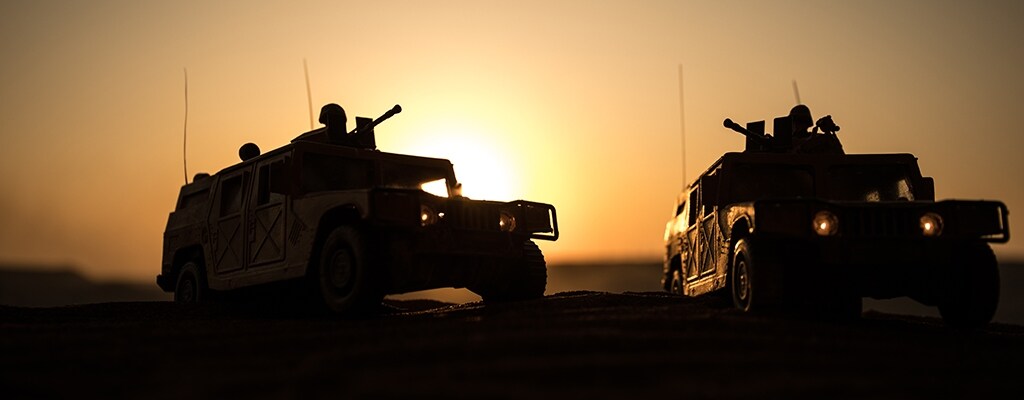
Product Insight
Special Solutions for Unique Challenges
While most of customers purchase a standard MIL-DTL-38999 connector, about 30% require a modified 38999 solution, known as a 38999 special. Understanding the different types of 38999 specials (product line extensions, other product derivatives) will help you to quickly choose the right solution.
D38999 specials are available in several options, but two types standout. The first type is aluminum nickel bronze MIL-DTL-38999 connector. The aluminum nickel bronze special is popular in aerospace and defense applications, such as military ground vehicles and some shipboard applications. Unlike conventional 38999s, which are manufactured in aluminum with various plating options and include a plastic composite material and stainless-steel elements to resist high temperatures, the aluminum nickel bronze 38999 specials are made of highly corrosion-resistant materials that are equal to, if not better than, stainless steel, meaning that these are engineered to provide significantly better anti-corrosion protection than aluminum.
The second type is the hybrid 38999 series 1.5, an option that has evolved over the years. There is no such specification for 38999 series 1.5, but it is a nickname of a commercial 38999 connector family that uses the scoop-proof coupling interface lengths of 38999 series I, and the diameters and mounting sizes of 38999 series II. DEUTSCH 38999 connectors Series I, III, and IV are standard connectors.
Our D38999s are built for reliability in technology that must operate without unexpected failure. All TE 38999 product derivatives are designed to mil-spec standards and validated through TE-controlled processes and field-proven reliability from years in use. These products are often used as commercial options, but they are still used in harsh environments.
Our D38999s are built for reliability in technology that must operate without unexpected failure.
Product Line Extensions
This group of 38999 specials is rapidly evolving at TE. Unlike the first group of 38999 specials, these product derivatives are not part of a product line. These connectors offer several modifications to the standard product and are designed to help engineers resolve unique connection challenges. For example, one of the newest 38999 specials is a high vibration plug connector that is rated higher than standard qualified D38999/26 plug connectors.
This group of 38999 connectors are crucial when trying to design a system that requires fitting many components – microprocessors, diodes, resistors, thermal management system, and capacitors – into a single box. In such cases, it is not uncommon for engineers to simply run out of the space needed for the input/output connector. And what they find is that the standard 38999 connector will not solve the issue. What they need is an application-specific connector, one that improves upon what exists, allows, or meets the 38999 standard connector.
When building a box, the standard approach is to mount receptacles onto the box. We typically supply crimp contacts with our D38999s. This enables installers to terminate the wires to the contacts, to the back of the connector and onto the back of the box, where there is usually a plug with a cable harness attached to it. The cable connects to the core application – aircraft, ground vehicle, radar system, or others.
For these types of applications, it is often critical to build smaller and lighter boxes to save on size and weight, which enables the aircraft to save on fuel and fly at increasingly faster speeds or soldiers to carry advanced technology over long distances. To enable this, instead of using the crimp contacts that come with our standard D38999 connectors, engineers remove connectors extended from the back of the box and solder the printed circuit board directly on the back of the connector inside the box. Our portfolio of D38999 specials includes three types of product derivatives: PC Tail connectors, 38999 Mounting Flange, and Integral Rear Banded Platform.
Circular Connectors beyond Mil-Spec limits to meet the widest range of harsh environments for signal, power, and optical needs.
D38999 Product Derivatives
PC Tail Connector
Our PC Tail Connector is result of customer requests for D38999 solutions that can be used in lighter and smaller boxes. Our PC Tail Connector, which became popular about 25 years ago, features a design that evolves every year as more customers adapt the PC Tail contacts in 38999 connectors instead of using the crimps.
38999 Mounting Flange
Some customers prefer a versatile 38999 connector. For them, we offer various mounting flange options, which can include moving the mounting flange forward and backward, creating a triangular mounting flange, adding threads to the mounting holes, or making a bigger or smaller mounting flange than the standard size. Since customer demand depends on the space constraint inside their box, our products are available with simple modifications to the shells/outer housings.
Integral Rear Banded Platform
At the back end of the standard D38999 connector are accessory threads. Typically, engineers wire contacts, install them in the back of the connector, and then put on the backshell, which acts like a rear adapter. There are hundreds of different types of backshells to strain relief the wire off the back of the connector, Installers can also ground the braid of the jacket and cable onto the back of the backshell, and then dress it with a shrink boot.
We developed this integral rear banded platform to satisfy industry demand for a lighter, smaller 38999. This solution replaces the rear threads on the back of the connector to provide a rear end of the connector that allows the customer to terminate the braid of the cable directly on the back of the connector. For example, instead of needing to buy a backshell and thread it onto the standard connector, installers can dress the braid of the cable, which allows them to ground the cable through the connector, resulting in optimal performance in applications. By attaching the cable directly to the back end of the connector, the installer can get a little better performance because the cable is touching the connector with the grounding pack. This eliminates some of the weight from the backshell, the cost of the backshell, and the extra time it takes to harness the backshell.
Full Custom Connectors
When the engineering challenge is unique, TE engineers can develop a fully custom 38999 connector to address a range of requirements. This includes designs new to the market and unique to the application yet fully using mil-spec standards in a 38999 connector that requires more than a simple or mid-level change. Customer requests for fully custom 38999 connectors are infrequent, mostly because of the longevity of this product in the marketplace, and because most previous iterations of customs have been adopted into product line derivatives.
One example of a fully custom 38999 connector is one that was developed 20 years ago. It is primarily used in applications to launch munitions from aircrafts. This connector uses the mil-spec principles of standard 38999 connectors – as well as other circular connectors – to deliver high reliability when used in harsh environments.
Because a fully customized connector does take time to develop and manufacture, customers typically engage with us early on in their design process, giving us enough time to meet their product requirements. Development timelines can range from four months to a few years, depending on the complexity of the designing and the machining required to produce it.
Partners in Connectivity
For more than 25 years, our engineers have developed D38999 specials that have become de facto product lines. Every day, we work closely with customers to innovate D38999 specials and improve the technology. Our dedicated integrated products team specifically supports these projects, and we allocate machinery and infrastructure to create 38999 specials to meet customers requirements.