Les ingénieurs de TE évoquent l’équation thermique côté véhicule en relation avec la charge rapide CC des véhicules électriques.
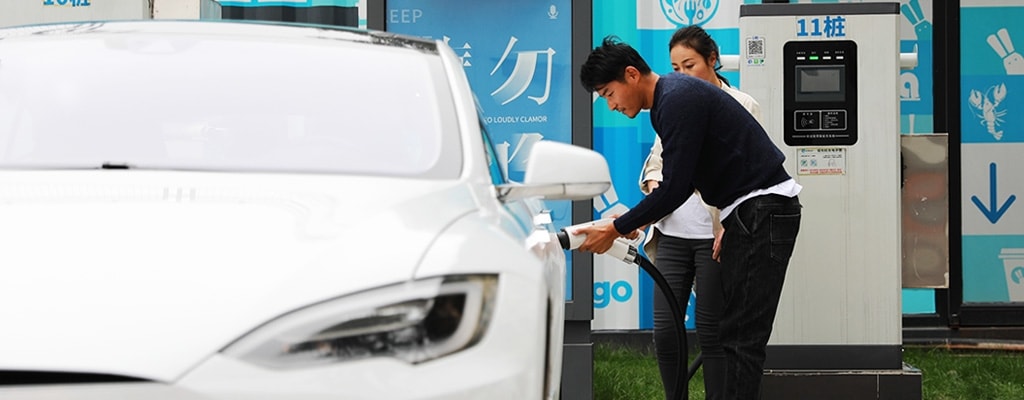
Innovation dans la mobilité électrique
La nouvelle génération de technologies des véhicules électriques
Les ingénieurs en conception de véhicules électriques s’appuient sur nos technologies d’interconnexion, de commutation et de détection pour améliorer les réseaux de connectivité de données basse tension et les systèmes de transmission haute tension. Pour atteindre cet objectif, ces technologies doivent fonctionner en parallèle, au sein d’architectures de véhicule centralisées de plus en plus intégrées.
On dit souvent que la nouvelle ère de la mobilité, qui offrira des moyens de transport plus sûrs, plus écologiques et plus connectés, sera marquée par des véhicules fonctionnant avec deux types de carburant : l’électricité et les données. Cependant, alors que la sécurité, le confort et la recherche d’une connectivité omniprésente sont à l’origine d’un nombre toujours croissant d’applications basées sur le cloud/les capteurs et dépendantes des données dans les véhicules, de nombreux consommateurs sont encore quelque peu réticents à l’idée d’adopter pleinement la technologie de la mobilité électrique malgré leurs préoccupations environnementales.
… « tous les composants conducteurs électriques […] du système électrique global, reliant la borne de recharge à la batterie du véhicule, doivent être conçus et dimensionnés mécaniquement, électriquement et thermiquement. »
Préoccupations des conducteurs
Les principales préoccupations de nombreux conducteurs potentiels de véhicules électriques (VE) sont l’autonomie et la recharge, notamment le temps de charge et la disponibilité de bornes de recharge. À cet égard, la connectivité et les composants des connecteurs, du port de charge au moteur électrique, en passant par la batterie du véhicule électrique, sont essentiels pour atteindre un niveau d’autonomie qui rassurerait les consommateurs grâce à une charge rapide à haute puissance à la fois sûre et fiable.
Aujourd’hui, charger un véhicule sur une borne de recharge rapide en courant continu (CC), que l’on trouve généralement dans les stations-service des réseaux autoroutiers, peut prendre jusqu’à une heure (en fonction de la puissance de charge et de la capacité de la batterie), pour récupérer environ 300 km d’autonomie. L’objectif de l’industrie est de réduire ce délai à environ 10 minutes, soit le temps moyen d’un arrêt pour faire le plein de carburant d’un véhicule à moteur à combustion interne (ICE).
Défis de connectivité
Cette charge haute puissance (HPC) peut représenter 350 kW de puissance de charge CC à des courants allant jusqu’à 500 A, ce qui représente l’état de charge le plus élevé pour l’ensemble du système électrique d’un véhicule électrique. Même une accélération brusque, lorsque le conducteur a besoin de beaucoup de puissance, ne se traduit pas par la même amplitude de courant moyen.
Ce niveau de courant continu provoque des pertes de chaleur importantes en raison de la résistance électrique inhérente à tous les composants (connecteurs, câbles) du groupe motopropulseur du véhicule électrique. Et il est encore plus élevé lorsque le véhicule est à l’arrêt et qu’aucun refroidissement convectif naturel n’a lieu.
La dissipation thermique passive ou active, ou un moyen de faciliter la diminution contrôlée du courant de recharge, sont donc essentiels lors de la conception et du dimensionnement de tous les composants conducteurs électriques pour éviter la surcharge/surchauffe. Cela signifie que le système électrique global, reliant la borne de recharge à la batterie du véhicule, doit être conçu et dimensionné mécaniquement, électriquement et thermiquement.
L’une des principales difficultés rencontrées réside dans le fait que plus le courant est élevé, plus la section de câble requise pour transmettre l’énergie au même niveau de tension sans surchauffe est grande. À l’intérieur du véhicule, c’est avant tout une question de poids et d’espace disponible.
Par exemple, il existe une différence considérable, en termes de coût, de poids et de volume, entre l’utilisation d’un conducteur de 50 mm² de section et celle d’un conducteur de 95 mm² de section entre le port de charge et la batterie. Pour que la proposition de HPC soit réaliste, il convient d’éviter de surdimensionner le câble et tous les autres composants électriques.
À ce jour, la conception des composants électriques n’a pas vraiment reflété l’évolution dynamique des profils de charge actuels entre les pics et les creux de la conduite ou les exigences en matière de HPC.
Les normes existantes sont basées sur des points de charge statiques utilisés à l’origine pour la conception de relais et de fusibles/interrupteurs à fusibles et déterminés par des méthodes statistiques reflétant leur fréquence et leur importance. Cela se traduit par des valeurs de charge en courant représentant des conditions statiques, ainsi qu’une conception correspondante des composants d’interconnexion électrique qui ne reflète pas la réalité, et qui inclut souvent des marges de sécurité pouvant atteindre 20 %.
Notre offre de solutions de connectivité pour véhicules hybrides et électriques couvre toute la gamme des groupes motopropulseurs électriques. Nous pouvons ainsi fournir une gamme complète de connecteurs, d’embases, de relais, de contacteurs, de faisceaux et de coupe-circuits pour connecter le flux d’énergie en toute sécurité et le protéger. Nos technologies s’appuient sur des décennies d’expérience dans la production, la transmission et la distribution d’énergie haute tension, dans quatre domaines d’application : les modules auxiliaires pour véhicules hybrides, les groupes motopropulseurs pour véhicules hybrides, la connectivité des batteries et les ports de charge.
Connectivité des batteries
Fournir une charge de pointe d’au moins 350 kW de puissance de charge nécessite une approche différente de la conception des composants électriques. Chez TE, nous développons une nouvelle méthodologie qui calcule de façon dynamique l’augmentation de température causée par les composants et la dissipation de chaleur dans le système à tout moment.
Une simulation thermique systémique en conditions quasi réelles permet d’examiner la conception du composant plus tôt dans le processus et de prédire ses performances dans différents modes de fonctionnement tout au long de sa durée de vie. Cela permet de proposer des composants sûrs et durables, ainsi qu’une conception favorisant une plus grande facilité d’utilisation. La simulation thermique basée sur un modèle fournit une base vérifiable pour les futurs profils de charge qui permettent de disposer d’une preuve de sécurité, de fiabilité et de durabilité de tous les composants d’interconnexion, quelle que soit la tension ou l’intensité.
De la même manière que le moteur à combustion interne (ICE) était considéré comme le cœur du véhicule à moteur traditionnel, la batterie est considérée comme le cœur des véhicules électriques et bon nombre des défis de conception sont identiques.
Les véhicules électriques à batterie (BEV) nécessitent des groupes motopropulseurs plus puissants. Cela remet en question l’intégration, dans la couche physique, du réseau de cartes automobiles, parfois en contradiction avec les exigences.
L’ingénierie de la connectivité du groupe motopropulseur pour véhicule électrique de nouvelle génération intègre des ports de charge, des connecteurs haute tension, des relais et des contacteurs ainsi que des connecteurs basse tension miniaturisés pour les systèmes de gestion de batterie des véhicules électriques.
Découvrez les options de connexions haut débit avec des canaux typiques de l’automobile, en tenant compte des facteurs environnementaux, ainsi que des exemples pratiques montrant l’importance des analyses de canaux à l’aide d’outils de simulation.
Le courant entrant et sortant de la batterie doit circuler en toute sécurité, quel que soit le mode de fonctionnement du véhicule. Par conséquent, la connexion de la batterie principale et, dans certains cas, les connexions entre les modules de cellules, doivent pouvoir transporter pendant plusieurs minutes des courants allant jusqu’à 600 A au cours d’un cycle de charge à haute puissance et des niveaux de crête nettement plus élevés lors d’une forte accélération.
Les connexions de module de batterie constituent également la couche physique de protection de la batterie (contre la surchauffe), la gestion de la batterie (gestion de l’état de charge, par exemple) et l’équilibrage des cellules (égalisation de la tension de charge entre des cellules présentant des états de charge différents). Pour garantir le bon déroulement de ces opérations, chaque module de batterie doit être doté de connexions électriques fiables.
Cela nécessite des systèmes de contacts hautement intégrés, qui doivent non seulement être capables de prendre en charge toutes les fonctionnalités tout au long de la durée de vie du véhicule (par exemple, 300 000 km/10 ans), mais aussi être suffisamment robustes pour éviter que les contraintes vibratoires et thermiques affectent les propriétés mécaniques et électriques des contacts. En outre, une protection tactile des contacts est nécessaire pour ne pas exposer les fabricants et le personnel d’entretien aux dangers liés à la haute tension et la haute puissance.
À titre d’exemple, l’un des principaux objectifs de conception du système de connexion de module BCON+ de TE était de supporter des courants constants de 400 A (avec des crêtes courtes pouvant atteindre 1 200 A) et des tensions allant jusqu’à 1 000 V, et d’être fiable à des températures ambiantes typiques de la batterie comprises entre -40 °C et +80 °C. Le principal défi consistait à réduire le plus possible la résistance de contact à chaque point de contact afin de limiter au maximum les pertes de puissance et la contrainte thermique, mais aussi à parvenir à une fiabilité à vie grâce à une résistance élevée aux vibrations conformément aux spécifications d’équipementiers du monde entier.
Gestion de la batterie
Le système de gestion de la batterie est le système électronique qui gère l’utilisation et la charge des cellules du bloc-batterie. Il empêche la batterie de fonctionner en dehors de ses limites de sécurité en surveillant les signaux de température et de tension des modules de cellules ainsi que les signaux de courant au niveau du bloc-batterie et en les transmettant aux éléments chargés d’équilibrer ou de contrôler l’environnement des modules de cellules.
Le système de gestion de la batterie est indispensable à des performances et une sécurité optimales de la batterie. Cette dernière doit en effet être très robuste et garantir un haut degré de précision et de fiabilité. Cependant, elle doit également être aussi compacte et légère que possible.
La connectivité est également un élément clé de la gestion de la batterie. Les signaux doivent être transmis au contrôleur de gestion de batterie (BMC), qui les traite et les transmet à son tour aux contrôleurs de gestion de cellules (CMC) afin d’équilibrer les cellules et de permettre un flux d’énergie contrôlé, par exemple pendant la charge.
Les composants électroniques du système BMS requièrent des systèmes de connexion très compacts, mais flexibles. Étant donné que le rapport entre les cellules de batterie et les contrôleurs de cellules varie en fonction des exigences de conception des batteries, telles que la capacité et la consommation énergétique du véhicule, les systèmes de connexion doivent présenter la flexibilité nécessaire pour permettre plusieurs permutations de configuration de connecteurs. Les connecteurs doivent également prendre en charge différents types de câbles, y compris les câbles FFC/FPC (câbles plats flexibles/imprimés) qui peuvent être acheminés autour de batteries compactes, à la géométrie complexe.
De plus, le système de connexion nécessite une « ligne de fuite » et une distance de sécurité suffisantes entre les broches afin d’éviter tout risque de court-circuit dû à la poussière ou à des arcs électriques. Les modules de batterie étant fournis scellés, les fabricants doivent être assurés que tous les connecteurs internes répondent à des spécifications strictes en matière de robustesse et de fiabilité automobile.
Solutions d’alimentation et de données à la une
Notre objectif est d’identifier les solutions de connectivité de la nouvelle génération de mobilité. Les couches d’alimentation et de réseau de données physiques, qui comprennent les câbles et les connecteurs, seront la pierre angulaire de la prochaine génération de véhicules connectés plus sûrs et plus écologiques que les consommateurs voudront acquérir, conduire ou utiliser en mode autonome.
Cela signifie que les réseaux de connectivité de données basse tension et les systèmes de transmission haute tension (HT) doivent fonctionner en parallèle, avec la plus grande fiabilité et en toute sécurité dans des architectures centralisées (« intelligentes ») de plus en plus intégrées.
Les technologies d’interconnexion, de commutation et de détection seront les catalyseurs des innovations qui permettront de concrétiser cette vision. Grâce à notre vaste gamme de technologies de pointe et à notre savoir-faire dans ces domaines, nous sommes dans une position idéale pour collaborer avec des entreprises spécialisées dans les technologies automobiles afin de cocréer les solutions de connectivité de la nouvelle génération de la mobilité.
Auteurs
- Qiong Sun, Vice President, Global Automotive, Hybrid & Electric Mobility Solutions
- Uwe Hauck, Director, Product Management, Automotive, Hybrid & Electric Mobility Solutions
- Luis Puras Trueba, Senior Manager, Product Management, Automotive, Hybrid & Electric Mobility Solutions
- Chris Yeadon, Senior Manager, Product Marketing, Automotive, Hybrid & Electric Mobility Solutions