TE's DEUTSCH connectors are engineered for durable connections in high-vibration technologies.
Get the right part fast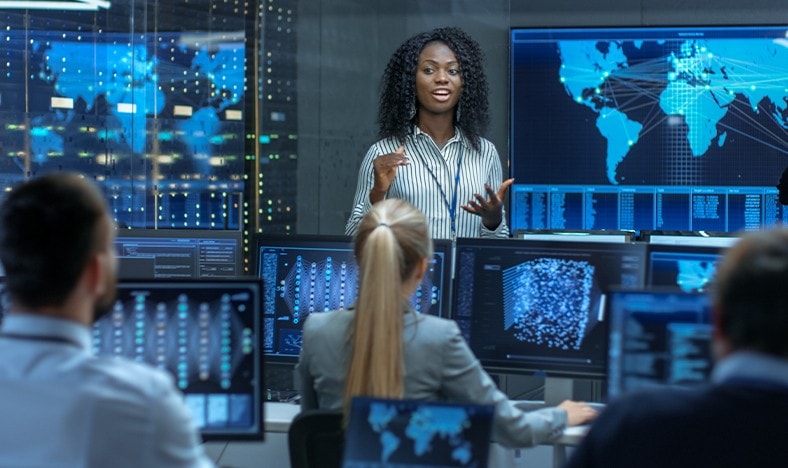
With the rise of generative artificial intelligence (AI), data centers have become an increasingly critical part of the world’s technological infrastructure — and a growing consumer of electricity. Even small-scale improvements involving the types of cables, connectors, and heat dissipation equipment used can have a huge impact on the amount of energy data connectivity systems use, helping increase data center sustainability.
Move data more efficiently to support AI technologiesEmpowering Engineers to Innovate
TE Connectivity helps engineers design and build the technologies transforming how people live, work, and connect As a go-to engineering partner for innovation leaders and technology entrepreneurs, we work on solving tomorrow's toughest technology challenges today. Our global team of regionally located experts – which includes electrical and mechanical engineers – develops and manufactures connectivity solutions enabling technological innovation for a safer, sustainable, productive, and connected world. Our broad portfolio of electrical parts and electronic components including different types of sensors are optimally engineered to reliably connect, protect, and optimize the flow of data, power, and signal – in electric vehicles and aircraft, in digital factories and smart homes, and in life-saving medical devices, efficient utility networks, and the global communications infrastructure, from IOT devices to AI systems. As a trusted electronics manufacturer with 80 years of experience in developing innovative and reliable solutions for industry applications and technological architectures, we work closely with customers to address their reliability, safety, and sustainability challenges.
Meet TE Experts at Events Worldwide
Find Us at Shows Near YouQuick access to top-searched products
- RJ45 Connectors
- USB Connectors
- AMP Connectors
- MQS Connectors
- DEUTSCH Connectors
- FAKRA Connection System
- FASTON Terminals
- MATE-N-LOK Connectors
- M12 Connectors
- Heavy Duty Sealed Connectors
- DEUTSCH DT Connectors
- Relays - Auto, Power, Signal
- RF Connectors - BNC & SMA
- Ring & Spade Terminals
- AMPMODU Connectors
Featured Tech Explainers
Our Approach to Business Innovation & Inclusion
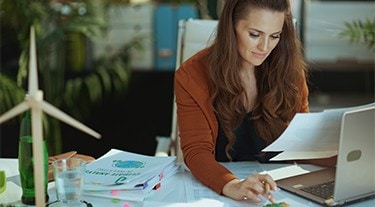
Performance Sustainability
Our commitment to sustainability includes helping our partners innovate sustainably.
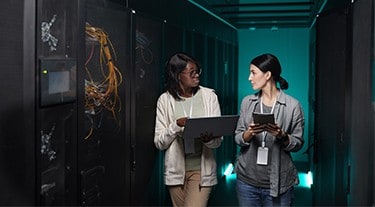
Supplier Diversity
Learn about our program for strategically empowering diversity-owned suppliers.

Industrial Tech Index
Our global survey reveals innovation challenges and opportunities for success.