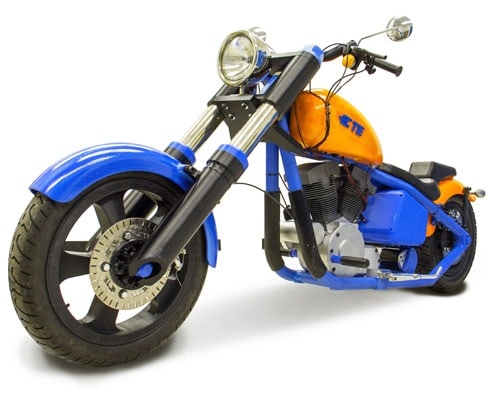
Inventing the Future
In 2014, we used this additive manufacturing process to build the world's first functional, 3D-printed motorcycle. Read the story behind this effort.
At TE, our engineers are continuously working on solutions for making more complex, robust products for real-world challenges. With 3D printing, engineers start by programing a computer with the digital pattern for a product, which dictates how strands of plastic will print together in layers. As these layers print and overlap, they fuse together to form a single part. Today, engineers use this technology to print everything from pizzas to chocolate bars, dresses to musical instruments.
FUN FACTS:
TE's 3D-Printed Motorcycle
10-15
miles per hour (MPH)
8
feet long
250
pounds
Making TE's 3D-Printed Motorcycle
In 2014, we used 3D printing to make the world's first 3D-printed motorcycle, as recognized by the Guinness World Records.
“Additive manufacturing is the ability to take and create something by putting materials together,” explained Chuck Fry, a principal electrical engineer on our Additive Manufacturing Team.
Additive manufacturing goes a step further than 3D printing because it allows engineers to add things as they go along in order to customize the final product.
“For example, the headlight was 3D printed and then it was finished, and then we added copper and then nickel plating on top of it,” Fry said. “Everything was done in an additive fashion instead of the standard methods of manufacturing. In additive manufacturing, you add things to it rather than subtract.”
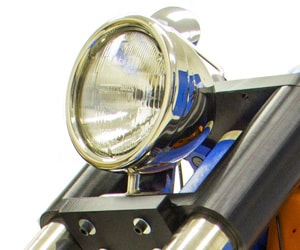
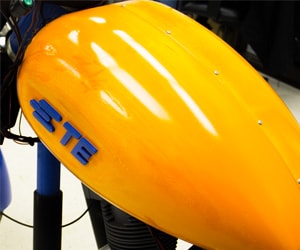
The motorcycle is a custom hardtail design and features a frame, wheel bearings, handlebars and seat all printed in plastic. It is 8 feet long, weighs 250 pounds, and can support 181kg, or two adult riders. The motor produces 1 horsepower, allowing it to travel at 10-15 mph for several minutes.
TE chose to do a custom hardtail, rather than starting with designs based on common models because it allowed engineers to have more freedom.
“Starting with a custom design allowed us to display what additive manufacturing is all about,” Fry said. “And that’s the ability to make custom features, custom designs. That type of customization is something that is easy in additive manufacturing and difficult in regular manufacturing.
With this exciting advancement, TE has demonstrated the potential for 3D printing as a viable method to produce real-world products.
“We decided to do this motorcycle because we wanted to…demonstrate the capabilities of additive manufacturing and 3D printing,” Fry said. “We needed people to see what it was capable of. It can do things that can’t be done otherwise.
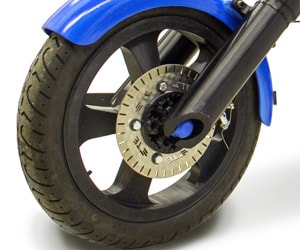