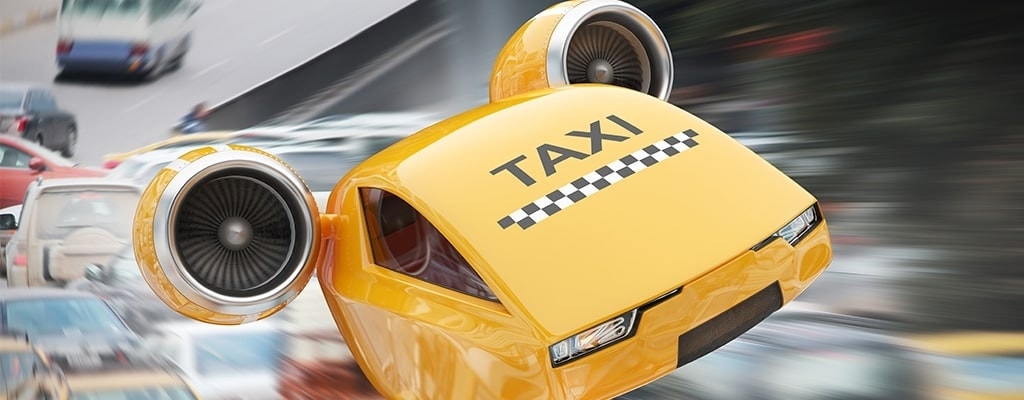
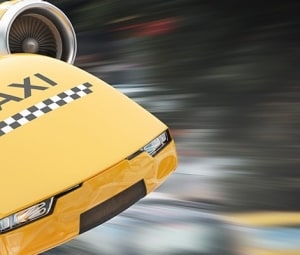
Yesterday’s dreams of electric-powered air taxis and flying cars are now turning into real Urban Air Mobility (UAM) projects.
The future of flight is cleaner, smaller and smarter. With populations booming in cities around the world—and current infrastructure struggling to keep up—engineers look to urban air mobility to rise above the gridlock. But getting there won’t be easy. Designers first need to overcome the inherent challenges of electric-powered vertical range, takeoff and landing.
TE Connectivity (TE) is leveraging decades of leadership in automotive, aerospace, rail and defense to answer the toughest questions facing urban air mobility. See how we’re helping today’s pioneers get off the ground by cutting weight, solving electrical challenges and more.
Q&A with Russ Graves, Global Business Development Manager
Q: Why do you think flying cars, taxis and other urban air mobility (UAM) projects will eventually become a reality?
A: The future of this market is just so logical. When you look at the megatrends that have shaped the modern age over the past century, you can’t help but see how increased personal mobility is the next step. Increasing urbanization; the rise of mega cities like Shanghai and Tokyo; landscapes at capacity; and growing congestion around population centers are key indicators that UAM is coming.
Q: What kinds of challenges do engineers need to consider when designing UAM applications?
A: Because we’re talking about electric power in most prototypes, getting airborne is intricately related to power management and high-power, high-voltage interconnects. These aircraft will use significant amounts of electrical power to achieve takeoff and maintain flight. One factor engineers must consider in UAM applications is how the interconnects fit into the system holistically. Another is how to manage corona discharges, an increased risk in airborne applications. There’s also the potential for arc tracking damage. Selecting proper insulating materials can help to mitigate these issues. Engineers should also consider how to handle high network operating voltages (>3kV DC) and electric propulsion motors, which place higher demands on relays and contacts. Specifying high-voltage relays and contactors helps meet peak load capacity in these applications. Power management is another critical consideration. There are valuable differences between hybrid electromechanical and solid-state power switching technologies. These are just a few of the factors that engineers should evaluate when developing UAM vehicles.
Q: What is TE doing to develop technologies that meet the needs of UAM applications?
A: We are working with industry standards bodies and leading universities to handle the challenges imposed by higher power and voltage levels. We’re also drawing on the full extent of our industry knowledge to bring time-tested solutions from across our portfolio for automotive, aerospace, energy and rail applications. TE’s KILOVAC line of high-voltage relays and contactors can provide the voltage levels needed for UAM projects. For the high temperature environments that will be found in these applications, TE’s Raychem high-performance power feeders and environmental sealing protection products are available. TE’s STRATO-THERM terminals, splices and spare wire caps are also designed for applications up to 1200°F (649°C). TE makes a range of connectors, sensors, cable assemblies and other products that can help engineers working on UAM projects. At the same time, we’re developing new products to help our customers turn their UAM prototypes into market-ready vehicles.
Q: Besides weight savings, why was PEEK polymer the material of choice?
A: In addition to being lighter than metal, we decided to use PEEK as the structure material in the TE P-Clamp because it maintains its strength and integrity when exposed to high temperature and aggressive fluids.
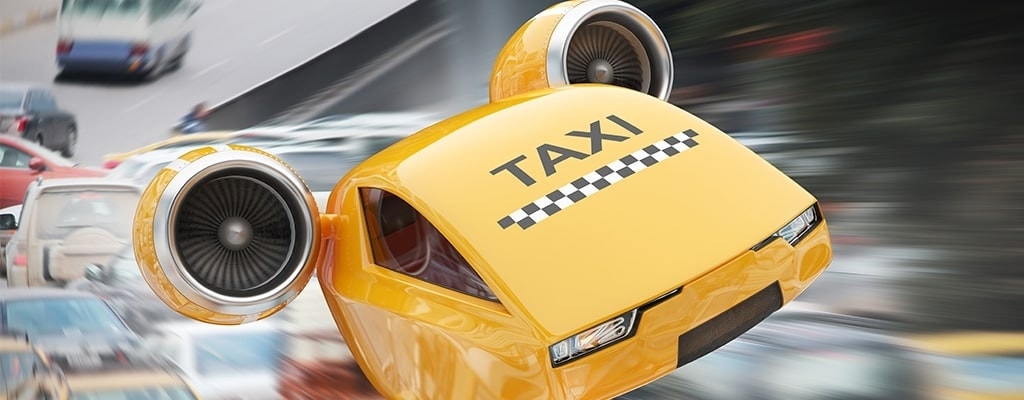
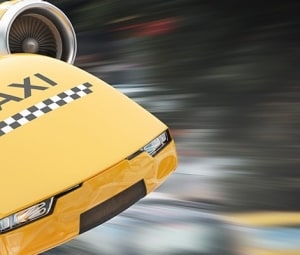
Yesterday’s dreams of electric-powered air taxis and flying cars are now turning into real Urban Air Mobility (UAM) projects.
The future of flight is cleaner, smaller and smarter. With populations booming in cities around the world—and current infrastructure struggling to keep up—engineers look to urban air mobility to rise above the gridlock. But getting there won’t be easy. Designers first need to overcome the inherent challenges of electric-powered vertical range, takeoff and landing.
TE Connectivity (TE) is leveraging decades of leadership in automotive, aerospace, rail and defense to answer the toughest questions facing urban air mobility. See how we’re helping today’s pioneers get off the ground by cutting weight, solving electrical challenges and more.
Q&A with Russ Graves, Global Business Development Manager
Q: Why do you think flying cars, taxis and other urban air mobility (UAM) projects will eventually become a reality?
A: The future of this market is just so logical. When you look at the megatrends that have shaped the modern age over the past century, you can’t help but see how increased personal mobility is the next step. Increasing urbanization; the rise of mega cities like Shanghai and Tokyo; landscapes at capacity; and growing congestion around population centers are key indicators that UAM is coming.
Q: What kinds of challenges do engineers need to consider when designing UAM applications?
A: Because we’re talking about electric power in most prototypes, getting airborne is intricately related to power management and high-power, high-voltage interconnects. These aircraft will use significant amounts of electrical power to achieve takeoff and maintain flight. One factor engineers must consider in UAM applications is how the interconnects fit into the system holistically. Another is how to manage corona discharges, an increased risk in airborne applications. There’s also the potential for arc tracking damage. Selecting proper insulating materials can help to mitigate these issues. Engineers should also consider how to handle high network operating voltages (>3kV DC) and electric propulsion motors, which place higher demands on relays and contacts. Specifying high-voltage relays and contactors helps meet peak load capacity in these applications. Power management is another critical consideration. There are valuable differences between hybrid electromechanical and solid-state power switching technologies. These are just a few of the factors that engineers should evaluate when developing UAM vehicles.
Q: What is TE doing to develop technologies that meet the needs of UAM applications?
A: We are working with industry standards bodies and leading universities to handle the challenges imposed by higher power and voltage levels. We’re also drawing on the full extent of our industry knowledge to bring time-tested solutions from across our portfolio for automotive, aerospace, energy and rail applications. TE’s KILOVAC line of high-voltage relays and contactors can provide the voltage levels needed for UAM projects. For the high temperature environments that will be found in these applications, TE’s Raychem high-performance power feeders and environmental sealing protection products are available. TE’s STRATO-THERM terminals, splices and spare wire caps are also designed for applications up to 1200°F (649°C). TE makes a range of connectors, sensors, cable assemblies and other products that can help engineers working on UAM projects. At the same time, we’re developing new products to help our customers turn their UAM prototypes into market-ready vehicles.
Q: Besides weight savings, why was PEEK polymer the material of choice?
A: In addition to being lighter than metal, we decided to use PEEK as the structure material in the TE P-Clamp because it maintains its strength and integrity when exposed to high temperature and aggressive fluids.