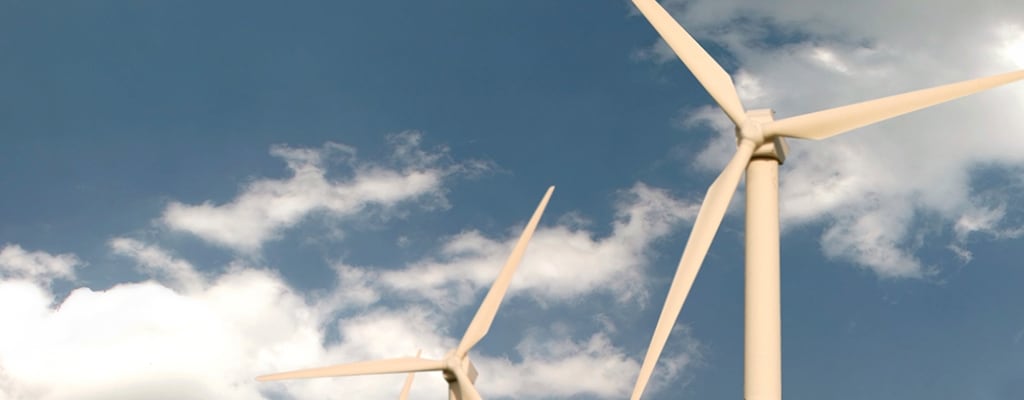
White Paper
Connectivity for reliable wind power
The complex structure of a wind turbine requires an array of cable solutions for various functional areas. By: Eric F. Freid, Industry Sales Manager, Automation & Control.
As wind power hits its stride as a mainstream technology for providing affordable green energy, manufacturers, installers, and operators all look to lower installation and operating costs while improving efficiency. Faster installs, higher reliability, and easier maintenance all play a role in the economics of wind power – getting a turbine online quickly and having it running reliably without interruption are critical concerns.
As the wind power industry matures, standardization is also occurring. Standards organizations are beginning to evolve standards specific to wind turbines. At present and in the past, most designers are turning to existing readily available technology such as Industrial Ethernet, or to widely proven approaches such as modular industrial connectors.
Plug-and-Play Lowers Costs and Increases Availability
The complex structure of a wind turbine requires an expansive array of cable solutions for various functional areas. These solutions include high-voltage cables for delivering the energy produced to the grid, also fiber optic and Ethernet cables for monitoring and SCADA (Supervisory Control and Data Acquisition), control cables for yaw and pitch, and power cables for motors and drives. To speed and simplify the installation and maintenance of turbine systems, designers are turning to more “plug-and-play” solutions. The goal is to achieve “plug-and-play” convenience in installing cable solutions to speed overall installation and maintenance of the wind-power systems.
Typical Requirements
Connectors Used in Wind Turbines
Wide temperature range: -40°C to +125°C |
Vibration and shock resistance |
Shielded or unshielded |
Fluid resistance |
Sealing capability up to IP67 |
Keying capability |
Fast connection/disconnection with positive seating |
Modularity: Ability to accommodate signal, power, and fiber optics as needed |
Single Interface for Multiple Connectors
In simplifying the overall cable solutions within the wind turbine, manufacturers are turning to well-established industrial connector technology. This technology combines three features: robust mechanical construction with sturdy metal or composite housing, modular inserts for flexibility in the types of contacts and cables accepted, and the ability to provide shielding and sealing as required.
The ability to mix and match cables – motor supply cables for motors and drives, twisted-pair cable for control, instrumentation cable for monitoring, and so forth – allows a single interface to replace multiple connectors.
The image below shows TE's heavy duty modular connectors, which typify a robust, industrial-strength connector. Up to six single or three double modules can be used in the frame. In many wind power applications, the heavy duty modular connector reduces the number of interfaces required by allowing users to configure the exact interface required for an application within a single connector.
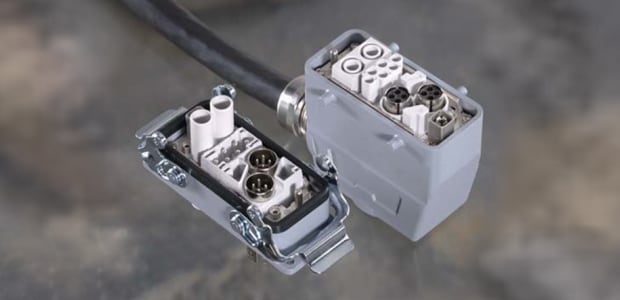
Interface Modules
- High-voltage contacts, up to 3000 V nominal
- High-current contacts, up to 700 A
- High density signal contacts, with up to 25 contacts in a single module
- Coaxial contacts
- RJ-45 modular plugs
- USB
- IEEE 1394 (FireWire)
- Quadrax contacts, supporting 1 GHz operation
- Subminiature-D interface
Availability to the Grid
The modularity of industrial connectors gives designers greater flexibility in configuring an interface and cable assembly. Through arrangement of inserts and through keying, cable assemblies can be “customized” for a specific application. The connector to the yaw motor controls is different from the connector to the pitch motor controls, making it impossible to connect the cable to the wrong subsystem.
To make identification easier, housings can be color-coded. The ability to color-code connectors to indicate function, circuits, or other application parameters makes visual identification simpler and virtually foolproof. Personal computer and audio-visual systems, for example, have long used a color-coding method to identify mouse, keyboard, video, and audio ports. Bringing color-coding to wind power applications offers the same convenience of installation thus improving the time for a system to be available to the grid.
Modular industrial connectors can also simplify the supply chain through standardization of a single connector family to accommodate a wide range of needs. While each cable application may use a differently configured connector, some modules can be shared across multiple applications. This ability to share reduces the number of parts that must be stocked and consolidates the number of different procedures that must be mastered in building cable assemblies. A single modular connector family can yield thousands of possible combinations. You can rely on the suppliers of such connectors for advice in configuring the parts for your specific applications. Another example is that multiple sources of a subsystem can now be specified since each could have the appropriate mating connector as it arrives to its final assembly point.
Advantages of Modularity
Modularity is also becoming commonplace in the tower. Many manufacturers today wire each vertical section in the tower factory or in the field. With a plug-and-play solution, as each section is raised and put in place, cables are simply plugged in from one section to the next eliminating the time-consuming task of using mechanical bolt type connectors which require multi-steps in the assembly process in the field.
A recent example of the advantages of modularity is seen in slip ring assemblies used for transferring data and power between the hub and nacelle. Most designs required time-consuming removal of numerous cable assemblies when rings needed repaired or replaced. The procedure could easily involve multiple days of downtime. A more modular design for slip ring assemblies permits the cable to be disconnected in minutes for faster removal of the slip rings. Today’s slip rings can be replaced in hours rather than days.
Critical Components
-
Industrial Ethernet
Industrial Ethernet is emerging as one of the predominant protocols for monitoring and controlling wind power systems. Sealed connectors, such as the IP67 connector (shown below in Figure A), offer rugged, dependable service. For protected connections inside cabinets, where sealing may not be required, standard Category 5e or 6 Ethernet cables can be used. Because many drives and motors have higher levels of intelligence built in, another variation is a hybrid connector (Figure B) offering up to eight power contacts and an Ethernet interface in a compact package using a screw lock coupling mechanism for vibration resistance. This allows a single connector to be used for signals and power.
-
Fiber for the Backbone
Optical fiber cables are the favored choice for communicating from the individual wind turbine to the wind farm central monitoring controls and within the wind turbine system itself because of fiber’s well-known high bandwidth, long transmission distances, and noise immunity. The choice of connector depends heavily on application parameters. Fiber optic connectors are also available in sealed industrial interfaces similar to those used with Industrial Ethernet copper connectors.
-
Medium-Voltage Connectors
Distributing the power generated by the turbine into the collector field and on to the transmission substation present different issues. Within the turbine, generated power is in the 600-V range to the base of the tower, where it is upconverted to 22 kV to 34.5 kV (depending on the country). Seven to ten turbines are daisy-chained serially and multiple chains deliver the up-converted voltage to the collector network’s headend or the transmission substation. At the substation, the voltage is again stepped up to several hundred thousand volts for transmission and distribution.
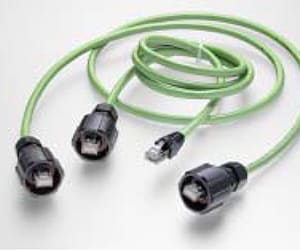
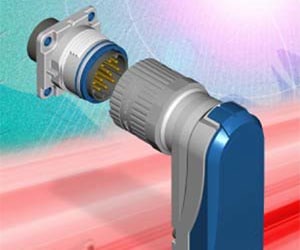
The lower 600-V levels within the turbine allow any number of industry-standard technologies to be used. Multiple cables – perhaps eight to ten – deliver this low voltage to the step-up transformer at the base of the station. From there, connectors more typically come from the energy industry than the industrial or communication industries. Compression or screw terminations in splices are common. An important consideration is the need for grounding, surge protection, arcing, and similar phenomena that separates medium-voltage power distribution from its signal and low-voltage counterparts.
Most power-distribution connections are either in-line splices or T connections (Figure C) for tapping. Since the collector network is underground, reliability is paramount. Unlike the nacelle, with its mechanical components subject to wear and sophisticated electronics, the collector network does not need to be concerned with fast, easy maintenance to the same degree as the turbine itself. Installed properly, the collector network should work for years. A failure in the collector network can take many generators offline. Similarly, a failure in the homerun feed from collector network to substation could disrupt the entire wind farm.
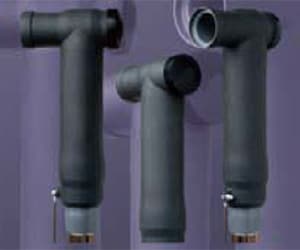
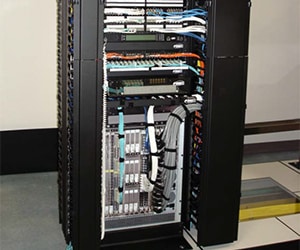
Networking the Control Center
Communication, monitoring, and control cables for the various turbines are consolidated at the control center for control of the turbines, for interfacing with the grid, and for upstream communication over the Internet. Networking the individual turbines into an integrated network presents connector and cabling choices similar to any other network. A structured cabling system allows the network to be conveniently managed and accommodate moves, additions, and changes to the infrastructure connecting the network switches and routers and the control system’s computers. Rack-mounted patch panels and fiber enclosures provide a means to organize and interconnect cables by function or circuit.
The main key here is, of course, confirmation that connectors and cables are matched to the speeds of the network. While Category 5e twisted pairs are the prevailing type used with Industrial Ethernet for data rates up to 1 Gb/s, Category 6 and 6A, capable of support 10-Gb/s networking, may be a better choice even if the higher data rates are used. Category 6 cables give extra performance headroom to provide a nice cushion for maintaining signal integrity. Since the control center is a controlled environment, issues like sealing or wide temperature ranges are not a concern. Standard structured cabling components generally work fine.
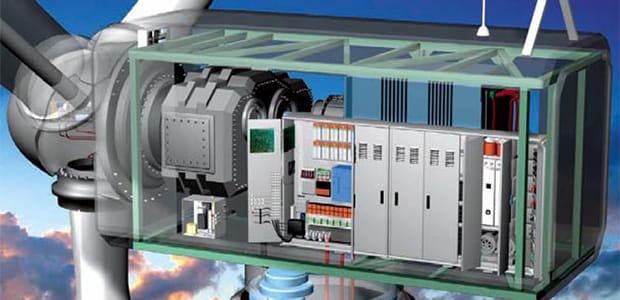
Wind Power “Availability” is the Key to Connector Choice
The choice of connector is not about cost. It is about uptime and the online availability of the wind turbine. Manufacturers of wind turbines now look beyond the acquisition costs of a component to the life-cycle costs. For instance, a properly configured cable assembly can significantly reduce the time it takes to install a wind turbine. It can also speed repairs and maintenance. The cost of the connector or a cable solution is generally insignificant in comparison to the cost of having a wind turbine offline.