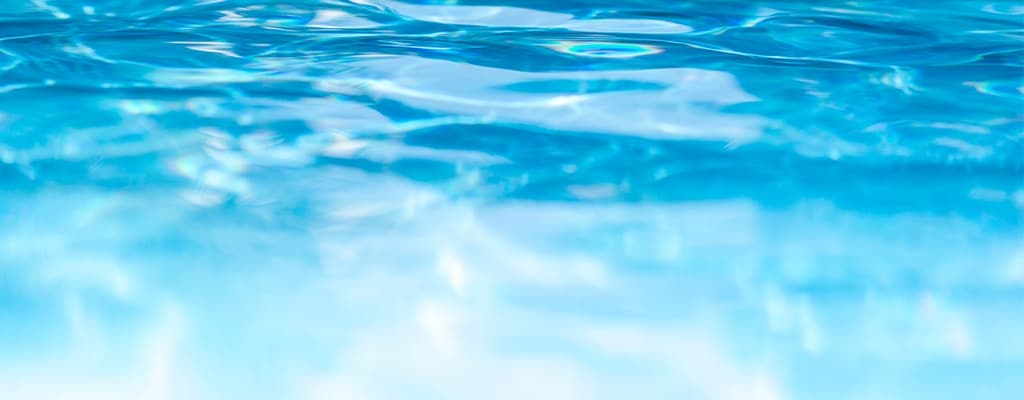
Livre blanc
Capteurs pour environnements corrosifs
Découvrez les progrès réalisés dans la conception des capteurs pour résister à l’exposition aux environnements chimiques corrosifs et hostiles.
Des usines aux trackers de fitness, les capteurs jouent un rôle crucial dans les demandes en constante évolution pour répondre aux attentes de demain. Les appareils grand public et industriels contiennent un nombre croissant de capteurs, poussés par l’utilisation généralisée des technologies sans fil et IoT. Les progrès réalisés dans le domaine des capteurs sont essentiels pour ces marchés : des capteurs ultra-compacts, à faible consommation, de haute précision, digitaux et résistants aux milieux hostiles doivent être conçus pour relever et surmonter ces défis de performance.

Les capteurs de pression sont utilisés dans un large éventail d’applications pour divers marchés tels que l’automobile, l’industrie, le médical et les produits de consommation. Notre monde devient de plus en plus connecté et « intelligent ». Pour ce faire, les capteurs sont désormais utilisés dans des applications et des environnements qui ne sont pas très accueillants pour les capteurs. Nombre de ces applications nécessitent des capteurs conçus pour résister à l’exposition à des produits chimiques corrosifs et hostiles. Ces produits chimiques existent souvent dans le milieu que le capteur essaie de mesurer. Les produits chimiques seront en contact direct avec le capteur lui-même et, pour être fiables et avoir une longue durée de vie, les capteurs modernes doivent être conçus pour résister aux attaques de ces substances. L’utilisation d’un capteur de pression dans une montre de natation en est un bon exemple. Ces montres sont régulièrement exposées à de l’eau contenant du chlore sous forme de gaz dissous (piscine) ou sous forme ionique (eau de mer). Le chlore est un oxydant puissant qui corrode rapidement la plupart des métaux et cause des dommages irréversibles au produit.
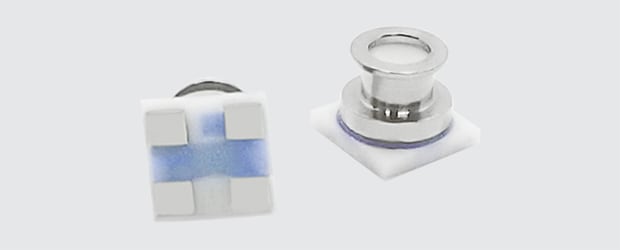

Fonctionnement d’un capteur de pression MEMS
La structure typique d’un capteur de pression piézorésistif est un diaphragme planaire en silicium formé par gravure chimique ou sèche. Les piézorésistances sont placées près du bord de la membrane et dans la plage de fonctionnement linéaire du capteur.
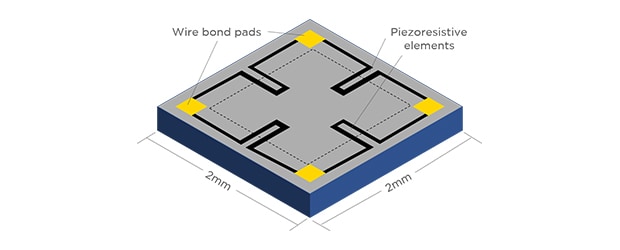
Lorsqu’une pression est appliquée sur l’élément MEMS, celui-ci dévie un peu comme un trampoline. La déviation provoque une déformation des éléments piézorésistifs et ceux-ci changent leur valeur de résistance proportionnellement à la déviation
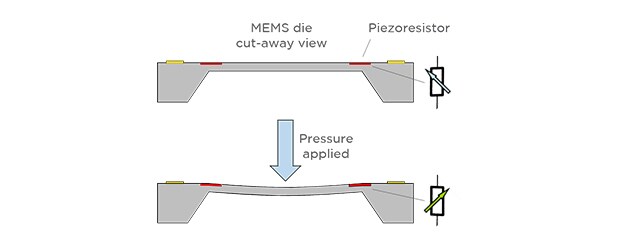
Dans la pratique, on utilise quatre piézorésistances, disposées en pont de Wheatstone de manière à maximiser les niveaux de signal et à assurer un certain degré de rejet en mode commun du bruit indésirable.
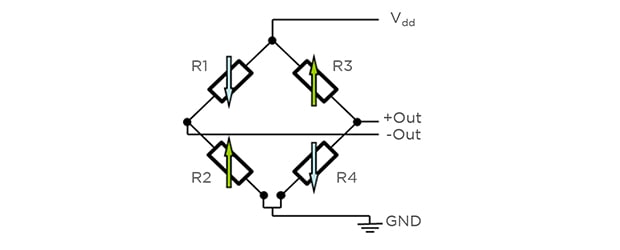
Un moyen de détecter les problèmes avec le capteur consiste à regarder les décalages du signal de sortie sans pression appliquée. Si le fonctionnement est correct, la sortie différentielle doit être de 0 V. Si la sortie n’est pas de 0 V, cela indique qu’il existe un problème avec l’élément de détection. La corrosion causée par des produits chimiques agressifs peut affecter le fonctionnement des éléments piézorésistifs, des interconnexions et des tampons de liaison filaire. La corrosion peut introduire des décalages dans le signal de sortie et des données erronées du capteur. Dans tous les cas, le signal de l’élément de capteur MEMS est connecté à un ASIC CMOS où il est compensé pour la linéarité de la température et d’autres erreurs, avant d’être amplifié et numérisé. Ces données numériques sont ensuite formatées pour être facilement communiquées à un microprocesseur maître via le protocole I2C ou SPI.

Emballage pour la protection
L’emballage et l’isolation environnementale de l’élément de détection MEMS et de l’ASIC CMOS sont très importants pour la fonctionnalité fiable du capteur de pression. Ils assurent la protection de la puce et permettent en même temps la connectivité avec le monde extérieur. Tous les capteurs doivent être physiquement en contact avec le milieu ou le phénomène qu’ils mesurent. De plus, ils doivent être connectés au système électronique qui utilise les données fournies par le capteur.
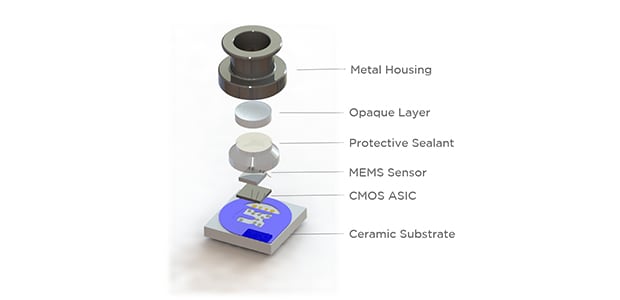
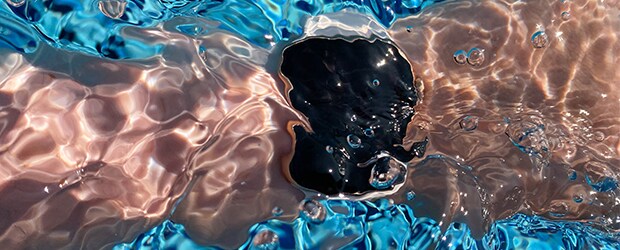

Une technologie unique pour les environnements difficiles
TE Connectivity a développé des capteurs de pression miniaturisés adaptés à l’exposition à des environnements difficiles et corrosifs, y compris des oxydants puissants tels que les halogènes (fluor, chlore, brome, iode). Ces types d’environnements difficiles existent sur les marchés de l’automobile, de la médecine et des appareils connectés personnels.
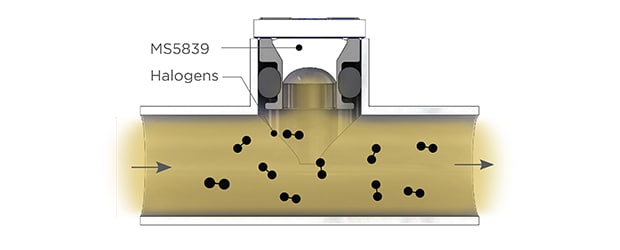
Dans les applications automobiles, certains des polymères organiques utilisés comme « substances ignifuges » sont formulés à l’aide de composés halogènes. Ces matériaux peuvent évacuer les produits chimiques à base d’halogène tels que l’iodométhane (méthane enrichi en iode). Même à des concentrations de quelques ppm, l’iodométhane agit comme un catalyseur sur les caractéristiques intermétalliques des puces MEMS et semi-conductrices, créant ainsi un sérieux problème pour nos clients du secteur automobile.
L’eau chlorée dans les piscines présente un problème similaire et connexe pour les applications portables. Les capteurs de pression de TE sont utilisés comme altimètres pour les montres de sport utilisées par les triathlètes ou les capteurs de profondeur dans les ordinateurs de plongée. Sans un emballage et une protection appropriés des appareils, les capteurs peuvent se corroder et tomber en panne lorsqu’ils sont utilisés dans des piscines ou dans de l’eau de mer, toutes deux riches en chlore dissous ou ionique.

ESSAIS ET VALIDATION
La nouvelle technologie et la nouvelle conception développées par TE Connectivity ont été testées avec l’ensemble des capteurs exposés à l’eau salée, à l’eau chlorée et au gaz diiodométhane. L’exposition au diiodométhane s’est avérée être le test le plus dur. Les figures ci-dessous illustrent la dérive du signal de sortie de l’élément de détection par rapport à l’exposition au diiodométhane et à l’eau chlorée. Les dérives sont considérées comme très limitées. De plus, la dérive en décalage peut principalement s’expliquer par la présence de l’environnement humide plutôt que par le diiodométhane qu’il contient. Un autre essai de durée de vie accéléré, à 85 °C et dans une humidité relative de 85 %, a montré les mêmes dérives dans le décalage et la portée, comme indiqué à côté des résultats pour le diiodométhane.

TEST DU CHLORE
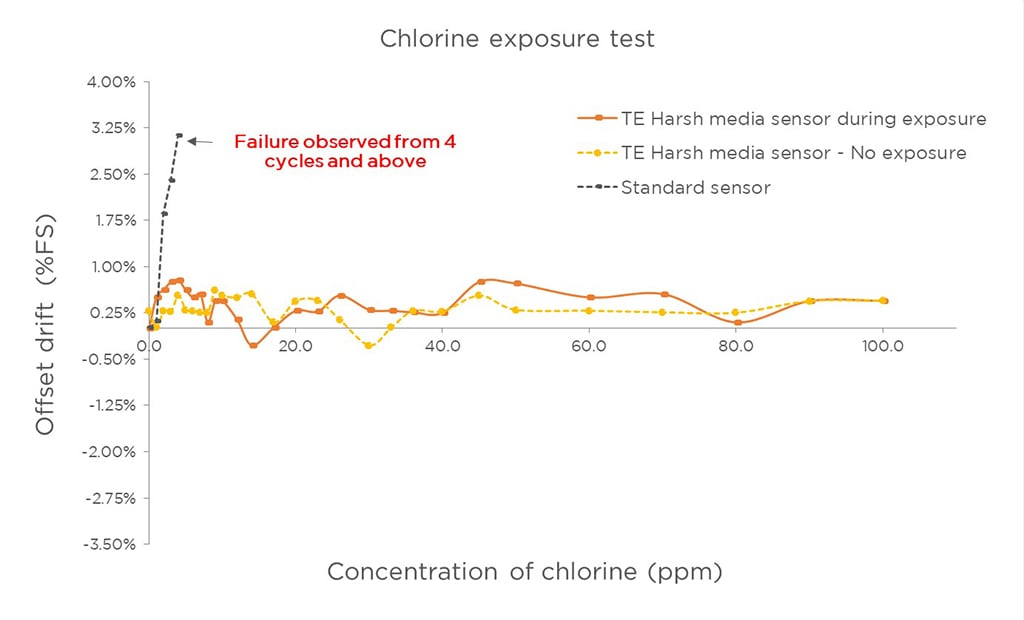
FIGURE 8. Résultats des tests de chlore

TEST DU DIIODOMÉTHANE
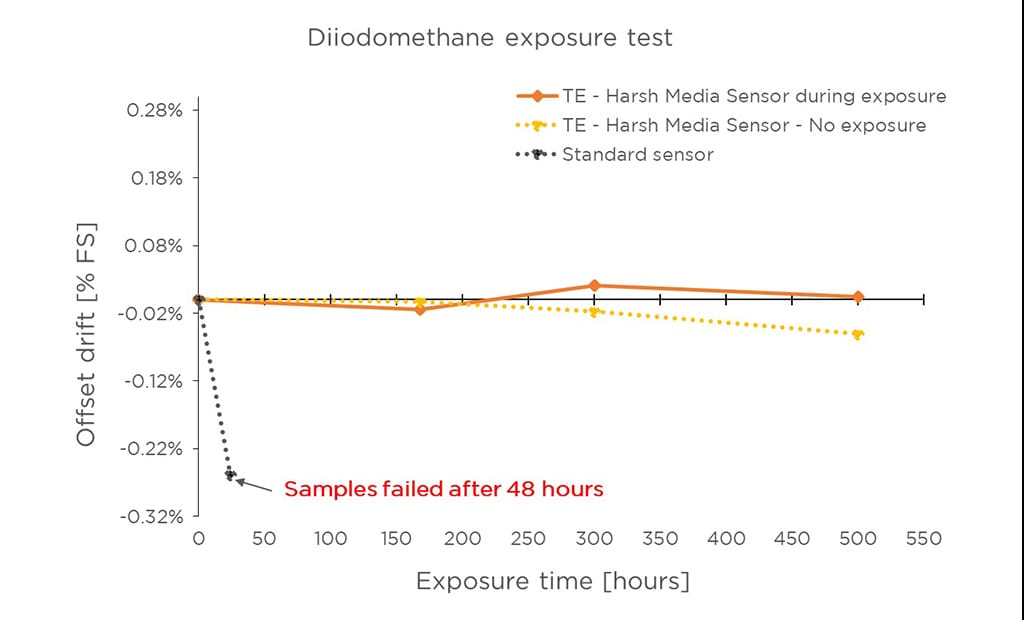
FIGURE 9. Résultats des tests du diiodométhane

Récapitulatif
La nouvelle conception du boîtier et les nouvelles procédures d’assemblage de TE Connectivity permettent d’obtenir un capteur présentant une résistance accrue aux produits chimiques et aux atmosphères corrosives. Les clients sont ainsi assurés que les capteurs TE résisteront mieux aux pannes ou aux dysfonctionnements dans les applications en milieu corrosif.

Les performances réelles peuvent varier selon l’application. Bien que les résultats des tests présentés dans ce document montrent une résistance accrue à la corrosion, le client doit tester et qualifier le capteur de manière appropriée pour ses applications spécifiques.

Microfused est une marque déposée.