del sensor de la niebla salina, la humedad, el lavado a mayor presión y la inmersión.
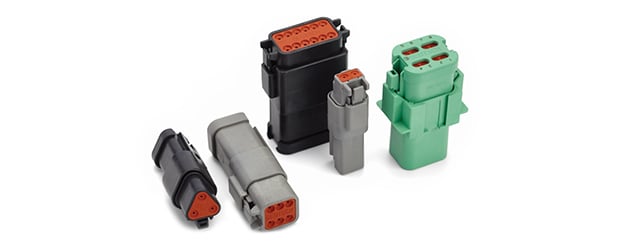
Compatibilidad con sistemas de conexión de alto rendimiento
El transductor de presión M9100 está diseñado para sistemas de conexión grandes y duraderos, como la serie de conectores DEUTSCH DT de TE, una de las mejores de su clase para la protección de ingreso. El sistema de conexión DEUTSCH junto con el robusto diseño del sensor da como resultado un sensor diseñado desde cero para permitir que el sensor sobreviva en una variedad de condiciones adversas y elimina el riesgo de que la niebla salina, la humedad, el polvo o el agua puedan penetrar en el producto y provoquen fallas. Los materiales elegidos para el diseño superan el rango de temperatura de funcionamiento del producto. La elección de materiales termoplásticos, adhesivos y componentes electrónicos (incluido un ASIC con clasificación AEC-Q100) contribuyen a la solidez del producto a temperaturas extremas, luz solar, oxígeno o productos químicos típicos que se encuentran en aplicaciones de equipos de alto rendimiento.

Rendimiento del transductor de presión M9100
La maquinaria hidráulica y sus componentes deben funcionar de manera confiable mientras están expuestos a condiciones extremas. La tecnología central de un sensor de presión es un sistema electromecánico muy complejo. La intención del sensor de presión es convertir la presión de un sistema en una salida eléctrica. A nivel físico, la estrategia es convertir la tensión en una superficie y el “diafragma” en una salida eléctrica que sea directamente proporcional y repetible a la presión aplicada. Sin embargo, la complejidad está en que los elementos utilizados son susceptibles a casi cualquier otra influencia ambiental.
Tecnología de galgas extensométricas
La tecnología de galgas extensométricas de TE, explicada anteriormente en este documento, se ha desarrollado y optimizado durante décadas para minimizar las fuentes de error y proporcionar una salida de presión altamente sensible y repetible. Esta señal de salida se puede corregir y amplificar con el uso de un circuito integrado específico de la aplicación (ASIC). Este ASIC corrige los errores inducidos por errores térmicos y de salida no lineales y las variaciones en el voltaje de alimentación. Esta corrección de errores simplifica la definición base de rendimiento en un término simple llamado banda de error total. La banda de error total es la culminación de todos los errores restantes que el ASIC no puede corregir (incluida la variación de pieza a pieza y de lote a lote) y se define como el error máximo que el usuario experimentará en el rango de temperatura compensada. El M9100 utiliza un ASIC con calificación AEC-Q100 que contiene capacidades de diagnóstico. Los diagnósticos confirman que el sensor funciona correctamente y reducen la posibilidad de una señal de salida incorrecta.
El uso de la especificación de banda de error total en un amplio rango de temperatura (-40 °C a +125 °C) simplifica las expectativas sobre el rendimiento del sensor dentro del sistema. El ASIC también es responsable del acondicionamiento de la señal del sensor; toma la señal de las galgas extensométricas de silicio y la convierte en una señal analógica amplificada. Mientras que el ASIC corrige los errores repetibles, los mismos efectos ambientales pueden causar errores no repetibles, de los cuales el más frecuente es la deriva con el paso del tiempo. La deriva se define como un cambio basado en el tiempo en la salida del sensor. Esta influencia puede provenir de varias fuentes, incluidos cambios en la tensión mecánica en un diafragma (fluencia o relajación del estrés); cambios físicos en el elemento sensor debido a efectos eléctricos o mecánicos, o cambios en la resistividad de las conexiones eléctricas o geles protectores. El ciclo de presión, las sobrepresiones, la exposición a la temperatura, el ciclo de temperatura y la humedad pueden contribuir a esta deriva a largo plazo. La larga experiencia de TE con la tecnología de galgas extensométricas Microfused y los conocidos factores que contribuyen a la deriva ambiental han permitido a TE optimizar el diseño y el procesamiento para proporcionarles a los clientes un producto estable. Desde el concepto hasta la prueba pasando por las pruebas de validación, la galga extensométrica Microfused de TE es una de las mejores tecnologías de detección de su clase.
Alta protección frente a EMI
El entorno eléctrico de los equipos se está volviendo más complejo a medida que se comunican los datos dentro del equipo, así como a su alrededor. Los sensores y transductores están expuestos a crecientes niveles de ruido eléctrico que pueden interferir con la señal si el sensor no está protegido adecuadamente. El M9100 está validado conforme a ISO 11452-2 en cuanto a susceptibilidad irradiada, lo que permite que el producto sobreviva al ruido eléctrico cercano y a la instalación cerca de los componentes emisores de EMI. El M9100 es resistente a interferencias de BCI (inyección de corriente a granel) de hasta 200 mA conforme a ISO 11452-4. Además, el alto nivel de protección eléctrica a la fuente de alimentación hace que el sensor sea más robusto respecto al control deficiente de la fuente de alimentación y reduce el riesgo de problemas del sistema. Si bien se recomienda diseñar un sistema de cableado que no permita conexiones inversas, el M9100 puede sobrevivir a una sobretensión de hasta 28 VCC, voltajes de fuentes de alimentación inversas de hasta 16 VCC y una salida analógica en cortocircuito a V (+) o GND, todo sin experimentar daños. Consulta la hoja de datos del modelo M9100 para obtener una lista completa de las especificaciones de pruebas eléctricas con las que se ha validado el producto.

Conclusión
Los sistemas hidráulicos son un componente esencial de los sistemas de transporte industrial y comercial. La industria hidráulica ha observado un aumento en los desafíos durante la transición de los interruptores de presión tradicionales a sensores y transductores de presión, como aumentos de presión, temperaturas de funcionamiento más altas, implementación en entornos peligrosos y hostiles, y transitorios de presión dentro de los circuitos hidráulicos. El diseño resistente y el rendimiento fiable del transductor de presión M9100 de TE Connectivity responden a estos desafíos y abordan las necesidades de detección de presión de las aplicaciones de alto rendimiento.
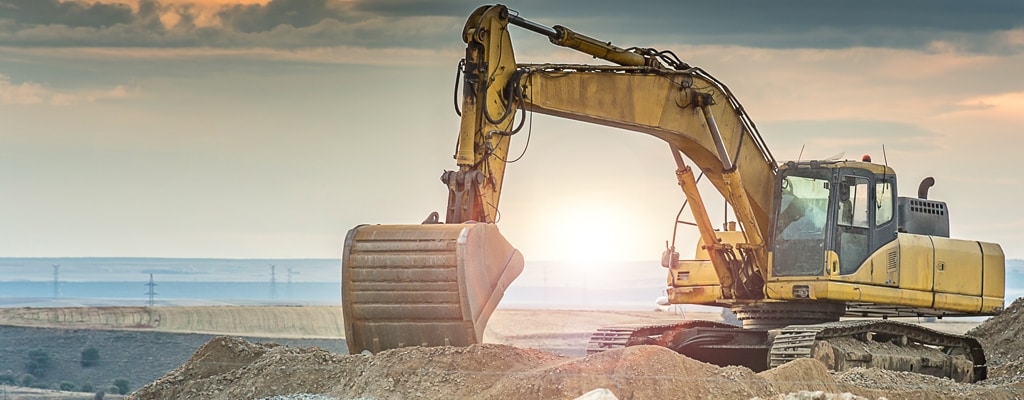
APLICACIÓN
LA PRESIÓN DE FUNCIONAMIENTO EN SISTEMAS Y CIRCUITOS HIDRÁULICOS
Durante las últimas dos décadas, la industria hidráulica se ha beneficiado de los avances en electrónica, la adopción generalizada de la IoT (Internet de las cosas), la reducción de costos en tecnología y la miniaturización de componentes. Además, la industria hidráulica ha observado un aumento en los desafíos durante la transición de los interruptores de presión tradicionales a sensores y transductores de presión, tales como aumentos de presión, temperaturas de funcionamiento más altas, implementación en entornos peligrosos y hostiles, y transitorios de presión. Estos son desafíos para los diseñadores e integradores de sistemas y pueden provocar retrasos en el proyecto o problemas de confiabilidad en el campo si no se abordan adecuadamente. Estos dispositivos de medición de presión también han evolucionado, desde el elemento de detección y el paquete mecánico general hasta la señal de salida electrónica y el acondicionamiento de la señal. En este documento revisaremos la tecnología detrás de los sensores de presión y transductores, los desafíos mecánicos comunes que enfrentan estos sensores y cómo funciona el transductor de presión M9100 de TE Connectivity (TE) en estos entornos desafiantes.
Tecnología de detección
Una mirada al interior del sensor
Desde el exterior, todos los transductores de presión se ven relativamente iguales; sin embargo, el elemento de detección del núcleo varía mucho entre los fabricantes de sensores. Uno de los enfoques económicos y tecnológicamente factibles más comunes es utilizar una galga extensométrica como elemento de detección para transferir la tensión mecánica que la presión induce en un diafragma a una señal de salida eléctrica precisa y repetible. TE utiliza su tecnología de galgas extensométricas Microfused en una configuración de puente de Wheatstone para transformar la tensión en una señal de salida de voltaje. TE diseñó el elemento de detección como un componente mecanizado único integrado con el puerto roscado. Este diseño optimizado proporciona una señal robusta del elemento de detección y brinda grandes niveles de sobrepresión y rendimiento de ruptura.
TE utiliza un proceso de unión de vidrio para fusionar las galgas extensométricas de silicio con un puerto metálico. Las galgas están posicionados de manera óptima para medir adecuadamente la tensión a medida que cambia la presión. Los procesos de unión de cables probados en la industria se utilizan para realizar conexiones entre las galgas y los sistemas electrónicos de acondicionamiento de señales. Las tecnologías competidoras en el mercado de sensores de presión hidráulica, como la deposición de película delgada, la película gruesa y las tecnologías basadas en cerámica, utilizan diafragmas por separado con elementos de detección de baja sensibilidad. Estas tecnologías requieren soldaduras adicionales en las rutas del fluido, juntas tóricas internas o pasos de procesamiento adicionales que pueden ocasionar largos plazos de entrega de la cadena de suministro. Las tecnologías alternativas pueden requerir altas tensiones en el elemento de detección para compensar la baja sensibilidad. Estas altas tensiones junto con la construcción de varias piezas pueden resultar en una reducción de la estabilidad y durabilidad a largo plazo. La tecnología de galgas extensométricas Microfused en TE ha sido probada en la producción de alto volumen durante décadas, tiene un bajo riesgo de interrupción de la cadena de suministro y ofrece una conexión de fluido robusta de una sola pieza, lo que reduce el riesgo de fallas internas del sensor y otros desafíos mecánicos.

Desafíos mecánicos
Como los transductores de presión se instalan como parte de un sistema hidráulico, se deben abordar y reconocer varios desafíos mecánicos dentro del diseño. A continuación se presentan las áreas típicas dentro de los sistemas hidráulicos que los diseñadores de sistemas deben considerar durante el proceso de diseño:
- Presión de funcionamiento
- Picos de presión
- Presión de prueba
- Conexiones de fluidos
- Presión de ruptura
- Choque mecánico/vibraciones
- Fatiga por presión
- Durabilidad frente a factores ambientales
Se aborda cada una de estas inquietudes en el diseño y la validación del sensor. Las clasificaciones de sobrepresión, las clasificaciones de presión de ruptura, el análisis de fatiga y el uso de amortiguadores de presión son parte del proceso de diseño en TE y se validan tanto a través de simulaciones y pruebas empíricas.
Rango de la presión de funcionamiento
En pocas palabras, este es el rango de presión que requiere control o retroalimentación del sistema. En condiciones de funcionamiento típicas, el sistema siempre se mantendrá dentro de este rango. Las presiones fuera de este rango normalmente no requieren una medición.
Presión de prueba
A menudo, en el diseño del sistema ocurren sucesos de presión que exceden el rango de medición necesario, pero no deben causar daños en el sistema. Por lo general, la expectativa es que después de un suceso de sobrepresión, el sistema volverá a su función normal. TE especifica la presión de prueba como la presión que se puede aplicar al elemento sensor sin causar un cambio permanente en la característica de salida o la precisión del transductor de presión.
Presión de ruptura
Puede haber modos de falla potenciales a nivel del sistema que podrían provocar que el sistema experimente presiones excesivas y corra el riesgo de fallar la contención de la presión. TE diseña y valida los transductores de presión tanto teórica como empíricamente para especificar la presión mínima que el sensor puede experimentar sin ruptura.
Fatiga por presión
La fatiga por presión típica se encuentra en sistemas donde hay una bomba o válvula que continuamente da como resultado fluctuaciones de presión en el sistema. Estas fluctuaciones varían en magnitud y frecuencia. Una bomba puede crear una oscilación de presión de alta frecuencia con muy baja magnitud, mientras que una válvula podría provocar un cambio de presión significativo, pero con menos frecuencia. En algunos casos, puede ocurrir lo contrario. Es imposible predecir cada comportamiento potencial del sistema, por lo tanto, el M9100 de TE se prueba desde 0 hasta ciclos de presión a gran escala de hasta 10 millones de ciclos y se valida a nivel teórico para confirmar que las tensiones se mantienen por debajo del límite de fatiga, lo cual proporciona una vida útil esencialmente ilimitada dentro del rango de operación y, a menudo, dentro del rango de presión de prueba. Cabe señalar que debido a que el elemento de detección de TE es mucho más sensible que las tecnologías de la competencia, el nivel de estrés es tan bajo que la fatiga por presión no es una preocupación.
Picos de presión
Posiblemente el desafío más oculto en un sistema hidráulico es la existencia de transitorios de presión de frecuencia muy alta, comúnmente conocidos como “picos de presión”, los cuales a veces se denominan efecto de golpe de ariete. Puede producirse un pico de presión durante el accionamiento de una válvula, ondas de presión impuestas debido a la arquitectura del sistema o el ingreso de aire en la bomba hidráulica. El pico de presión se caracteriza generalmente por un aumento extremadamente rápido de la presión (generalmente microsegundos) a amplitudes muy altas (potencialmente 10 veces más de presión de funcionamiento). La velocidad de un pico de presión puede ser tan rápida que un sensor de presión típico puede no ser capaz de detectar que el suceso ha ocurrido. Sin embargo, este fenómeno puede dañar permanentemente el transductor de presión y causar un cambio de cero permanente, una falla del sensor para responder a la presión o la ruptura del diafragma, lo cual provoca que el fluido se filtre en la carcasa del sensor. A menudo, los clientes no tienen el equipo adecuado para identificar adecuadamente los picos de presión en el sistema; sin embargo, la selección de un transductor de presión con la tecnología correcta ayudará. El sólido diseño M9100 de TE y el amortiguador opcional reducen los posibles modos de falla causados por picos de presión.
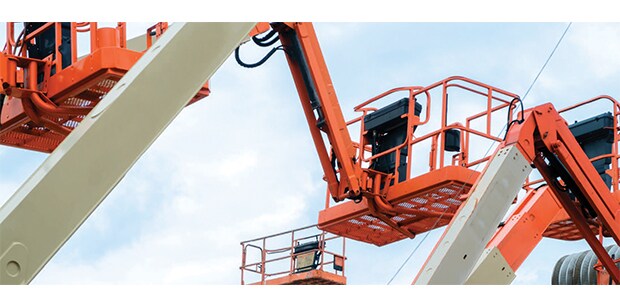
Conexiones de fluidos
Otra consideración mecánica es la conexión al circuito hidráulico. Hay varias opciones de conexión roscada que son populares entre las regiones globales, incluidas SAE (América del Norte), serie G (EMEA) y Metric (APAC). TE tiene una vasta experiencia con las normas históricas de la industria como SAE J1926 o ISO 1179, y continúa manteniéndose al día con los requisitos cambiantes. Cada conexión roscada también tiene sus propias clasificaciones; a medida que las altas presiones se vuelven más comunes dentro de la industria hidráulica, se deben tomar precauciones adicionales para garantizar que el transductor de presión esté correctamente clasificado, asentado y con el par de torsión adecuado.
Choque mecánico/vibraciones
El choque mecánico y la vibración se combinan tradicionalmente dentro de la industria de sensores. Los transductores de presión generalmente están expuestos a condiciones en carretera y todoterreno debido al entorno mecánico específico de las aplicaciones en las que se utilizan. Desde la vibración de alta frecuencia de un motor diésel hasta el choque de una carretilla elevadora que deja caer una carga completa al suelo, estas condiciones requieren que el transductor de presión sea inmune a los efectos adversos de “choque y vibración”.
Durabilidad frente a factores ambientales
La durabilidad frente a factores ambientales es fundamental para garantizar que cualquier producto pueda cumplir con las condiciones extremas del medio ambiente y proporcionar años de servicio confiable. En un sensor de presión se deben considerar el diseño mecánico y las opciones de materiales para garantizar la compatibilidad y la confiabilidad durante toda la vida útil, pero también debe tener en cuenta el impacto de estas condiciones ambientales en el rendimiento a largo plazo del sensor. Ahora que hemos visto los desafíos mecánicos comunes que enfrentan los sensores de presión, echemos un vistazo al sólido diseño del transductor de presión de alto rendimiento M9100 de TE pensado para responder a los desafíos mecánicos de la maquinaria hidráulica crítica.

Diseño robusto
El diseño resistente y el rendimiento fiable del transductor de presión M9100 satisfacen las necesidades de detección de presión de las aplicaciones de alto rendimiento. El sensor M9100 de TE es uno de los mejores de su clase en cuanto a durabilidad hidráulica. El M9100 fue diseñado teniendo en cuenta la simplicidad y la durabilidad para satisfacer o superar las necesidades de las aplicaciones más resistentes. Los diseños complejos que requieren múltiples placas de circuitos, cableado interno y varias interconexiones soldadas suelen ser más vulnerables a daños tempranos y a problemas de confiabilidad en el campo. El M9100 está diseñado para ser simple, compacto y duradero al eliminar tantos modos de falla como sea posible. El transductor de presión logra su tamaño compacto con un solo diseño de placa de circuito impreso. Todas las conexiones soldadas en el sensor están bien controladas por medio de equipos automatizados de recolección y colocación y soldadura por reflujo. No hay conexiones soldadas manuales ni interconexiones soldadas dentro del sensor, ni tampoco apilamiento de placas.
La estructura de diafragma de detección de acero inoxidable mecanizado de una sola pieza elimina los pasos adicionales de ensamblaje, como soldaduras y uniones. La construcción produce un bajo grado de tensión, lo que resulta en una excelente resistencia a la prueba, la ruptura, la fatiga y los picos de presión, lo que reduce el riesgo de problemas tanto durante el proceso de diseño como en el campo. El diseño del sensor Microfused presenta un diafragma extremadamente grueso en comparación con otras tecnologías. Esto permite que el sensor sea más resistente al daño por los picos de presión y contenga completamente estos sucesos de presión. Además, el M9100 de TE cuenta con un amortiguador integral opcional que puede reducir aún más la velocidad y la amplitud de un pico de presión. El diseño integrado elimina la necesidad de un componente separado. La estructura interna del sensor está sellada del entorno externo con una junta tórica. Este diseño protege a los componentes internos del sensor de la niebla salina, la humedad, el lavado a mayor presión y la inmersión.
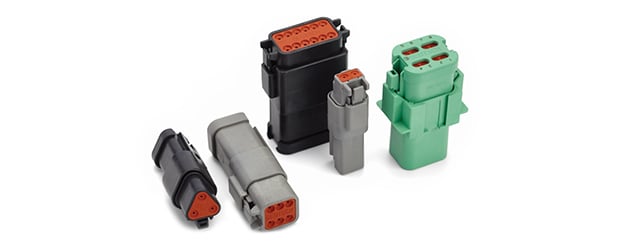
Compatibilidad con sistemas de conexión de alto rendimiento
El transductor de presión M9100 está diseñado para sistemas de conexión grandes y duraderos, como la serie de conectores DEUTSCH DT de TE, una de las mejores de su clase para la protección de ingreso. El sistema de conexión DEUTSCH junto con el robusto diseño del sensor da como resultado un sensor diseñado desde cero para permitir que el sensor sobreviva en una variedad de condiciones adversas y elimina el riesgo de que la niebla salina, la humedad, el polvo o el agua puedan penetrar en el producto y provoquen fallas. Los materiales elegidos para el diseño superan el rango de temperatura de funcionamiento del producto. La elección de materiales termoplásticos, adhesivos y componentes electrónicos (incluido un ASIC con clasificación AEC-Q100) contribuyen a la solidez del producto a temperaturas extremas, luz solar, oxígeno o productos químicos típicos que se encuentran en aplicaciones de equipos de alto rendimiento.

Rendimiento del transductor de presión M9100
La maquinaria hidráulica y sus componentes deben funcionar de manera confiable mientras están expuestos a condiciones extremas. La tecnología central de un sensor de presión es un sistema electromecánico muy complejo. La intención del sensor de presión es convertir la presión de un sistema en una salida eléctrica. A nivel físico, la estrategia es convertir la tensión en una superficie y el “diafragma” en una salida eléctrica que sea directamente proporcional y repetible a la presión aplicada. Sin embargo, la complejidad está en que los elementos utilizados son susceptibles a casi cualquier otra influencia ambiental.
Tecnología de galgas extensométricas
La tecnología de galgas extensométricas de TE, explicada anteriormente en este documento, se ha desarrollado y optimizado durante décadas para minimizar las fuentes de error y proporcionar una salida de presión altamente sensible y repetible. Esta señal de salida se puede corregir y amplificar con el uso de un circuito integrado específico de la aplicación (ASIC). Este ASIC corrige los errores inducidos por errores térmicos y de salida no lineales y las variaciones en el voltaje de alimentación. Esta corrección de errores simplifica la definición base de rendimiento en un término simple llamado banda de error total. La banda de error total es la culminación de todos los errores restantes que el ASIC no puede corregir (incluida la variación de pieza a pieza y de lote a lote) y se define como el error máximo que el usuario experimentará en el rango de temperatura compensada. El M9100 utiliza un ASIC con calificación AEC-Q100 que contiene capacidades de diagnóstico. Los diagnósticos confirman que el sensor funciona correctamente y reducen la posibilidad de una señal de salida incorrecta.
El uso de la especificación de banda de error total en un amplio rango de temperatura (-40 °C a +125 °C) simplifica las expectativas sobre el rendimiento del sensor dentro del sistema. El ASIC también es responsable del acondicionamiento de la señal del sensor; toma la señal de las galgas extensométricas de silicio y la convierte en una señal analógica amplificada. Mientras que el ASIC corrige los errores repetibles, los mismos efectos ambientales pueden causar errores no repetibles, de los cuales el más frecuente es la deriva con el paso del tiempo. La deriva se define como un cambio basado en el tiempo en la salida del sensor. Esta influencia puede provenir de varias fuentes, incluidos cambios en la tensión mecánica en un diafragma (fluencia o relajación del estrés); cambios físicos en el elemento sensor debido a efectos eléctricos o mecánicos, o cambios en la resistividad de las conexiones eléctricas o geles protectores. El ciclo de presión, las sobrepresiones, la exposición a la temperatura, el ciclo de temperatura y la humedad pueden contribuir a esta deriva a largo plazo. La larga experiencia de TE con la tecnología de galgas extensométricas Microfused y los conocidos factores que contribuyen a la deriva ambiental han permitido a TE optimizar el diseño y el procesamiento para proporcionarles a los clientes un producto estable. Desde el concepto hasta la prueba pasando por las pruebas de validación, la galga extensométrica Microfused de TE es una de las mejores tecnologías de detección de su clase.
Alta protección frente a EMI
El entorno eléctrico de los equipos se está volviendo más complejo a medida que se comunican los datos dentro del equipo, así como a su alrededor. Los sensores y transductores están expuestos a crecientes niveles de ruido eléctrico que pueden interferir con la señal si el sensor no está protegido adecuadamente. El M9100 está validado conforme a ISO 11452-2 en cuanto a susceptibilidad irradiada, lo que permite que el producto sobreviva al ruido eléctrico cercano y a la instalación cerca de los componentes emisores de EMI. El M9100 es resistente a interferencias de BCI (inyección de corriente a granel) de hasta 200 mA conforme a ISO 11452-4. Además, el alto nivel de protección eléctrica a la fuente de alimentación hace que el sensor sea más robusto respecto al control deficiente de la fuente de alimentación y reduce el riesgo de problemas del sistema. Si bien se recomienda diseñar un sistema de cableado que no permita conexiones inversas, el M9100 puede sobrevivir a una sobretensión de hasta 28 VCC, voltajes de fuentes de alimentación inversas de hasta 16 VCC y una salida analógica en cortocircuito a V (+) o GND, todo sin experimentar daños. Consulta la hoja de datos del modelo M9100 para obtener una lista completa de las especificaciones de pruebas eléctricas con las que se ha validado el producto.

Conclusión
Los sistemas hidráulicos son un componente esencial de los sistemas de transporte industrial y comercial. La industria hidráulica ha observado un aumento en los desafíos durante la transición de los interruptores de presión tradicionales a sensores y transductores de presión, como aumentos de presión, temperaturas de funcionamiento más altas, implementación en entornos peligrosos y hostiles, y transitorios de presión dentro de los circuitos hidráulicos. El diseño resistente y el rendimiento fiable del transductor de presión M9100 de TE Connectivity responden a estos desafíos y abordan las necesidades de detección de presión de las aplicaciones de alto rendimiento.