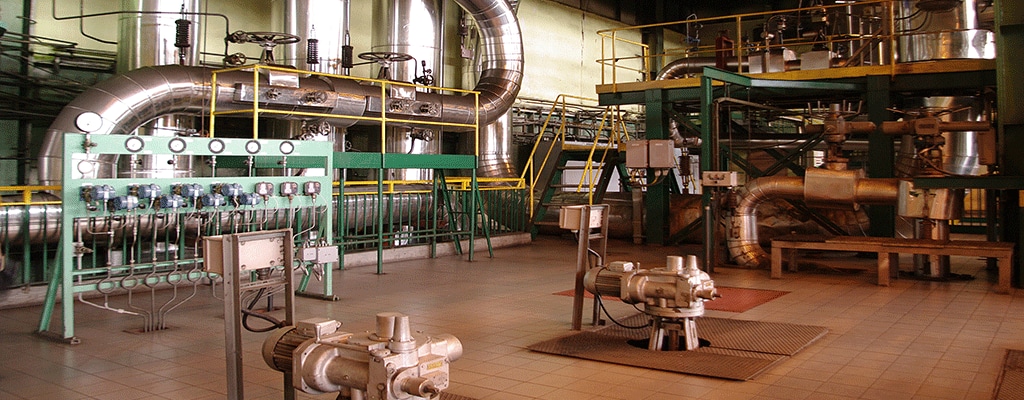
MECHANISCHE ENTSCHEIDUNGEN
Zu den wesentlichen Überlegungen bei der Auswahl eines LVDT zählt die mechanische Schnittstelle.
Beide LVDT-Wegsensortypen, ob mit freiem oder mit geführtem Kern, bieten den Vorteil der unendlichen Auflösung und sind in Ausführungen für den Einsatz in rauen Umgebungen erhältlich. LVDTs mit freiem Kern sind im Allgemeinen preiswerter und in vielen Ausführungen zu haben, aber auch anspruchsvoller im Einbau als Sensoren mit geführtem Kern. LVDTs mit feder- oder luftgeführtem Kern sind einfacher zu installieren, aber teurer und in weniger zahlreichen Ausführungen erhältlich. Neben diesen Unterschieden eignen sich manche Anwendungen einfach besser für einen LVDT mit freiem Kern, andere ziehen den größeren Nutzen aus einem LVDT mit geführtem Kern.
LVDT MIT FREIEM KERN
Das bewegliche Element eines LVDT mit freiem Kern ist ein hohler, magnetisch leitfähiger Anker: der sogenannte Kern. Der Kern ist in der Hohlbohrung der Spule axial frei verschiebbar und mechanisch an das Messobjekt gekoppelt. Die Bohrung gewährt dem Kern ein ausreichendes Radialspiel, sodass zur reibungsfreien Messung – und im Sinne einer praktisch unbegrenzten mechanischen Lebensdauer – kein physischer Kontakt zwischen Bohrung und Spule entsteht.
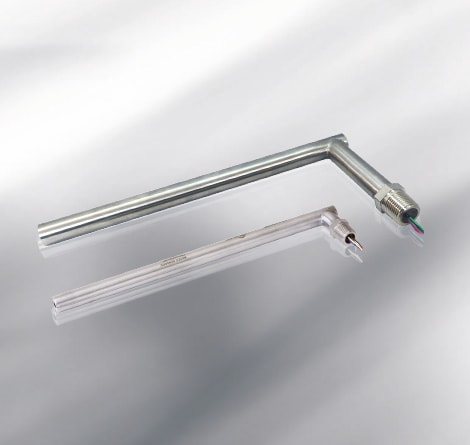
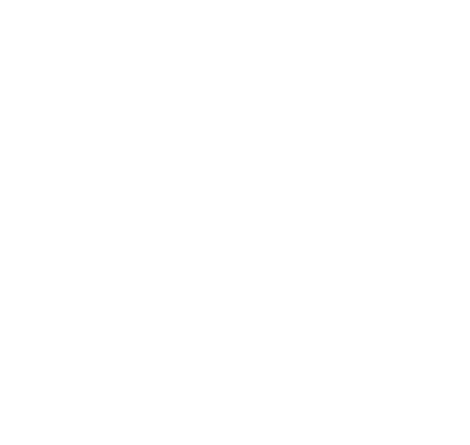
ANWENDUNGEN
LVDTs mit freiem Kern sind sehr vielseitig und robust und arbeiten berührungslos – das garantiert in Verbindung mit den richtigen Werkstoffen die langfristige Zuverlässigkeit in rauen widrigen Umgebungen. Aus der Tatsache, dass keine Reibung anfällt, ergibt sich eine höhere Wiederholpräzision und Auflösung. Aufgrund dieser Eigenschaften kommen LVDTs typischerweise in Systemen zum Einsatz, in denen Betriebskosten, Sicherheit und hohe Ausfallsicherheit Prioritäten sind, wie zum Beispiel bei Landeklappen oder Heißdampfventilen, in Unterwasseranwendungen und Kraftwerkanlagen. Andere Anwendungen, für die sich LVDTs mit freiem Kern anbieten, sind:
- Anwendungen, in denen das Messobjekt mechanisch mit der Referenzfläche oder dem Objekt gekoppelt ist (Ventile, Hydraulikzylinder, Stellglieder, Dehnungsmesseinrichtungen)
- Messbereiche größer als 4,00"
- Frequenzgang >10 Hz (Schwingungsmessungen)
- Kritische Messungen filigraner oder hochelastischer Materialien, die der Bewegung des Messobjekts wenig oder keinen mechanischen Widerstand entgegensetzen
LVDT MIT GEFÜHRTEM KERN
Federbelastete LVDTs, auch bekannt als Messtaster oder Wegaufnehmer, sind berührungslose, induktive Wegsensoren, entweder als LVDT oder Halbbrücke ausgeführt, mit einem beweglichen Anker, der einerseits unter dem Druck einer Feder steht und andererseits mit einem präzisionsgelagerten Schaft verbunden ist. Die meisten Messtaster verfügen über einen maximalen Messbereich von ±0,50 mm bis ±50,0 mm (±0,020 in bis ±2,00 in), die Auflösungen betragen Bruchteile von Mikrometern. Die Elektronik kann in die federbelastete Einheit integriert werden – so ist keine externe Elektronik erforderlich, und die mechanische Einrichtung des Sensors in einer automatisierten Umgebung wird vereinfacht und ist kostengünstig möglich.
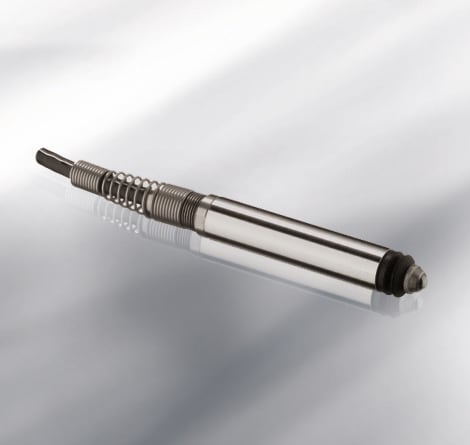
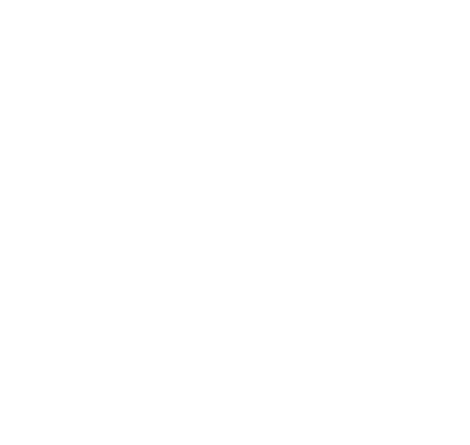
ANWENDUNGEN
Elektronische Messtaster werden üblicherweise zur Vermessung von gefertigten Teilen eingesetzt und dienen somit als wichtige Komponenten in Qualitätssicherungssystemen. Zielanwendungen, in denen das Messobjekt NICHT mechanisch mit der Referenzfläche gekoppelt ist:
- Schwerindustrie: Hermetisch abgedichtete Messtaster stellen eine Lösung für viele Messanwendungen in rauen Umgebungen dar.
- Hochpräzisionsmessung: Bei Hochpräzisions-Messtastern läuft ein gehärteter und geschliffener, nichtdrehender Messschaft in einer geraden Kugellagerschiene, die radiale Auslenkungen und Belastungen absolut minimiert. Dies resultiert in einer außerordentlichen Wiederholpräzision der Taster von 0,15 μm (0,000006 Zoll).
- Qualitätskontrolle in der Montage: Hier empfehlen sich Messtaster, die zur Messwertnahme luftunterstützt ausgefahren und danach federunterstützt zurückgefahren werden – so wird eine Beschädigung des Sensors beim Durchlauf des Produkts auf dem Band vermieden.
- Planheitsmessungen auf Platten
- Bewegung des Messobjekts quer zur Achse: z. B. Messung der Rundheit eines drehenden Teils
- Dickenmessungen
Federbelasteter LVDT – Automatisierung
Der federbelastete LVDT GHSAR 750 leistet akkurate Positionsmessung in verschiedensten Anwendungen – z. B. bei der Herstellung und Prüfung von Zylinderköpfen.