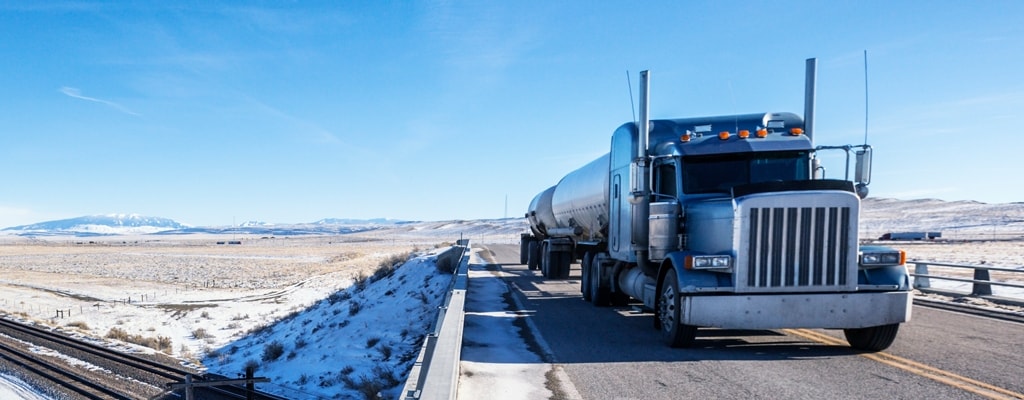
Trend Insight
Ethernet’s Importance in Enabling Trends
Discover why design engineers must consider incorporating Ethernet systems in their industrial and commercial vehicles and machinery to meet future customers' needs.
Authors
By Joachim Barth, R&D/Product Development Engineering Manager, and Christian Manko, Data Connectivity Product Manager, TE Connectivity
Agricultural, construction and other heavy-duty vehicles are typically built to last several years or more depending on the type of vehicle. So, manufacturers must be able to design for future trends to give customers the most long-term value. The pace of technology change makes this a difficult task, but one advantage the industrial and commercial transportation industry has is it can use the knowledge and technology from future-focused applications already proven in the automotive industry.
As automated functionality and data, connectivity demands continue to increase in the industrial and commercial transportation sector, the CAN bus protocol is quickly reaching its limits. To stay on top of megatrends driving these demands—such as green, safe, connected, and productive—designers must consider incorporating Ethernet systems in their designs now to be able to meet customer demands in the near future and beyond.
Trends impacting design
Industrial and commercial vehicle designers are working to make the next generation of trucks, buses, and off-road vehicles safer, greener, more connected and more productive. To make this happen, they are introducing advanced automated functionality, which was previously developed only for passenger vehicles, to help increase productivity and drive down the total cost of ownership.
Driver assistance and automation features, infotainment options, 360-degree camera systems, high-speed vehicle-to-vehicle (V2V) and vehicle-to-infrastructure (V2I) communication, and a wide range of essential safety features are becoming standard requirements for new heavy-duty vehicles. Currently, the industry is at level 2—partial automation. In four to five years, we expect the market to be at level 4, with a high level of automated function in most new vehicles. This means functional safety must be integrated not only into the design but also as part of the development and quality management process in order to meet ISO 26262 as well as future standards.
Commercial vehicles of the future will “know” more about their environment and the route ahead, as well as send feedback to a home base that can be analyzed and acted upon to improve performance and productivity. These technologies and the ones mentioned below deliver increased driver satisfaction, better productivity and lower total cost of ownership (TCO) for vehicle owners, and far greater performance feedback for manufacturers.
Trends
The following are just some example of emerging trends we’re seeing across the market:
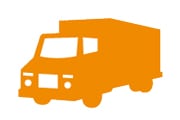
On-Highway Trucks and Buses
Safety, productivity, and sustainability in operations are three trends in on-highway trucks and buses that must be addressed in new vehicle designs. Blind spots for the drivers of these vehicles can lead to accidents with other vehicles, bicyclists, and pedestrians. For example, in Germany and other countries around the world, drivers of heavy-duty vehicles have, due to blind spots, struck pedestrians or bicyclists as they make a right turn. Soon, in Germany and other countries, mandatory regulations may require heavy-duty vehicles to have sensors and cameras to enable more sophisticated blind spot detection and alarms to help avoid these types of accidents. Telemetrics can help facilitate online freight disposition and route planning, as well as optimize driving behavior to help increase safety and productivity. Predictive cruise control determines the ideal speed for vehicles depending on road conditions. This saves fuel, giving drivers more productive time on the road without interruption. Vehicle-to-vehicle communications enable vehicle platooning for multiple drivers to increase safety and reduce fuel consumption. Vehicle-to-infrastructure communication is essential for Advanced Driver Assist Systems (ADAS) and eventually complete autonomous driving. These features all rely on a network of sensors and high-speed/low-latency data connections.
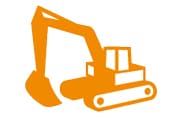
Off-Highway Construction and Mining Vehicles
Because of their size and configuration, off-highway vehicles have accidents or rollovers most often when they are backing up or traveling over trenches, holes, or uneven terrain. Today’s 360-degree camera systems are essential to help the driver maneuver safely over varied terrain and create a safer worksite. From a productivity standpoint, manufacturers want to give customers more technologies that make the machines run reliably and efficiently. The challenge is to add connectivity that enables the intake of key information from the environment for a real-time response while also withstanding dirt, chemicals, water, high vibration, and thermal shock. As technology advances, construction and mining equipment will use this data connectivity to become smarter and more automated, eventually enabling some operators to work remotely in complete safety. Preventive diagnostics is another valuable tool that helps with reliability, productivity, and costs. Advanced functionality can predict when a part may fail or require replacement before a vehicle or machine breaks down. This is especially valuable for both off-highway construction vehicles and agricultural machinery, where a sudden and prolonged work stoppage could be costly.

Agricultural Vehicles and Machinery
Productivity and sustainability are two very important trends in the agricultural industry especially given the pressure on farmers to minimize the effect on local resources (such as water supplies and air quality). Advances in connectivity and automation in agricultural machinery can enable and improve precision farming and smart farming to address these key challenges. For example, treatment of weeds and application of pesticides can be made more precise so that farmers can yield the most crops possible and not affect neighboring lands, farms, or drinking water supplies. Thinking about the future, agricultural machines can use sensors, data, and connectivity to understand weather patterns and then adapt and calculate seeding, irrigation, pesticides, and harvesting down to the last second and last plant in a field. Manufacturers of agricultural equipment must produce vehicles that can detect, identify and make management decisions about every plant in the field – ultimately reducing costs as well as improving sustainability.
More sophisticated networks
All these trends and technologies require a sophisticated network infrastructure that can handle increased data demands to make all communication possible—within the vehicle, from one vehicle to another, or between the vehicle and another location such as a depot or control center and even the manufacturer. This network needs to transmit high-speed data with low latency while operating in harsh conditions. So far, CAN bus architectures have been able to serve as the backbone for a vehicle’s network. As designers look to incorporate more automated features for safety and productivity, the data bandwidth required for advanced vehicle functionality is too great to be served by CAN alone. The transition to Ethernet has begun, first in areas where higher bandwidth and performance are required and eventually replacing CAN as automation becomes more prevalent and more power and bandwidth needs to be integrated throughout the system.
Currently, most sensor and connectivity systems in vehicles for ADAS are dedicated systems. One function or application, like adaptive cruise control, has sensors for radar/lidar and connectors that feed into one electronic control unit (ECU). As automated functions increase in these vehicles, sensor fusion—where data from several sensors can be combined and analyzed—becomes increasingly vital to collect more accurate positioning and environmental information. For example, while in passenger automobiles sensors are needed to detect obstacles on solid roads, in construction, mining, and agriculture, sensors need to detect material properties as well. If a farm combine is crossing a field harvesting crops and an obstacle that looks like a stick is detected in its path, it needs to know whether that object is a lightweight stick that can be easily handled by the machine or a stray steel pipe that could potentially damage the combine and put it out of service for repair, and then take action accordingly. Accomplishing this accurately and quickly requires additional computing power.
In this fused model, sensors are interconnected across multiple or all applications in the vehicle leading to one ECU. The higher amount of data being processed requires more bandwidth, and that higher bandwidth requires connectors and cables that can handle more speed as well as an Ethernet network that can handle up to 1 Gbit per second of data to transmit information reliably.
The transition to these types of technologies and automated functions brings a whole new challenge for engineers to design vehicles that can perform reliably and stand the test of time even in the harshest environments.
New connector technologies
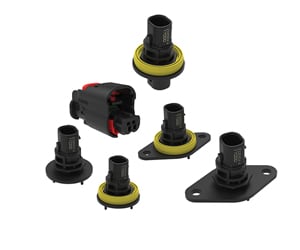
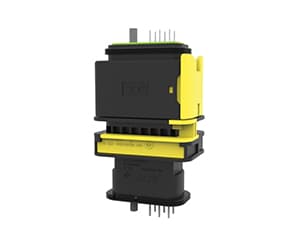
As industrial and commercial vehicle designers look to upgrade the connectivity systems and networks in their vehicles, many high-speed data applications can be designed using connector technology that has been developed over the past few years for use in the automotive industry. However, the environments and challenges that commercial vehicles face are often much harsher in comparison to what cars and light-duty trucks may see. For applications where dust, dirt, moisture, extreme temperatures, and high-vibration are common, our new connectors, such as sealed enetSEAL+ and Heavy Duty Sealed Connector Series with MATEnet inserts can be used. enetSEAL+ connectors can be used for applications requiring up to 100 MB per second of data connectivity, while the Heavy Duty Sealed Connector Series with MATEnet inserts can be used to transfer up to 1 gigabit per second.
enetSEAL+ connectors
- Optimal, high-quality design helps reduce manufacturing and service costs.
- Multi-contact point technology for higher reliability.
- Built-in secondary locking feature is designed to secure contact retention.
- Modular application possible with two codings and multiple panel thicknesses.
- OEMs can use existing harness maker supply chain.
Benefits of Heavy Duty Sealed Connector Series with MATEnet Inserts include:
- Optimized to improve long-term use reliability, reduce manufacturing and service costs.
- Connection secured with the built-in secondary locking feature for contact retention.
- Clear handling, the low mating force with reliable slide locking mechanism delivered in pre-locked position.
- Designed with the modular application in mind for wire-to-wire and wire-to-board allowing several mounting options: inline, sealed flange, and PCB mount.
Applications for our new connectors
Both solutions adapt to virtually any harsh environment application including: radar, lidar, cameras, telematics units, onboard diagnostics, head-up displays, instrument clusters, infotainment applications and Ethernet architecture.
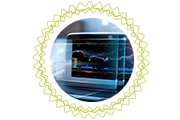
INFOTAINMENT
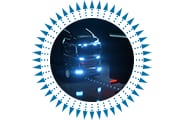
SAFETY
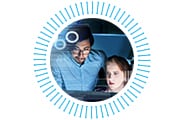
NETWORKS
Staying competitive
To stay competitive in the market and ahead of automation trends and functionality that enable safety, productivity and sustainability, designers and manufacturers must incorporate Ethernet in all their latest designs to be able to handle the increased data connectivity requirements. The best way to do this is to consult early on with engineering experts, like those at TE, who can advise on the topology and technology needed to design and manufacture the innovative components that enable increased sensing and computing power while maintaining signal integrity in harsh conditions.
Originally published in Elektronik journal “Special edition electromechanics”
To Learn More About our Solutions for Connected Vehicles
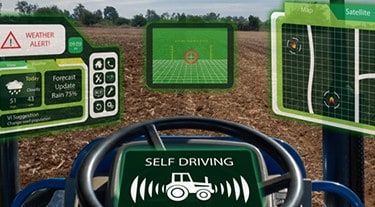
Autonomous Driving
Ethernet Solutions
Learn more about the connectivity requirements to enable commercial and industrial vehicles autonomous driving.
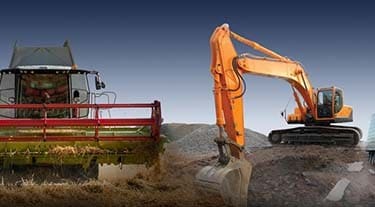
Data Connectivity
Heavy-Duty Vehicles Solutions
Discover why design engineers must consider incorporating Ethernet systems in their industrial and commercial vehicles and machinery to meet future customers' needs.
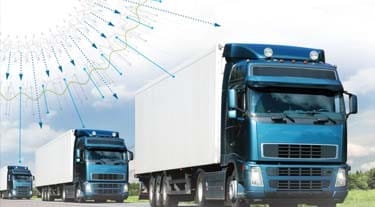
Ethernet Connectivity
Heavy-Duty Vehicles Requirements
Discover the considerations we took to design our Ethernet connectors for heavy-duty vehicles.